La tendencia de desarrollo de las piezas de fundición de automóviles y su tecnología de fabricación
La fundición es uno de los métodos de formación de metales más antiguos. Aproximadamente del 15% al 20% de las piezas de automóvil son piezas fundidas producidas por diferentes métodos de fundición. Estas piezas fundidas son principalmente componentes clave del sistema de energía e importantes componentes estructurales. En la actualidad, la tecnología de producción de piezas de fundición de automóviles en los países desarrollados en las industrias del automóvil europea y estadounidense es avanzada, con buena calidad de producto, alta eficiencia de producción y baja contaminación ambiental. La fundición de materias primas y auxiliares se ha serializado y estandarizado, y todo el proceso de producción ha sido mecanizado, automatizado e inteligente. Estos países generalmente utilizan tecnología digital para mejorar el nivel de diseño del proceso de fundición. La tasa de rechazo de casting es de aproximadamente 2% a 5%, y se ha establecido un sistema de servicio transnacional y se ha implementado soporte técnico de red. Por el contrario, aunque la producción de piezas de fundición de automóviles en mi país es relativamente grande, la mayoría de ellas son piezas de fundición negras con un valor agregado y contenido técnico relativamente bajos, y una estructura relativamente simple, que dista mucho del nivel extranjero. Este artículo analiza principalmente la dirección de desarrollo de las piezas fundidas de automóviles y la tecnología del automóvil a partir de las necesidades de desarrollo del ahorro de energía del automóvil y la protección del medio ambiente.
Diseño integrado de piezas de fundición de automóviles
Con los crecientes requisitos para la conservación de energía y la protección ambiental de los automóviles y la reducción de los costos de producción, aprovecharemos al máximo las ventajas de la fundición para realizar la fundición de piezas integradas a través de un diseño razonable y optimización estructural de varias piezas formadas por estampado, soldadura, forja y fundición. El conformado puede reducir efectivamente el peso de las piezas y reducir los procesos de procesamiento innecesarios, logrando así piezas ligeras y de alto rendimiento.
La forma principal de la carcasa del eje monolítico de fundición común es que los tubos de acero sin costura se presionan en los dos extremos de la carcasa del eje como manguitos de medio eje y se fijan con pasadores para formar el conjunto de la carcasa del eje. Con el fin de mejorar aún más la resistencia y rigidez de la carcasa del eje y simplificar el proceso, FAW Group ha desarrollado una carcasa de eje integrada en la que las mangas del eje (las partes en ambos lados de la carcasa del eje en la Figura 1) se moldean directamente en el carcasa del eje. El procesamiento es difícil, la reducción de costos es mayor, la estructura de la carcasa del eje tiende a ser simple y la rigidez de la carcasa del eje es mejor, se puede convertir en una forma compleja e ideal, se puede cambiar el grosor de la pared, se puede obtener una distribución ideal de la tensión y su resistencia y La rigidez es grande, trabaja de forma fiable. Debido a la integración del manguito del eje, el tamaño de la fundición aumenta significativamente. La longitud de la pieza fundida es de 2 mm y el peso de una pieza supera los 258 kg. En vista de las características de esta fundición integrada, la empresa ha establecido una línea de producción dedicada para garantizar la producción.
La tendencia de desarrollo de la integración de piezas de fundición de automóviles es más obvia en el desarrollo de piezas de fundición de aleaciones no ferrosas. Para aprovechar al máximo las características del proceso de fundición que puede lograr la producción de fundiciones de estructuras complejas, se ha diseñado un diseño integrado de fundiciones de alta presión, como paneles interiores de puertas, marcos de asientos, marcos de paneles de instrumentos, marcos frontales y cortafuegos. emergió. Las dimensiones son significativamente mayores que las que se producen actualmente. Para las piezas fundidas, se requiere una máquina de fundición a presión con un tonelaje de 4 a 000 toneladas o incluso más para la producción.
Ligereza de las piezas de fundición de automóviles
Con la premisa de garantizar la resistencia y la seguridad del automóvil, reduzca el peso en vacío del automóvil tanto como sea posible para lograr un peso ligero, mejorando así la potencia del automóvil, reduciendo el consumo de combustible y reduciendo la contaminación del escape. Por cada 100 kg de reducción del peso en vacío del vehículo, el consumo de combustible por cada 100 kilómetros se puede reducir de 0.3 a 0.6 L. Si el peso del vehículo se reduce en un 10%, la eficiencia del combustible se puede aumentar entre un 6% y un 8%. Con la necesidad de protección ambiental y ahorro de energía, el peso ligero de los automóviles se ha convertido en la tendencia del desarrollo automovilístico mundial, y el peso ligero de las piezas de fundición de automóviles también se ha convertido en una de las direcciones de desarrollo importantes de las piezas de fundición de automóviles.
Diseño ligero de piezas de fundición de automóviles
Debido a la necesidad del factor de seguridad general de las piezas fundidas, el diseño de igual espesor es uno de los principales métodos de diseño para las piezas fundidas de automóviles. Sin embargo, la principal desventaja del diseño de igual espesor es que el rendimiento estructural no se puede utilizar por completo y aumenta el peso de la pieza fundida. Utilice análisis CAE, optimización de topología y otros métodos para optimizar el diseño de las partes, de modo que los valores de tensión de las partes de las partes estén cerca, es decir, el espesor de pared de cada parte sea inconsistente y las partes con pequeños las fuerzas se adelgazan o son innecesarias para reducir las piezas. el peso de. Teniendo en cuenta que el moldeado por colada puede realizar el moldeado de coladas de estructuras complejas, se pueden realizar varias secciones transversales de forma irregular. Al diseñar, utilice CAE o la optimización de topología para realizar análisis de tensión en los componentes. De acuerdo con la distribución de la fuerza, determine la forma de la pieza y el grosor del material de la pieza específica. Al reforzar, cavar agujeros y espesar las piezas fundidas, el peso de las piezas se puede reducir considerablemente.
Piezas de fundición de automóviles de aleación ligera
El uso de materiales de aleación ligera como el aluminio y el magnesio es actualmente la principal medida de reducción de peso adoptada por los fabricantes de automóviles en varios países. La densidad del aluminio es solo 1/3 de la del acero y tiene una excelente resistencia a la corrosión y ductilidad. El magnesio tiene una densidad más baja, solo 2/3 de la del aluminio, y tiene una fluidez excelente en condiciones de fundición a alta presión. La resistencia específica (relación resistencia / masa) del aluminio y el magnesio es bastante alta, lo que juega un papel decisivo en la reducción del peso propio y la mejora de la eficiencia del combustible. La creciente competitividad de la industria automotriz estadounidense en los últimos dos años está estrechamente relacionada con su adopción a gran escala de fundiciones estructurales de aluminio y magnesio y fundiciones integradas.
La nueva serie 5 lanzada por la empresa alemana BMW está equipada con la última generación de bloque motor de seis cilindros en línea compuesto de magnesio-aluminio, el peso se reduce en 10 kg en comparación con la generación anterior, lo que mejora enormemente el rendimiento y el combustible. economía. Sin embargo, debe tenerse en cuenta que el precio de las materias primas para las aleaciones ligeras como el aluminio y el magnesio es mucho más alto que el de los materiales de acero, lo que limita su aplicación más amplia en la industria automotriz. Sin embargo, a pesar del precio relativamente alto de las materias primas, el consumo actual de fundición de magnesio y aluminio para bicicletas ha ido aumentando año tras año. Por un lado, el progreso tecnológico ha compensado el aumento de costes. Por otro lado, la competencia del mercado ha obligado a los fabricantes de automóviles a reducir las ganancias y adoptar aleaciones más ligeras. Sin embargo, para aumentar en gran medida la cantidad de aleaciones ligeras y reducir el precio de compra de los lingotes de magnesio y aluminio, el desarrollo de tecnología avanzada de conformado es una de las claves.
Alto rendimiento de los materiales de fundición de automoción
Mejorar el rendimiento del material, de modo que el peso unitario de la pieza pueda soportar cargas más altas, es uno de los métodos para reducir eficazmente el peso de la pieza fundida. Las fundiciones estructurales de tipo soporte representan una gran proporción de las fundiciones de automóviles, por lo que el desarrollo de sus fundiciones se ha convertido en uno de los focos de atención. A través del tratamiento térmico y otras medidas, se cambia la microestructura del material, mejorando así la resistencia, rigidez o tenacidad de las piezas, lo que puede reducir eficazmente el peso de las piezas.
El hierro dúctil austemperado no solo tiene mayor resistencia que los materiales de acero fundido ordinarios, sino que también tiene una densidad más baja que el acero. Su densidad es de 7.1 g / cm3, mientras que la densidad del acero fundido es de 7.8 g / cm3, material muy recomendado en los últimos años. . Adopta hierro dúctil austemperado, que es un 10% más ligero que las piezas fundidas de acero con el mismo tamaño de piezas fundidas. Dongfeng Motor Corporation ha llevado a cabo un trabajo de verificación ligero en un cierto tipo de vehículo comercial utilizando hierro dúctil austemperado en lugar de fundiciones de acero. En vista de las características de alta resistencia de las piezas de hierro dúctil austemperado, se rediseñaron 14 piezas de suspensión en el foro de expertos. En términos generales, la sustitución de material de las piezas de fundición de automóviles suele acompañar al diseño ligero de las piezas.
En las fundiciones de aleación de aluminio y aleación de magnesio, se utilizan en su lugar materiales de alta resistencia y alta tenacidad. Sobre la base de la reducción de peso de aleación ligera original, se utilizan materiales de alto rendimiento para reducir aún más el peso. En su lugar, General Motors de los Estados Unidos utiliza una aleación AE44 de alto rendimiento. La aleación de aluminio original utiliza fundición a alta presión para producir el bastidor auxiliar, lo que reduce aún más el peso de la aleación de aluminio en 6 kg.
Digitalización del desarrollo de fundición automotriz
La combinación integral de desarrollo de fundición automotriz y tecnología digital puede mejorar significativamente el nivel de tecnología de fundición y acortar el diseño del producto y el ciclo de producción de prueba. En la actualidad, la tecnología de fabricación digital se ha utilizado ampliamente en el desarrollo de piezas de fundición para automóviles. En la etapa del diseño de la estructura de fundición y el diseño del proceso de fundición, el software de diseño 3D como Pro / E, CATIA y UG se ha utilizado ampliamente, y algunas empresas de fundición avanzadas han realizado un diseño sin papel. Software como MAGMA, ProCAST y Huazhu CAE se han utilizado ampliamente para simular el proceso de solidificación, la microestructura, la segregación de la composición y las propiedades de los materiales de las piezas de fundición de automóviles. También puede analizar el campo de velocidad, el campo de concentración, el campo de temperatura y la fase en el proceso de fundición. La simulación de campos, campos de tensión, etc., puede garantizar que el plan de proceso se optimice antes de la producción en masa.
Con el fin de satisfacer las necesidades de desarrollo rápido de piezas de fundición de automóviles, basado en el diseño y desarrollo de CAD / CAE, la RP (tecnología de creación rápida de prototipos) se ha utilizado ampliamente para la producción de prueba rápida de piezas de fundición de automóviles. Una vez obtenidos los datos CAD / CAE originales, se adopta el método capa por capa para obtener el prototipo de la pieza fundida o el prototipo del molde necesario para formar la pieza fundida mediante unión, sinterización o sinterización. Las primeras pueden ser muestras de fundición producidas de prueba mediante fundición a la cera perdida, fundición de yeso y otros métodos, mientras que la segunda se puede utilizar directamente como molde para fabricar núcleos de arena, y las fundiciones se pueden verter a través del modelado de ensamblaje de núcleos. Además, el método de sinterización por láser de polvo (SLS) se puede utilizar para completar directamente la producción de núcleos de arena y moldes de arena, a fin de obtener los moldes de arena necesarios para la producción de prueba de piezas fundidas. Para moldes exteriores con estructuras relativamente simples, las máquinas herramienta CNC también se pueden utilizar para procesar CAM con plásticos mecanizables para obtener la caja de machos y el patrón requeridos para la producción de prueba de piezas fundidas, o procesar directamente el bloque de arena para obtener el molde de arena del molde exterior. directamente.
En términos generales, la tecnología digital ha penetrado en todos los aspectos del diseño, el desarrollo y la producción de pruebas de fundición, mejorando efectivamente la velocidad y la eficiencia del desarrollo de la fundición. El principal problema en la actualidad es que las tecnologías digitales de diseño, análisis y fabricación rápida son independientes entre sí. Cuando el proceso de desarrollo se transforma de una etapa a otra, también se requiere un trabajo de conversión de datos bastante tedioso. Se espera que en el futuro, se pueda desarrollar una plataforma de interfaz de datos unificada para la tecnología digital aplicada en todos los aspectos del desarrollo de fundición, y se puedan establecer estándares de conversión de datos estandarizados para lograr una conversión de datos perfecta entre diferentes software, a fin de aumentar aún más la velocidad de desarrollo de las piezas fundidas.
Tecnología de producción de piezas fundidas de estructura compleja de paredes delgadas
Con el desarrollo de la industria del automóvil y la demanda de ahorro de energía y reducción de emisiones, las piezas de automóviles son cada vez más ligeras. A través del diseño de paredes delgadas, la reducción de peso es una dirección de desarrollo importante para los bloques de motor. Tomemos como ejemplo a FAW Casting Co., Ltd. para la producción de bloques de cilindros de hierro fundido de FAW-Volkswagen. El bloque de cilindros 06A producido anteriormente tiene un grosor de pared de 4.5 mm ± 1.5 mm, y el bloque de cilindros EA111 tiene un grosor de pared de 4 mm ± 1 mm. El bloque de cilindros EA888Evo2 producido en serie actual tiene un grosor de pared de 4 mm ± 1 mm. 3.5 mm ± 0.8 mm, la estructura del producto del bloque de cilindros EA888Gen.3 de próxima generación es más compleja, su espesor de pared es de solo 3 mm ± 0.5 mm, actualmente es el bloque de cilindros de hierro fundido gris más delgado. Aunque existen problemas con núcleos rotos, núcleos flotantes y grandes fluctuaciones de espesor de pared en la producción en masa, al controlar la calidad de los núcleos de arena y la arena de moldeo, el proceso de vertido horizontal ampliamente utilizado aún puede cumplir con los requisitos de producción de los cilindros EA888Evo2. Pero no puede cumplir con los requisitos de producción del bloque de cilindros EA888Gen.3, por lo que se debe adoptar todo el proceso de fundición vertical del ensamblaje del núcleo.
Tecnología de fabricación de grandes piezas estructurales de aleación de aluminio y magnesio
Con los crecientes requisitos para el ahorro de energía, la protección del medio ambiente y la reducción de los costes de los componentes, las fundiciones estructurales a gran escala de aleación de aluminio y magnesio se han convertido en una importante tendencia de desarrollo, y su tecnología de fabricación también se ha convertido en un foco de desarrollo actual. En la actualidad, las principales tecnologías de producción de piezas estructurales de aleación de aluminio y magnesio a gran escala incluyen la fundición a alta presión, la fundición por compresión y la fundición a baja presión. Debido a la alta eficiencia de producción de la fundición a alta presión y la buena calidad del producto, se ha convertido en el principal proceso de producción en la actualidad. El desarrollo de su tecnología de fabricación se centra principalmente en el fácil arrastre de gas durante el proceso de fundición a alta presión y la formación de poros dentro de las fundiciones, lo que no puede mejorar el problema del tratamiento térmico.
La empresa Fulai de Alemania desarrolló el proceso de fundición por succión y presión negativa al vacío, todo el proceso de fundición a presión se lleva a cabo a alto vacío (menos de 30 mbar). El metal fundido pasa a través del molde, la cámara de presión y la tubería de succión en un estado de vacío y es succionado del horno por la tubería de succión sin oxidarse, y el vapor del agente de desmoldeo también es descargado por el sistema de vacío. Las principales características del proceso de colada por succión y presión negativa al vacío mencionado anteriormente son: cuando se inicia el vertido cuantitativo, todo el sistema se encuentra en un estado de alto vacío; en el proceso de vertido cuantitativo, el gas de la cavidad y el metal fundido pueden descargarse eficazmente; durante el proceso de vertido No hay oxidación del metal fundido; no hay pérdida de calor durante el proceso de vertido, y se puede usar una temperatura de vertido más baja para verter, y el llenado de flujo laminar no perturbado se puede realizar bajo monitoreo en tiempo real. El proceso anterior se ha aplicado con éxito a la producción en masa de piezas fundidas estructurales de automóviles del Auto Expert Forum, proporcionando métodos y procesos de conformado avanzados para la aplicación de piezas fundidas de aleación ligera de alta calidad.
La empresa suiza Buhler ha desarrollado un sistema de vacío de doble circuito para la producción de fundiciones estructurales. Esta tecnología de producción se denomina tecnología de producción estructural. El uso de tecnología de producción estructural puede incrementar la velocidad de aspiración, obteniendo así condiciones de producción estables y mejorando significativamente la fundición a presión La calidad de las piezas. Como se muestra en la Fig. 5, el puerto de extracción de aire de un circuito en el sistema de vacío de doble circuito está dispuesto en el extremo superior de la cámara de presión y se usa principalmente para extraer aire en la cámara de presión. Comienza cuando el émbolo de inyección se mueve hacia adelante para sellar el puerto de vertido y se cierra cuando el émbolo está a punto de sellar el puerto de succión. El otro ajuste del circuito es el mismo que el del proceso de vacío tradicional y se utiliza principalmente para extraer aire de la cavidad. En la actualidad, la tecnología se ha aplicado con éxito a la fabricación de torres de amortiguación integradas de aleación de aluminio, paneles interiores de puertas y rieles de carrocería de automóviles de pasajeros.
Tecnología de formación de fundición de precisión para piezas fundidas
La comúnmente conocida como fundición de precisión de piezas de fundición de automóviles se refiere principalmente a la tecnología de fundición de inversión y espuma perdida. Con el desarrollo de la tecnología de formación de fundición de automóviles, la formación de precisión de fundición se refiere a un tipo de método de formación de fundición. Las piezas fundidas producidas por este tipo de método de formación se pueden usar directamente sin cortar o menos cortar. Con los crecientes requisitos para la precisión dimensional de las piezas fundidas, la tecnología de fundición de precisión se ha desarrollado rápidamente en los últimos años, y han surgido una serie de nuevos métodos de fundición, como la fundición en arena de precisión, la fundición de espuma perdida, la fundición a presión controlada y la fundición a presión. El método de fundición Cosworth es un método desarrollado por el Reino Unido que utiliza un conjunto de núcleo de arena de circonio y una bomba electromagnética para controlar el vertido. Se ha utilizado con éxito en la producción en masa de bloques de cilindros de aleación de aluminio y han aparecido muchas variantes de proceso, como el uso de vertido a baja presión en lugar de procesos electromagnéticos como el vertido con bomba. Este tipo de método de fundición puede producir cilindros de aleación de aluminio con un espesor de pared de 3.5 a 4.0 mm, que es el proceso representativo actual de fundición en arena de precisión.
El proceso de fundición de espuma perdida se inventó en 1965, y las principales piezas de fundición para automóviles producidas son bloques de cilindros, culatas de cilindros, tubos de admisión y escape y otros productos, y han formado una producción a gran escala. Desde la introducción de la tecnología de fundición de espuma perdida en la década de 1990 en el siglo XX, mi país ha comenzado a tomar forma y ha sido promovido por el estado como la alta y nueva tecnología más utilizada para transformar la industria de la fundición tradicional. En la actualidad, hay tres procesos de fundición de precisión por inversión en mi país: caparazón de silicato de sodio, capa compuesta y capa de sol de sílice. Entre ellos, la calidad de la superficie de la fundición utilizada en la producción de cáscaras de sol de sílice para productos de automóviles puede alcanzar Ra 20 μm, y la precisión dimensional puede alcanzar CT1.6. Grado, el grosor mínimo de la pared puede ser de 4 ~ 0.5 mm. Dongfeng Motor Precision Casting Co., Ltd. adopta el proceso de fabricación de carcasa compuesta de sol de sílice + vidrio de agua para producir piezas fundidas integradas de estructura compleja, lo que reduce significativamente los costos de producción. La tendencia de desarrollo del proceso de moldeo por tecnología de fundición por inversión es que las piezas de fundición se acercan cada vez más al producto final, y la complejidad y la calidad de los productos son cada vez más altas. La aplicación de CAD, CAM y CAE se ha convertido en la principal tecnología de desarrollo de productos, y la cooperación profesional comenzó a aparecer.
La fundición al vacío, la fundición a presión llena de oxígeno, la fundición a presión tixotrópica o reológica de metales semisólidos y otros métodos de proceso desarrollados sobre la base del proceso de fundición a alta presión están diseñados para eliminar defectos de fundición, mejorar la calidad interna y ampliar el rango de aplicación de las fundiciones a presión. . Durante el proceso de fundición por compresión, la masa fundida se llena y solidifica bajo presión, lo que tiene las ventajas de suavidad, ausencia de salpicaduras de metal, menor pérdida de oxidación del metal líquido, ahorro de energía, operación segura y reducción de orificios de fundición y otros defectos. Se utiliza en bastidores auxiliares de aleación de aluminio, etc. El desarrollo y la aplicación de fundiciones de aleación de aluminio de alto rendimiento se han utilizado ampliamente.
El crecimiento continuo de la producción de automóviles requiere con urgencia el desarrollo de la producción de fundición en la dirección de alta calidad, excelente rendimiento, forma casi neta, múltiples variedades, bajo consumo y bajo costo. Porque entre el 15% y el 20% de las piezas de un vehículo completo son piezas fundidas. Esto requiere que la industria de la fundición aplique continuamente varias tecnologías nuevas y nuevos materiales para mejorar el nivel general de fundición. La tecnología de formación de piezas de fundición de precisión de piezas de fundición puede cumplir los requisitos mencionados anteriormente de piezas de fundición de automóviles, y su aplicación también cubrirá diferentes procesos de producción de piezas de fundición de automóviles.
Conclusión
Para adaptarse a los requisitos cada vez más estrictos de las normas de protección del medio ambiente, los automóviles se están desarrollando en la dirección de un peso más ligero. Por cada 10% de reducción del peso del vehículo, el consumo de combustible se puede reducir en un 5.5%, la economía de combustible se puede aumentar entre un 3% y un 5% y las emisiones se pueden reducir en aproximadamente un 10%. La aplicación de fundiciones de aluminio-magnesio y otras aleaciones no ferrosas, el desarrollo de fundiciones integradas de estructura compleja a gran escala y la aplicación generalizada de la tecnología de moldeado de precisión de fundición son las principales formas de lograr fundiciones ligeras para automóviles. Por lo tanto, se requiere realizar la investigación, el desarrollo y la producción de piezas fundidas de automóviles mediante materiales de fundición de alto rendimiento y una amplia aplicación de equipos de automatización sobre la base del uso extensivo de la tecnología digital para satisfacer las necesidades de la industria automotriz moderna.
Conserve la fuente y la dirección de este artículo para reimprimir: La tendencia de desarrollo de las piezas de fundición de automóviles y su tecnología de fabricación
Minhe Empresa de fundición a presión se dedican a fabricar y proporcionar piezas de fundición de calidad y alto rendimiento (la gama de piezas de fundición a presión de metal incluye principalmente Fundición a presión de pared delgada,Fundición a presión en cámara caliente,Fundición a presión de cámara fría), Servicio redondo (servicio de fundición a presión,Mecanizado cnc,Fabricación de moldes, Tratamiento de superficie) .Cualquier fundición a presión de aluminio personalizada, fundición a presión de magnesio o Zamak / zinc y otros requisitos de fundición pueden contactarnos.
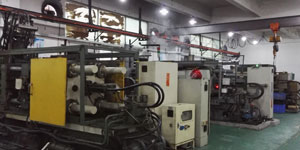
Bajo el control de ISO9001 y TS 16949, todos los procesos se llevan a cabo a través de cientos de máquinas de fundición a presión avanzadas, máquinas de 5 ejes y otras instalaciones, que van desde desintegradores hasta lavadoras Ultra Sonic.Minghe no solo cuenta con equipos avanzados, sino que también cuenta con profesionales equipo de ingenieros, operadores e inspectores experimentados para hacer realidad el diseño del cliente.
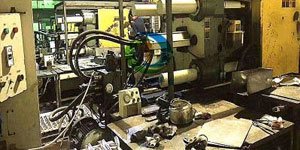
Fabricante por contrato de piezas de fundición a presión. Las capacidades incluyen piezas de fundición a presión de aluminio de cámara fría de 0.15 libras. a 6 libras, configuración de cambio rápido y mecanizado. Los servicios de valor agregado incluyen pulido, vibración, desbarbado, granallado, pintura, enchapado, revestimiento, ensamblaje y herramientas. Los materiales con los que se trabaja incluyen aleaciones como 360, 380, 383 y 413.
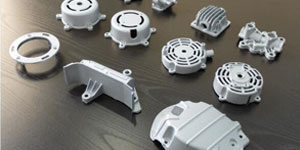
Asistencia en el diseño de fundición a presión de zinc / servicios de ingeniería simultáneos. Fabricante personalizado de piezas fundidas de zinc de precisión. Se pueden fabricar piezas de fundición en miniatura, piezas de fundición a presión de alta presión, piezas de fundición de moldes de deslizamiento múltiple, piezas de fundición de moldes convencionales, piezas de fundición unitaria e independiente y piezas de fundición selladas en cavidades. Las piezas fundidas se pueden fabricar en longitudes y anchos de hasta 24 pulgadas con una tolerancia de +/- 0.0005 pulgadas.
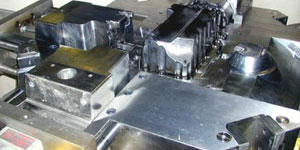
Fabricante certificado por ISO 9001: 2015 de magnesio fundido a presión, las capacidades incluyen fundición a presión de magnesio a alta presión de hasta 200 toneladas de cámara caliente y 3000 toneladas de cámara fría, diseño de herramientas, pulido, moldeado, mecanizado, pintura en polvo y líquida, control de calidad completo con capacidades de CMM , montaje, embalaje y entrega.
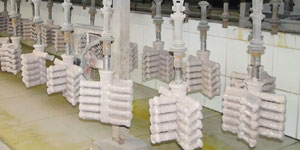
Certificado ITAF16949. El servicio de casting adicional incluye fundición de inversión,moldeo en arena,Fundición por gravedad, Fundición de espuma perdida,Fundición centrífuga,Fundición al vacío,Fundición de molde permanenteLas capacidades incluyen EDI, asistencia de ingeniería, modelado de sólidos y procesamiento secundario.
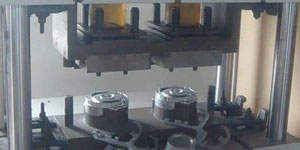
Industrias de fundición Estudios de casos de piezas para: automóviles, bicicletas, aeronaves, instrumentos musicales, embarcaciones, dispositivos ópticos, sensores, modelos, dispositivos electrónicos, carcasas, relojes, maquinaria, motores, muebles, joyas, plantillas, telecomunicaciones, iluminación, dispositivos médicos, dispositivos fotográficos, Robots, Esculturas, Equipos de sonido, Equipos deportivos, Herramientas, Juguetes y más.
¿Qué te podemos ayudar a hacer a continuación?
∇ Ir a la página de inicio para Fundición a presión China
→Piezas de fundición-Descubre lo que hemos hecho.
→ Consejos Ralated Acerca de Servicios de fundición a presión
By Fabricante de fundición a presión Minghe | Categorías: Artículos útiles |Material Tags: Fundición de aluminio, Fundición de zinc, Fundición de magnesio, Fundición de titanio, Fundición de acero inoxidable, Fundición de latón,Fundición de bronce,Casting de video,Historia de la empresa,Fundición a presión de aluminio | Comentarios desactivados