La historia y la tendencia del proceso de fundición de metales semisólidos
Desde 1971, DBSpencer y MCFlemings del Instituto de Tecnología de Massachusetts en los Estados Unidos inventaron un nuevo proceso de fundición con agitación (agitación), es decir, la preparación de una suspensión reológica de Srr15% pb mediante el método de agitación mecánica giratoria de doble barril, semisólido La tecnología de fundición de metales (SSM) ha experimentado más de 20 años de investigación y desarrollo.
Las aleaciones preparadas por fundición con agitación se denominan generalmente aleaciones no dendríticas o aleaciones de fundición parcialmente solidificadas (aleaciones de fundición parcialmente solidificadas). Debido a que los productos que utilizan esta tecnología tienen las características de alta calidad, alto rendimiento y alta aleación, tienen una gran vitalidad.
Además de la aplicación en equipos militares, comenzó a centrarse en los componentes clave de los vehículos automáticos, por ejemplo, las ruedas de los automóviles, que pueden mejorar el rendimiento, reducir el peso y reducir la tasa de desperdicio. Desde entonces, se ha aplicado gradualmente en otros campos, produciendo piezas de alto rendimiento y con forma casi neta. También se han introducido una tras otra las máquinas formadoras para la tecnología de fundición de metales semisólidos.
En la actualidad, se ha desarrollado y producido la máquina de fundición a presión semisólida de 600 toneladas a 2000 toneladas, y el peso de las piezas formadas puede alcanzar más de 7 kg. Actualmente, esta tecnología de proceso se usa ampliamente en los Estados Unidos y Europa. El proceso de fundición de metales semisólidos se considera una de las tecnologías de formación casi neta y de preparación de nuevos materiales más prometedoras del siglo XXI.
Principio de proceso
En el proceso de fundición ordinario, los cristales primarios crecen en forma de dendritas. Cuando la relación de fase sólida alcanza aproximadamente 0.2, las dendritas forman un esqueleto de red continuo y pierden su fluidez macroscópica. Si el metal líquido se agita vigorosamente durante el proceso de enfriamiento de la fase líquida a la fase sólida, el esqueleto de la red dendrítica que se forma fácilmente durante la colada ordinaria se romperá para retener la estructura granular dispersa y se suspenderá en la fase líquida restante. Esta microestructura granular no dendrítica todavía tiene cierta reología cuando la relación de fase sólida alcanza 0.5-0.6, de modo que se pueden utilizar procesos de conformado convencionales como fundición a presión, extrusión, forjado en matriz, etc. para lograr la conformación de metales.
Preparación de la aleación
Existen muchos métodos para preparar aleaciones semisólidas. Además de los métodos de agitación mecánica, en los últimos años se han desarrollado métodos de agitación electromagnética, métodos de carga de pulsos electromagnéticos, métodos de agitación por vibración ultrasónica, flujo forzado de líquido de aleación a lo largo de canales curvos bajo fuerza externa y activación de fusión inducida por tensión. Método (SIMA), método de deposición por pulverización (Ospray), método de control de la temperatura de vertido de la aleación, etc. Entre ellos, el método de agitación electromagnética, el método de control de la temperatura de vertido de la aleación y el método SIMA son los métodos más prometedores para aplicaciones industriales.
1. Método de agitación mecánica
La agitación mecánica es el método más antiguo utilizado para preparar aleaciones semisólidas. Flemings y col. preparó con éxito una suspensión semisólida de aleación de estaño-plomo utilizando un conjunto de dispositivos de agitación que constaba de un cilindro interno y externo dentado concéntrico (el cilindro externo giraba y el cilindro interno estaba estacionario); H. Lehuy y col. utilizó una paleta de agitación para preparar aluminio- Lechada semisólida de aleación de cobre, aleación de zinc-aluminio y aleación de aluminio-silicio. Las generaciones posteriores mejoraron el agitador y prepararon una suspensión semisólida de aleación ZA-22 mediante el uso de un agitador en espiral. A través de la mejora, se mejora el efecto de agitación de la lechada, se refuerza la resistencia general al flujo del metal fundido en el molde y el metal fundido genera presión hacia abajo, lo que promueve el vertido y mejora las propiedades mecánicas del lingote.
2. Método de agitación electromagnética
La agitación electromagnética es el uso de un campo electromagnético giratorio para generar una corriente inducida en el metal fundido. El metal fundido se mueve bajo la acción de la fuerza magnética de Loren para lograr el propósito de remover el metal fundido. En la actualidad, existen principalmente dos métodos para generar un campo magnético giratorio: uno es el método tradicional de pasar corriente alterna en la bobina de inducción; el otro es el método de imán permanente giratorio introducido por C. Vives de Francia en 1993, que tiene la ventaja de la inducción electromagnética. El dispositivo está compuesto de materiales de imán permanente de alto rendimiento con una alta intensidad de campo magnético. Al cambiar la disposición de los imanes permanentes, el metal fundido puede producir un flujo tridimensional obvio, lo que mejora el efecto de agitación y reduce el atrapamiento de gas durante la agitación.
3. Método de activación por fusión inducida por deformación (SIMA)
El método de activación por fusión inducida por deformación (SIMA) consiste en deformar previamente los lingotes convencionales, como extrusión, laminado y otros procesos térmicos en barras semiacabadas. En este momento, la microestructura tiene una estructura deformada fuertemente alargada, y luego se calienta a La zona de dos fases sólido-líquido es isotérmica durante un cierto período de tiempo, y los granos de cristal alargados se convierten en partículas finas, que luego se enfrían rápidamente para obtener un lingote de estructura no dendrítica.
El efecto del proceso SIMA depende principalmente de las dos etapas de trabajo en caliente y refundición a temperatura más baja, o si se agrega una etapa de trabajo en frío entre las dos, el proceso es más fácil de controlar. La tecnología SIMA es adecuada para una variedad de aleaciones con puntos de fusión altos y bajos, y tiene ventajas únicas en la preparación de aleaciones no dendríticas con puntos de fusión más altos. Se ha aplicado con éxito a series de acero inoxidable, acero para herramientas, aleación de cobre y aleación de aluminio, y ha obtenido una aleación de estructura no dendrítica con un tamaño de grano de aproximadamente 20um. Se está convirtiendo en un método competitivo para preparar materias primas de formación semisólidas. Sin embargo, su mayor desventaja es que el tamaño del blanco preparado es pequeño.
4. Nuevos métodos desarrollados en los últimos años
En los últimos años, la Universidad del Sureste y el Instituto de Investigación Arety en Japón han descubierto que al controlar la temperatura de fundición de la aleación, la estructura dendrítica primaria se puede transformar en una estructura esferulítica. La característica de este método es que no es necesario agregar elementos de aleación ni remover. V. Dobatkin y col. propuso un método para agregar un refinador al metal líquido y realizar un tratamiento ultrasónico para obtener un lingote semisólido, que se denomina tratamiento ultrasónico.
Método de moldeo
Existen muchos métodos de conformado para aleaciones semisólidas, principalmente:
1. El reoformado (Rheocast) agita fuertemente el metal fundido de líquido a sólido durante el proceso de enfriamiento, y directamente moldea o extruye hidráulicamente la suspensión de metal semisólida obtenida con una cierta fracción sólida.
Por ejemplo, R. Shibata et al. una vez enviada la suspensión de aleación semisólida preparada por el método de agitación electromagnética directamente a la cámara de inyección de la máquina de fundición a presión para su formación. Las propiedades mecánicas de las piezas de fundición de aleación de aluminio producidas por este método son superiores a las de las piezas de extrusión y equivalentes a las de las piezas de fundición tixotrópicas semisólidas. El problema es que el almacenamiento y transporte de lechada de metal semisólido es difícil, por lo que no hay muchas aplicaciones prácticas.
2. Tixocasting (Thixoforming, Thixocast)
El lingote de estructura no dendrítica preparado se recalienta a la zona de dos fases sólido-líquido para alcanzar una viscosidad adecuada, y luego se moldea a presión o se forma por extrusión.
EOPCO, HPM Corp., Prince Machine, THT Prensas en los Estados Unidos, Buhler en Suiza, IDRA USA, Italpresse of America en Italia, Producer USA en Canadá, Toshib a Machine Corp. Equipo especial para el tixoformado de aleaciones sólidas de aluminio. Este método permite automatizar fácilmente el calentamiento y transporte de la pieza en bruto, por lo que es el principal método de proceso de fundición semisólida en la actualidad.
3. Moldeo por inyección
El metal fundido se enfría directamente a una temperatura adecuada en lugar de la suspensión semisólida después del tratamiento, y se inyecta en la cavidad para formar con ciertas condiciones de proceso. Por ejemplo, el Thixoforming Development Center en Wisconsin, EE. UU., Utilizó este método para la fundición semisólida de aleaciones de magnesio. El profesor KK Wang de la Universidad de Cornell en los Estados Unidos y otros han desarrollado un dispositivo de moldeo por inyección de aleación de magnesio similar. La suspensión semisólida se agrega del tubo de material y se inyecta en la cavidad después de un enfriamiento adecuado.
4. Colada continua a baja temperatura
La llamada colada continua a baja temperatura es un método de colada en el que el sobrecalentamiento del metal fundido se controla a aproximadamente 0 ° C y el enfriamiento forzado se realiza debajo del molde, como se muestra en la Figura 4. La segregación central es un gran problema en colada continua, y pueden producirse roturas durante el laminado continuo del alambrón. Por tanto, el proceso es de gran importancia.
5. Pelar colada continua
Flemings utilizó Sn-15% pb de metal de bajo punto de fusión para llevar a cabo experimentos de colada continua de bandas y analizó la transferencia de calor, solidificación y deformación. Se cree que el espesor de la tira está relacionado con la presión del rodillo, la relación de fase sólida, la velocidad de cizallamiento reológico y la velocidad de colada continua. Cuando la presión específica bajo extrusión es grande, se promueve la microsegregación. Para garantizar la calidad de la superficie, la calidad interna y la precisión dimensional, es necesario controlar estrictamente los parámetros del proceso de fabricación de metales semisólidos, como la relación de fase sólida, el tamaño de la forma del cristal primario y la cantidad de metal descargado.
Para metales de alto punto de fusión, como la aleación de bronce fosforoso Cu-Sn-P (Cu-8% Sn-0.1% P), la temperatura del líquido es de 10300 ℃, que es difícil de procesar con calor. Tiene un efecto obvio en la placa delgada hecha de esta aleación semisólida. En la actualidad, es posible preparar lingotes de acero inoxidable semisólidos y lingotes de acero para herramientas de alta velocidad con una excelente organización.
Ventajas técnicas
Las ventajas del proceso de fundición a presión semisólida se pueden resumir en ventajas del proceso y ventajas del producto.
1. Ventaja del proceso
- 1) Se puede obtener una estructura de grano fino sin agregar ningún refinador de grano, eliminando cristales columnares y dendritas gruesas en la fundición tradicional.
- 2) Baja temperatura de formación (como la aleación de aluminio se puede reducir en más de 1200 ℃), lo que puede ahorrar energía.
- 3) Se alarga la vida del molde. El esfuerzo cortante de la lechada semisólida a una temperatura del sólido más baja es tres órdenes de magnitud menor que el de la lechada dendrítica tradicional, por lo que el relleno es estable, la carga térmica es pequeña y la resistencia a la fatiga térmica se reduce.
- 4) Reducir la contaminación y los factores inseguros. Elimine el ambiente de metal líquido de alta temperatura durante el funcionamiento.
- 5) La resistencia a la deformación es pequeña, y el procesamiento homogéneo se puede realizar con una pequeña fuerza, y la formación de materiales difíciles de procesar es fácil.
- 6) Se acelera la velocidad de solidificación, se mejora la productividad y se acorta el ciclo del proceso.
- 7) Es adecuado para el diseño y la fabricación asistidos por computadora, lo que mejora el grado de automatización de la producción.
2. Ventajas del producto
- 1) Las piezas son de alta calidad. Debido al refinamiento de los granos de cristal, la distribución uniforme de la estructura, la contracción del cuerpo reducida y la tendencia al agrietamiento térmico reducida, se elimina la tendencia a la contracción de la matriz y se mejoran en gran medida las propiedades mecánicas.
- 2) La contracción por solidificación es pequeña, por lo que el cuerpo moldeado tiene una alta precisión dimensional, un pequeño margen de mecanizado y una forma casi neta.
- 3) Amplia gama de aleaciones de formación. Las aleaciones no ferrosas incluyen aleaciones de aluminio, magnesio, zinc, estaño, cobre y níquel; Las aleaciones a base de hierro incluyen acero inoxidable y acero de baja aleación.
- 4) Fabricación de materiales compuestos de matriz metálica. Al utilizar la alta viscosidad del metal semisólido para hacer aleaciones con una gran diferencia de densidad y una pequeña solubilidad de sólidos, también puede mezclar eficazmente diferentes materiales para crear nuevos materiales compuestos.
Conserve la fuente y la dirección de este artículo para reimprimir: La historia y la tendencia del proceso de fundición de metales semisólidos
Minhe Empresa de fundición a presión se dedican a fabricar y proporcionar piezas de fundición de calidad y alto rendimiento (la gama de piezas de fundición a presión de metal incluye principalmente Fundición a presión de pared delgada,Fundición a presión en cámara caliente,Fundición a presión de cámara fría), Servicio redondo (servicio de fundición a presión,Mecanizado cnc,Fabricación de moldes, Tratamiento de superficie) .Cualquier fundición a presión de aluminio personalizada, fundición a presión de magnesio o Zamak / zinc y otros requisitos de fundición pueden contactarnos.
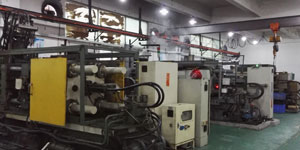
Bajo el control de ISO9001 y TS 16949, todos los procesos se llevan a cabo a través de cientos de máquinas de fundición a presión avanzadas, máquinas de 5 ejes y otras instalaciones, que van desde desintegradores hasta lavadoras Ultra Sonic.Minghe no solo cuenta con equipos avanzados, sino que también cuenta con profesionales equipo de ingenieros, operadores e inspectores experimentados para hacer realidad el diseño del cliente.
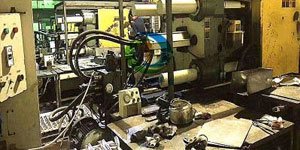
Fabricante por contrato de piezas de fundición a presión. Las capacidades incluyen piezas de fundición a presión de aluminio de cámara fría de 0.15 libras. a 6 libras, configuración de cambio rápido y mecanizado. Los servicios de valor agregado incluyen pulido, vibración, desbarbado, granallado, pintura, enchapado, revestimiento, ensamblaje y herramientas. Los materiales con los que se trabaja incluyen aleaciones como 360, 380, 383 y 413.
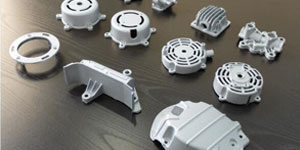
Asistencia en el diseño de fundición a presión de zinc / servicios de ingeniería simultáneos. Fabricante personalizado de piezas fundidas de zinc de precisión. Se pueden fabricar piezas de fundición en miniatura, piezas de fundición a presión de alta presión, piezas de fundición de moldes de deslizamiento múltiple, piezas de fundición de moldes convencionales, piezas de fundición unitaria e independiente y piezas de fundición selladas en cavidades. Las piezas fundidas se pueden fabricar en longitudes y anchos de hasta 24 pulgadas con una tolerancia de +/- 0.0005 pulgadas.
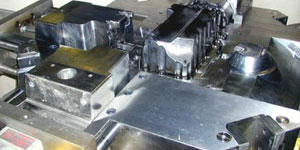
Fabricante certificado por ISO 9001: 2015 de magnesio fundido a presión, las capacidades incluyen fundición a presión de magnesio a alta presión de hasta 200 toneladas de cámara caliente y 3000 toneladas de cámara fría, diseño de herramientas, pulido, moldeado, mecanizado, pintura en polvo y líquida, control de calidad completo con capacidades de CMM , montaje, embalaje y entrega.
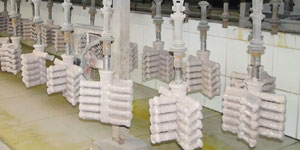
Certificado ITAF16949. El servicio de casting adicional incluye fundición de inversión,moldeo en arena,Fundición por gravedad, Fundición de espuma perdida,Fundición centrífuga,Fundición al vacío,Fundición de molde permanenteLas capacidades incluyen EDI, asistencia de ingeniería, modelado de sólidos y procesamiento secundario.
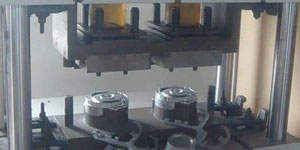
Industrias de fundición Estudios de casos de piezas para: automóviles, bicicletas, aeronaves, instrumentos musicales, embarcaciones, dispositivos ópticos, sensores, modelos, dispositivos electrónicos, carcasas, relojes, maquinaria, motores, muebles, joyas, plantillas, telecomunicaciones, iluminación, dispositivos médicos, dispositivos fotográficos, Robots, Esculturas, Equipos de sonido, Equipos deportivos, Herramientas, Juguetes y más.
¿Qué te podemos ayudar a hacer a continuación?
∇ Ir a la página de inicio para Fundición a presión China
→Piezas de fundición-Descubre lo que hemos hecho.
→ Consejos Ralated Acerca de Servicios de fundición a presión
By Fabricante de fundición a presión Minghe | Categorías: Artículos útiles |Material Tags: Fundición de aluminio, Fundición de zinc, Fundición de magnesio, Fundición de titanio, Fundición de acero inoxidable, Fundición de latón,Fundición de bronce,Casting de video,Historia de la empresa,Fundición a presión de aluminio | Comentarios desactivados