El control de la atmósfera durante el proceso de sinterización del acero sinterizado y su rendimiento
Atmósfera de sinterización y su selección.
Si solo se considera la sinterización de acero que contiene carbono, la atmósfera de sinterización utilizada en la industria de la pulvimetalurgia es hidrógeno, nitrógeno, nitrógeno + hidrógeno (potencial de carbono o sin potencial de carbono), descomposición de amoniaco, gas endotérmico, gas endotérmico + nitrógeno, síntesis Para gas y vacío, la selección correcta de la atmósfera de sinterización requiere la comprensión de las características y el rendimiento de varias atmósferas de sinterización, y la selección de acuerdo con los principios de garantizar la calidad y reducir los costos.
El hidrógeno es una atmósfera reductora fuerte. Mucha gente cree que el hidrógeno tiene un cierto efecto de descarburación, pero esto depende en gran medida de la pureza del hidrógeno utilizado en lugar del hidrógeno en sí. Generalmente, el hidrógeno después de la electrólisis o conversión catalítica contiene una cierta cantidad de gas de impureza, como H2O, O2, CO y CH4, etc., a veces la cantidad total puede alcanzar aproximadamente el 0.5%. Por lo tanto, es mejor secarlo y purificarlo antes de usarlo para reducir su contenido de oxígeno y su punto de rocío. Sin embargo, debido al alto precio del hidrógeno, el hidrógeno puro rara vez se usa como atmósfera de sinterización, a menos que existan razones especiales.
El nitrógeno es un gas inerte seguro y barato, pero debido a que el nitrógeno puro no tiene capacidad de reducción a la temperatura de sinterización, el nitrógeno puro rara vez se utiliza como atmósfera de sinterización en la producción de acero pulvimetalúrgico tradicional. En los últimos años, a medida que ha disminuido el coste de la purificación de nitrógeno y ha mejorado la estanqueidad al aire del horno de sinterización, también se ha comenzado a utilizar nitrógeno como atmósfera de sinterización para sinterizar acero que contiene carbono.
En los últimos años, la mezcla de nitrógeno e hidrógeno se ha utilizado cada vez más en la sinterización de acero al carbono. El nitrógeno / hidrógeno se usa generalmente entre 95 / 5-50 / 50. Esta mezcla tiene un cierto grado de reducibilidad y el punto de rocío puede llegar por debajo de -60 ℃, en general, se debe agregar una cierta cantidad de CH4 o C3H8 para mantener un cierto potencial de carbono cuando se usa este gas a 1050-1150 ℃, mientras se sinteriza. el acero al carbono por encima de 1250 ℃ no necesita controlar el potencial de carbono. Esta mezcla se puede utilizar para sinterizar aleaciones a base de hierro que contienen cromo por debajo de 1120 ° C sin oxidación.
El amoníaco descompuesto se produce al descomponer el gas amoníaco a través de un catalizador calentado, que incluye 75% de H2 y 25% de N2. Pero en términos generales, una pequeña cantidad de moléculas de amoníaco sin descomponer siempre permanece en el amoníaco descompuesto. Cuando están en contacto con metal caliente a altas temperaturas, se descomponen en átomos de hidrógeno y nitrógeno altamente activos, nitrurando así el metal. Estudios recientes han demostrado que si se controla adecuadamente, la sinterización de AstaloyCrM a 1120 ° C descompondrá y amoniará la mezcla 90N2 / 10H2 con una reducibilidad más fuerte. La razón principal es que estos átomos de hidrógeno activo que se acaban de descomponer durante el proceso de sinterización son más efectivos que el 90N2 / El hidrógeno en el gas mixto 10H2 tiene una capacidad de reducción más fuerte y puede reducir efectivamente la capa de óxido fuera de las partículas de AstaloyCrM. Para purificar y descomponer el amoníaco, puedes pasarlo por agua y secarlo, o usar alúmina activada o un tamiz molecular para eliminar el resto. Se elimina todo el amoníaco.
El gas endotérmico es un tipo de gas mixto que se obtiene mezclando gas hidrocarburo (CH4 o C3H8) con aire en cierta proporción, precalentando a 900-1000 ° C y convirtiéndolo catalíticamente con un catalizador de óxido de níquel. Dependiendo de la relación de aire a gas de carbón, el proceso de conversión se acompaña de reacciones endotérmicas o exotérmicas. El gas mixto resultante se llama gas endotérmico o gas exotérmico, y la reacción puede ser la siguiente:
CmHn+m(O2+3.774N2)—mCO+n/H2+1.887mN2
Si la reacción anterior se va a llevar a cabo completamente, es decir, todo el C en CmHm acaba de reaccionar con el O2 en el aire, el aire / gas requerido debe ser m / 2 (1 + 3.774), que es 2.387 m. Por ejemplo, si el gas de hidrocarburo usado es CH4, el aire / gas requerido debe ser 2.387, y el gas mezclado producido en este momento incluye 40.9% H2, 38.6% N2 y 20.5% CO. Después de la reacción, el gas mezclado contiene H2 El contenido de CO y CO disminuye con el aumento de aire / gas, pero aumenta el contenido de H2O y CO2. También muestra que el potencial de carbono en el gas mezclado después de la reacción disminuye con el aumento de aire / gas y aumenta el rendimiento de oxidación. Esta es también la razón principal por la que rara vez se usa gas exotérmico cuando se sinteriza acero que contiene carbono, y se usa la mayoría de los gases endotérmicos.
En términos generales, el gas mezclado producido por aire / gas entre 2.0-3.0 se llama gas caliente de absorción, y el gas mezclado producido cuando la relación es mayor que 5.0 se llama gas exotérmico. La relación entre el punto de rocío del gas endotérmico producido con CH4 como materia prima y el aire / gas muestra que el aire / gas solo aumenta de 2.4 a 2.5, y el punto de rocío del gas mezclado producido aumenta de -25 ° C a por encima de 0 ° C. Por lo tanto, si los usuarios producen gas endotérmico por sí mismos, deben prestar especial atención a controlar la relación de aire a gas en las materias primas (preferiblemente no más de 2.4) para obtener gas endotérmico con un punto de rocío suficientemente bajo. En el gas mezclado después de la reacción, la proporción de los diferentes gases corresponde a la proporción al final de la reacción, que generalmente es (1000-1100 ° C).
Después de la reacción, si la temperatura del gas cambia, el potencial de carbono del gas mezclado, el punto de rocío y la proporción de diferentes gases cambiarán. Muchos fabricantes de pulvimetalurgia utilizan un generador de gas exotérmico para suministrar la atmósfera de sinterización necesaria para varios hornos de sinterización al mismo tiempo a través de la tubería. La temperatura de la atmósfera se ha reducido antes de llegar al horno de sinterización. . Si el aislamiento de la tubería no es bueno y la temperatura de la pared de la tubería es inferior a 800 ° C, una parte del carbono del gas mezclado se depositará en la pared de la tubería en forma de negro de humo. En otras palabras, cuando el gas mezclado se recalienta a la temperatura de sinterización en el horno de sinterización, su calor de carbono es mucho más bajo que el potencial de carbono que puede proporcionar el generador de gas endotérmico.
En este caso, se debe agregar una cantidad adecuada de metano o propano al horno de sinterización para asegurar el potencial de carbono en el horno. Ahora, algunos fabricantes extranjeros de pulvimetalurgia han comenzado a instalar un pequeño generador de gas endotérmico al lado de cada horno de sinterización, y utilizan el gas endotérmico que se acaba de producir directamente en el horno de sinterización sin enfriar, para evitar afectar la atmósfera de sinterización debido a los cambios de temperatura. . . Otro punto a recordar es que incluso con el efecto catalítico del catalizador de óxido de níquel, una pequeña cantidad de gas hidrocarburo (CH4 o C3H8, etc.) permanece en la mezcla de gas obtenida después del transporte. Además, entre los gases a 900-1100 ℃ Después de que la reacción alcance el equilibrio, se producirá una pequeña cantidad de CO2 y H2O (gaseoso), que deben secarse antes de su uso.
La adición de nitrógeno al gas endotérmico puede reducir el contenido relativo de CO, CO2 y H2O en el gas endotérmico, a fin de amortiguar la sensibilidad de la atmósfera al potencial de carbono y al punto de rocío, y facilitar algunos coeficientes de correlación en la atmósfera de sinterización. al control.
El gas sintético es un método propuesto por fabricantes extranjeros de hornos de sinterización en los últimos años para generar directamente (diluir) gas endotérmico en el horno de sinterización (sin la necesidad de un generador de gas endotérmico fuera del horno). Mezcla alcohol metílico gaseoso y nitrógeno en cierta proporción y luego lo pasa directamente al horno de sinterización. Las siguientes reacciones ocurrirán en la zona de sinterización a alta temperatura:
CH3OH — CO + 2H2
Debido a que la proporción de CO y H2 en el gas descompuesto es igual a la proporción del gas endotérmico producido por el método habitual con CH4, y el nitrógeno mezclado se puede combinar para sintetizar una atmósfera mixta con la misma composición que el gas endotérmico (1L El metano corresponde a 1.05nm3 de nitrógeno). Su mayor ventaja es que no requiere un generador de gas endotérmico fuera del horno. Además, los usuarios pueden mezclar diferentes cantidades de gas nitrógeno para producir gas endotérmico diluido de acuerdo con sus propios requisitos.
El vacío también es un tipo de atmósfera de sinterización, que se utiliza principalmente para sinterizar acero inoxidable y otros materiales, pero no se utiliza habitualmente para sinterizar acero al carbono.
Propiedades físicas de la atmósfera de sinterización
La mayoría de los artículos e informes sobre atmósferas de sinterización discuten principalmente el comportamiento químico entre diferentes atmósferas de sinterización y el cuerpo sinterizado durante el proceso de sinterización, pero rara vez discuten la influencia de las propiedades físicas de diferentes atmósferas en la sinterización, aunque este efecto en muchos casos no es posible. ser ignorado. Por ejemplo, la diferencia en la viscosidad del gas provocará el gradiente de concentración química del cuerpo sinterizado desde la superficie hacia el interior a lo largo de la abertura, lo que afectará a las propiedades superficiales del cuerpo sinterizado. Por otro ejemplo, la capacidad calorífica y la conductividad térmica de diferentes gases tienen una gran influencia en el tiempo de sinterización y la velocidad de enfriamiento. Esta sección enumera las principales propiedades físicas de algunas atmósferas de sinterización a diferentes temperaturas (alrededor de la temperatura de sinterización) para referencia de los lectores.
Ejemplos de problemas relacionados con la atmósfera durante la sinterización.
1 Ejemplos de grietas en la superficie de las piezas durante el desparafinado
Cuando se usa un horno de sinterización de cinta de malla y se usa gas endotérmico como atmósfera de sinterización, si la tasa de aumento de temperatura y la atmósfera en la zona de desparafinado no están bien controladas, se producirá el agrietamiento de la superficie. Mucha gente piensa que este fenómeno se debe a la rápida descomposición del lubricante que se provoca, pero no es así. La verdadera razón es que el monóxido de carbono en el gas endotérmico se descompone en carbono sólido y dióxido de carbono en el rango de temperatura de 450-700 ℃ bajo la catálisis de hierro, níquel y otros metales. Es el carbono sólido recién depositado en los poros del cuerpo sinterizado el que expande su volumen y provoca el fenómeno de agrietamiento superficial mencionado anteriormente.
La calidad de las piezas varía con la temperatura durante el proceso de sinterización en diferentes atmósferas. Entre ellos, la atmósfera 3 es gas de carbón endotérmico seco, y las atmósferas 4 y 5 son gas de carbón endotérmico agregado con diferentes cantidades de vapor de agua. Se puede observar que durante el proceso de sinterización, la calidad de las piezas comienza a declinar a unos 200 ° C, lo que significa que el lubricante sólido en su interior se descompone continuamente y desborda el cuerpo de sinterización, reduciendo su calidad. Por supuesto, si no hay lubricante sólido en el polvo mezclado, el fenómeno anterior no existe. Si se utilizan las tres atmósferas anteriores, cuanto más seca sea la atmósfera de la calidad del cuerpo sinterizado a aproximadamente 450 ° C, más grave será este fenómeno.
Pero lo interesante es que cuando se usa gas 3 (gas endotérmico seco), el agrietamiento superficial ocurre independientemente de la presencia de lubricantes sólidos, lo que indica que no está directamente relacionado con el desparafinado, y se encuentra gas rico en carbono en las grietas. Fenómeno, podemos afirmar la veracidad de la explicación anterior.
Hay varias formas de evitar la aparición del fenómeno de agrietamiento mencionado anteriormente. Lo más directo es cambiar la atmósfera de sinterización de gas endotérmico a una mezcla de hidrógeno-nitrógeno sin romper las líneas discontinuas. Si no se puede cambiar la atmósfera de sinterización, existen dos métodos. Una consiste en soplar parte del gas endotérmico que contiene vapor de agua en la zona de desparafinado del horno de sinterización. Sin embargo, este método es difícil de obtener un control estable en la operación real.
El control del flujo de aire del horno de sinterización no es bueno y el fenómeno de una atmósfera de alto punto de rocío que ingresa a la zona de sinterización puede afectar la calidad de la sinterización. El segundo y mejor método es aumentar la velocidad de calentamiento de las piezas en la zona de desparafinado del horno de sinterización para que pase a 450 lo antes posible. En la zona donde se produce el agrietamiento a -600 ° C, el llamado desparafinado rápido suele estar diseñado para este fenómeno.
2 Ejemplo de sinterización de AstaloyCrM
El cromo metálico se usa ampliamente en acero aleado debido a su bajo precio y buen efecto de refuerzo. Sin embargo, el acero sinterizado que contiene cromo encontrará muchos problemas en su proceso de producción. Uno es la producción de polvo de hierro que contiene cromo, que debe someterse a un estricto proceso de atomización y reducción de recocido para obtener polvo de materia prima con menor contenido de oxígeno y carbono. .
Honganas AB de Suecia es actualmente el único fabricante en el mundo que puede producir esta materia prima en polvo a bajo costo. La segunda es que incluso si se puede obtener polvo de hierro que contiene cromo de alta calidad, si la sinterización y la temperatura media, especialmente la atmósfera de sinterización, no se pueden controlar bien, será más probable que se oxide durante la sinterización y oxidación, y la se reducirá el rendimiento de sinterización.
Los cálculos termodinámicos y una gran cantidad de experimentos han demostrado que si el gas endotérmico se utiliza como atmósfera de sinterización de AsaloyCrM, los requisitos de sinterización no se pueden cumplir incluso si el punto de rocío es muy bajo.
En otras palabras, solo se puede usar hidrógeno puro o una mezcla de hidrógeno-nitrógeno para sinterizar AsaloyCrM. En la actualidad, se utilizan la mayoría de estos últimos. , La proporción de hidrógeno representa el 5% -20%. Se debe recordar al lector que no solo debe garantizar la composición de la atmósfera de sinterización, sino también la calidad de la atmósfera de sinterización.
La denominada calidad aquí se refiere al grado de oxidación en la atmósfera de sinterización, que generalmente se calibra por la presión parcial de oxígeno en la atmósfera. Al sinterizar a 1120 ℃, si la presión parcial de oxígeno en la atmósfera es inferior a 1 × 10-14Pa, no se producirá oxidación durante el proceso de sinterización.
Cuando se baja la temperatura, para evitar la oxidación, se requiere que la presión parcial de oxígeno en la atmósfera sea incluso baja. También puede garantizar que AsaloyCrM sinterizado a 1125 ℃ no se oxide a 1 × 10-14Pa. El cálculo anterior ha sido confirmado por datos experimentales.
Conserve la fuente y la dirección de este artículo para reimprimir: El control de la atmósfera durante el proceso de sinterización del acero sinterizado y su rendimiento
Minhe Empresa de fundición a presión se dedican a fabricar y proporcionar piezas de fundición de calidad y alto rendimiento (la gama de piezas de fundición a presión de metal incluye principalmente Fundición a presión de pared delgada,Fundición a presión en cámara caliente,Fundición a presión de cámara fría), Servicio redondo (servicio de fundición a presión,Mecanizado cnc,Fabricación de moldes, Tratamiento de superficie) .Cualquier fundición a presión de aluminio personalizada, fundición a presión de magnesio o Zamak / zinc y otros requisitos de fundición pueden contactarnos.
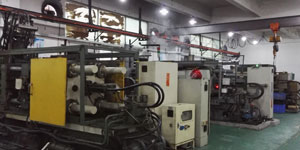
Bajo el control de ISO9001 y TS 16949, todos los procesos se llevan a cabo a través de cientos de máquinas de fundición a presión avanzadas, máquinas de 5 ejes y otras instalaciones, que van desde desintegradores hasta lavadoras Ultra Sonic.Minghe no solo cuenta con equipos avanzados, sino que también cuenta con profesionales equipo de ingenieros, operadores e inspectores experimentados para hacer realidad el diseño del cliente.
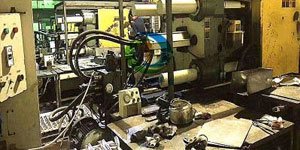
Fabricante por contrato de piezas de fundición a presión. Las capacidades incluyen piezas de fundición a presión de aluminio de cámara fría de 0.15 libras. a 6 libras, configuración de cambio rápido y mecanizado. Los servicios de valor agregado incluyen pulido, vibración, desbarbado, granallado, pintura, enchapado, revestimiento, ensamblaje y herramientas. Los materiales con los que se trabaja incluyen aleaciones como 360, 380, 383 y 413.
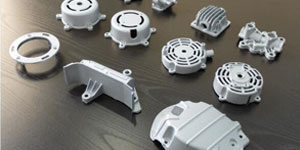
Asistencia en el diseño de fundición a presión de zinc / servicios de ingeniería simultáneos. Fabricante personalizado de piezas fundidas de zinc de precisión. Se pueden fabricar piezas de fundición en miniatura, piezas de fundición a presión de alta presión, piezas de fundición de moldes de deslizamiento múltiple, piezas de fundición de moldes convencionales, piezas de fundición unitaria e independiente y piezas de fundición selladas en cavidades. Las piezas fundidas se pueden fabricar en longitudes y anchos de hasta 24 pulgadas con una tolerancia de +/- 0.0005 pulgadas.
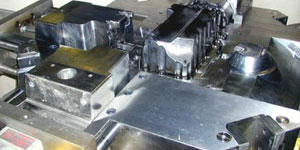
Fabricante certificado por ISO 9001: 2015 de magnesio fundido a presión, las capacidades incluyen fundición a presión de magnesio a alta presión de hasta 200 toneladas de cámara caliente y 3000 toneladas de cámara fría, diseño de herramientas, pulido, moldeado, mecanizado, pintura en polvo y líquida, control de calidad completo con capacidades de CMM , montaje, embalaje y entrega.
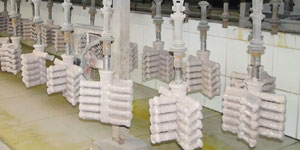
Certificado ITAF16949. El servicio de casting adicional incluye fundición de inversión,moldeo en arena,Fundición por gravedad, Fundición de espuma perdida,Fundición centrífuga,Fundición al vacío,Fundición de molde permanenteLas capacidades incluyen EDI, asistencia de ingeniería, modelado de sólidos y procesamiento secundario.
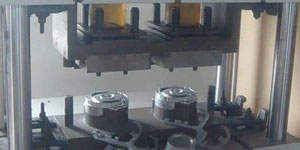
Industrias de fundición Estudios de casos de piezas para: automóviles, bicicletas, aeronaves, instrumentos musicales, embarcaciones, dispositivos ópticos, sensores, modelos, dispositivos electrónicos, carcasas, relojes, maquinaria, motores, muebles, joyas, plantillas, telecomunicaciones, iluminación, dispositivos médicos, dispositivos fotográficos, Robots, Esculturas, Equipos de sonido, Equipos deportivos, Herramientas, Juguetes y más.
¿Qué te podemos ayudar a hacer a continuación?
∇ Ir a la página de inicio para Fundición a presión China
→Piezas de fundición-Descubre lo que hemos hecho.
→ Consejos Ralated Acerca de Servicios de fundición a presión
By Fabricante de fundición a presión Minghe | Categorías: Artículos útiles |Material Tags: Fundición de aluminio, Fundición de zinc, Fundición de magnesio, Fundición de titanio, Fundición de acero inoxidable, Fundición de latón,Fundición de bronce,Casting de video,Historia de la empresa,Fundición a presión de aluminio | Comentarios desactivados