El diseño y la aplicación del canal caliente para fundición a presión de zinc
Pérdida de corredor de casting
Cualquiera que sepa sobre fundición a presión sabrá que el corredor o el material restante es parte de la fundición. Aunque no hay valor de beneficio, no se puede evitar en el proceso de producción. Esta parte del costo generalmente solo se calcula como una proporción fija del costo de la fundición. Al mismo tiempo, en vista de la reciclabilidad de las aleaciones de zinc, el método de tratamiento local más común es el retorno en tiempo real al horno de la máquina para su refundición. Debido a la necesidad de controlar los problemas de calidad, la industria acepta gradualmente el uso de hornos de fusión centrales para reciclar canales o productos de desecho (Figura 1). En cuanto a la escoria, las plantas de fundición a presión más grandes pueden reciclarlas por sí mismas y, en general, vender los materiales restantes a los proveedores de materias primas para obtener nuevos materiales. El precio de reciclaje local de los materiales de zinc es generalmente del 50 al 70% del de los materiales nuevos. Sin buenas condiciones ambientales, el manejo de la escoria puede fácilmente causar contaminación del aire.
Tomemos como ejemplo una máquina de fundición a presión de cámara caliente de 160 toneladas. Cada vez que produce al menos 150 gramos de canales (excluidos los pozos de desbordamiento), asumiendo tres turnos, el ciclo de producción es de 20 segundos, la tasa de utilización de la máquina es del 80% y la producción anual es El canal de boca puede llegar a 190 toneladas. Otro ejemplo: utilizando una máquina de 80 toneladas para producir 100 gramos de corredores cada vez, se hace la misma suposición pero el ciclo de producción se cambia a 12 segundos y la producción anual de corredores supera las 210 toneladas.
Se puede ver que el diseño del corredor afecta la importancia del costo.
Varios métodos de reciclaje
Entre los métodos de reciclaje, arrojar directamente el canal de regreso al horno es el método más simple y económico. El canal de flujo recién producido por fusión por reflujo no necesita ser precalentado, y el espacio de almacenamiento se reduce, pero es difícil controlar la calidad del material fundido, incluyendo más escoria, la temperatura del horno es difícil de controlar y la aleación. no se puede conocer la composición; lo que es más importante, se basa en la destreza del personal operativo, como la proporción de nuevos materiales y la observación de los cambios en el agua de la caldera, mientras que el personal coloca pozos de desbordamiento y flashes en el horno, no solo empeorará la situación, este método de derretir los desechos también los esconde. La alta tasa de defectos, la inestabilidad del diseño del molde y los parámetros de fundición a presión han impedido a los gerentes realizar mejoras efectivas. Este método no es adecuado para la producción de piezas fundidas con altos requisitos de calidad superficial y es difícil calcular con precisión el costo de la pérdida de canal.
Las boquillas de recuperación de horno central y los productos defectuosos se han vuelto populares en las plantas de fundición a presión con gran producción. Sus beneficios son muy obvios, es decir, el procesamiento centralizado de materiales reciclados puede mejorar la eficiencia del horno y controlar la calidad de la aleación. Si el metal fundido se alimenta directamente al horno desde el horno central, la temperatura del material de la máquina de fundición a presión se puede mantener estable y hay menos escoria. Si está equipado con control automático de alimentación, el cambio del nivel de líquido se puede minimizar. Los hornos centrales de fusión actualmente populares se dividen en varias categorías: hornos de crisol de hierro fundido con mayor capacidad, hornos de crisol de acero inoxidable y hornos sin crisol de tipo de fusión continua. El transporte de zinc líquido también se divide en varias categorías: hay transporte de material líquido tipo grúa aérea, transporte de horno de retención tipo carro (sin rieles o con orugas) (con dispositivo de alimentación) y dispositivo de transporte por gravedad de tipo artesa de retención, que conecta el horno y la central horno conectado. Su desventaja es que la inversión es relativamente grande, solo es adecuada para una sola aleación (el horno de crisol pequeño no se analiza aquí) y el taller ocupa un área grande, por lo que las plantas de fundición a presión pequeñas (menos de cinco máquinas) no son adecuado, y los viejos talleres son difíciles de transformar y cooperar. Por lo tanto, generalmente solo se vuelve a planificar cuando se construye una nueva planta. El uso de un pequeño horno de crisol para refundir el material del bebedero, debido a la falta de economías de escala, costará más que el horno central, por lo que no se utiliza como referencia para el cálculo.
Cálculo del costo de fusión
Simplemente use el horno de fusión central para calcular el costo de fusión del canal como referencia. Tomemos como ejemplo una empresa con cinco máquinas de fundición a presión de 80 o 160 toneladas. Suponiendo que la inversión del equipo es de 500,000, se divide en diez años. Cada año se procesan alrededor de 1,000 toneladas de materiales de reciclaje de canal (la situación real debe fundirse en proporción a los nuevos materiales, y es puramente conveniente calcular el costo de la refundición).
El costo de fusión por kilogramo de material de puerta es $ 0.93. Según el cálculo de las cinco máquinas anteriores, la producción anual de 1000 toneladas de toberas de canal implica casi 10 millones de yuanes. Si se incluye el reciclaje de productos defectuosos, esta cifra es aún más alarmante (por ejemplo, el peso medio de la fundición es de 100 gramos y la tasa de producto defectuoso es del 5%, el ciclo es de 12 segundos y la recuperación anual de productos defectuosos es de aproximadamente 53 montones). Aunque cuanto mayor sea la cantidad de procesamiento, menor será el costo de fusión, aquí no se calculan los costos de protección ambiental y estricto control de calidad. Se puede ver que el costo de la refundición en compuerta es bastante alarmante y la planta de fundición a presión debe minimizar el costo. Por lo tanto, cómo reducir el peso de la puerta es una clave importante para controlar los costos.
- Alquiler de ocupación de terreno 20.000 HKD
- Reparto de inversión en equipo de 50.000 HKD
- Costo de intereses HKD 5.000
- Mantenimiento y reparación HKD 25.000
- Tasa de fueloil (100 litros de residuos de aceite por tonelada · 2 dólares EE.UU. / litro) 200,000 HKD
- Tarifa de electricidad (1 USD / kWh) 30.000 HKD
- Salarios (incluidos los trabajadores operativos, el personal de gestión, el personal de control de calidad) 100.000 dólares de Hong Kong
- Pérdida de metal 5% (USD 10 / kg) 500,000 HKD
- Total: 930.000 HKD
Método de cálculo de prorrateo del costo del corredor
El costo de refinar la boquilla debe incluirse en el costo de producción de la pieza fundida. El método más común es multiplicar el material utilizado por un porcentaje fijo. Por ejemplo, si el precio de la materia prima es $ 10 / kg y el costo de fusión de la boquilla es el 3% del peso de la pieza fundida, se utilizarán $ 10.3 al calcular el precio del material de la pieza fundida. Aunque este método es simple, puede causar desviaciones en el cálculo de costos y ocultar el verdadero costo del reciclaje de las salidas de agua. Ahora puede usar el siguiente ejemplo para comparar:
- El peso neto de la fundición A es de 400 gramos y el peso del canal de la boquilla es de 100 gramos.
- El peso neto de la fundición B es de 400 gramos y el peso del canal de la boquilla es de 250 gramos.
Si se calcula con un porcentaje fijo:
- El costo de la fundición A y la fundición B debe ser el mismo ($ 10.3 x 0.4) = $ 4.12.
Si se calcula por el costo de recuperación real:
- El casting A debería ser ($ 10 x 0.4 + $ 0.93 x 0.1) = $ 4.093
- El casting B debería ser ($ 10 x 0.4 + $ 0.93 x 0.25) = $ 4.233
Esta diferencia puede parecer pequeña, pero con 20 segundos como ciclo de producción, la tasa de utilización de la máquina es del 80% y la producción es en tres turnos, cada máquina produce 1,261,440 veces al año. La diferencia es la siguiente:
- Costo de la boquilla del corredor Fundición A Fundición B
- Diferencia Método de relación fija HKD 5.197.132 HKD 5.197.132 HKD 0
- Método de costo real HK $ 5.163.074 HK $ 5.339.675 HK $ 176.601
- Diferencia HK $ 34.058 HK $ 142.543
Si se usa el método de proporción fija, el costo de la fundición A y B es el mismo, pero de hecho el costo de la fundición B es mayor. Se puede ver en este caso que el uso del método de proporción fija para calcular la fundición B no solo subestima el costo de producción, sino que también alienta indirectamente a los diseñadores a no reducir el peso del canal de la boquilla como objetivo, y debe promover la aplicación de la actual método de costo (ver la tabla a continuación).
Para reducir el peso de la puerta, es más común utilizar un diseño de puerta corta (boquilla corta) y reducir el grosor de la plantilla. Utiliza una boquilla de máquina más larga (generalmente 20 mm más larga de lo normal), combinada con un diseño de molde de puerta de cavidad profunda para reducir el peso de la puerta. El siguiente es un nuevo diseño de canal de fundición a presión de cámara caliente.
Diseño de canal de fundición a presión de cámara caliente
El corredor de fundición a presión es el camino del metal fundido que fluye desde la boquilla hasta la cavidad del molde. Está compuesto por las ramas del bebedero y el corredor. Debido a la necesidad de sujetar las piezas fundidas y facilitar el desmoldeo, el bebedero debe tener una inclinación. Al mismo tiempo, el bloque divisor de la plantilla móvil puede reducir el grosor del bebedero; la adición de un canal de agua de enfriamiento en el bloque divisor facilita el equilibrio del calor del molde, acorta el tiempo de enfriamiento y saca la pieza fundida y la expulsa. Un estudio realizado por el CSIRO australiano a principios de la década de 1970 encontró que, con errores aceptables, el líquido de aleación de zinc se puede resumir de la siguiente manera en el caso de la fundición a presión:
El líquido se comporta como un líquido incompresible
Cumplir con los principios generales de la mecánica de fluidos.
El alto número de Reynold indica que el proceso de flujo es turbulento.
Según los resultados de la investigación anterior, el estado de flujo ideal del metal fundido debería ser:
1. La sección del corredor es circular.
Dado que la relación circunferencia / área es la más baja, la resistencia de la superficie de la tubería de sección transversal circular es la más baja, por lo que la pérdida de presión también es la más baja. En comparación con la misma área de sección transversal trapezoidal, la periferia se reduce en más del 20%.
2. La tubería de flujo es recta
Las tuberías dobladas generarán un flujo sesgado, mezclarán burbujas en la masa fundida y causarán pérdida de presión. Especialmente cuando la relación entre el radio de curvatura y el diámetro de la tubería es inferior a 1, la pérdida de presión aumenta rápidamente.
3. El perfil del canal de flujo se contrae gradualmente en términos de flujo de líquido.
El cambio rápido del perfil de la tubería, ya sea que se vuelva más grande o más pequeño, causará una gran pérdida de presión y corrientes parásitas. La mejor solución es reducir gradualmente el perfil para compensar la pérdida de resistencia causada por la superficie de la tubería.
Conserve la fuente y la dirección de este artículo para reimprimir:El diseño y la aplicación del canal caliente para fundición a presión de zinc
Minghe Casting Company se dedica a fabricar y proporcionar piezas de fundición de calidad y alto rendimiento (la gama de piezas de fundición a presión de metal incluye principalmente Fundición a presión de pared delgada,Fundición a presión en cámara caliente,Fundición a presión de cámara fría), Servicio redondo (servicio de fundición a presión,Mecanizado cnc,Fabricación de moldes, Tratamiento de superficie) .Cualquier fundición a presión de aluminio personalizada, fundición a presión de magnesio o Zamak / zinc y otros requisitos de fundición pueden contactarnos.
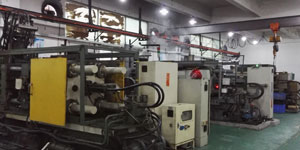
Bajo el control de ISO9001 y TS 16949, todos los procesos se llevan a cabo a través de cientos de máquinas de fundición a presión avanzadas, máquinas de 5 ejes y otras instalaciones, que van desde desintegradores hasta lavadoras Ultra Sonic.Minghe no solo cuenta con equipos avanzados, sino que también cuenta con profesionales equipo de ingenieros, operadores e inspectores experimentados para hacer realidad el diseño del cliente.
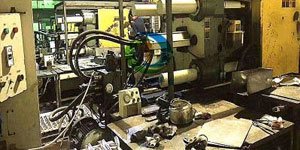
Fabricante por contrato de piezas de fundición a presión. Las capacidades incluyen piezas de fundición a presión de aluminio de cámara fría de 0.15 libras. a 6 libras, configuración de cambio rápido y mecanizado. Los servicios de valor agregado incluyen pulido, vibración, desbarbado, granallado, pintura, enchapado, revestimiento, ensamblaje y herramientas. Los materiales con los que se trabaja incluyen aleaciones como 360, 380, 383 y 413.
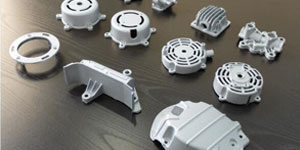
Asistencia en el diseño de fundición a presión de zinc / servicios de ingeniería simultáneos. Fabricante personalizado de piezas fundidas de zinc de precisión. Se pueden fabricar piezas de fundición en miniatura, piezas de fundición a presión de alta presión, piezas de fundición de moldes de deslizamiento múltiple, piezas de fundición de moldes convencionales, piezas de fundición unitaria e independiente y piezas de fundición selladas en cavidades. Las piezas fundidas se pueden fabricar en longitudes y anchos de hasta 24 pulgadas con una tolerancia de +/- 0.0005 pulgadas.
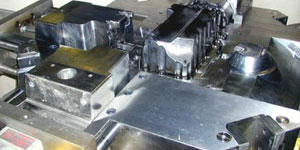
Fabricante certificado por ISO 9001: 2015 de magnesio fundido a presión, las capacidades incluyen fundición a presión de magnesio a alta presión de hasta 200 toneladas de cámara caliente y 3000 toneladas de cámara fría, diseño de herramientas, pulido, moldeado, mecanizado, pintura en polvo y líquida, control de calidad completo con capacidades de CMM , montaje, embalaje y entrega.
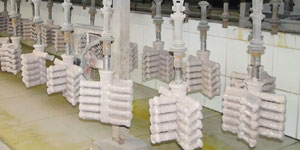
Certificado ITAF16949. El servicio de casting adicional incluye fundición de inversión,moldeo en arena,Fundición por gravedad, Fundición de espuma perdida,Fundición centrífuga,Fundición al vacío,Fundición de molde permanenteLas capacidades incluyen EDI, asistencia de ingeniería, modelado de sólidos y procesamiento secundario.
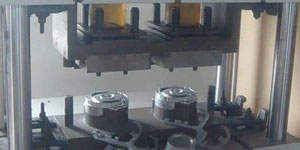
Industrias de fundición Estudios de casos de piezas para: automóviles, bicicletas, aeronaves, instrumentos musicales, embarcaciones, dispositivos ópticos, sensores, modelos, dispositivos electrónicos, carcasas, relojes, maquinaria, motores, muebles, joyas, plantillas, telecomunicaciones, iluminación, dispositivos médicos, dispositivos fotográficos, Robots, Esculturas, Equipos de sonido, Equipos deportivos, Herramientas, Juguetes y más.
¿Qué te podemos ayudar a hacer a continuación?
∇ Ir a la página de inicio para Fundición a presión China
→Piezas de fundición-Descubre lo que hemos hecho.
→ Consejos Ralated Acerca de Servicios de fundición a presión
By Fabricante de fundición a presión Minghe | Categorías: Artículos útiles |Material Tags: Fundición de aluminio, Fundición de zinc, Fundición de magnesio, Fundición de titanio, Fundición de acero inoxidable, Fundición de latón,Fundición de bronce,Casting de video,Historia de la empresa,Fundición a presión de aluminio | Comentarios desactivados