Tres razones para las fugas de material fundido durante la producción de moldes
En comparación con los moldes de canal caliente, el sistema de compuerta en el molde de canal caliente siempre está a una temperatura alta durante el uso, y el plástico fundido es propenso a tener fugas en las juntas de las partes del sistema de canal caliente bajo la acción de altas temperaturas y altas temperaturas. presión. Las fugas de material fundido no solo afectarán la calidad de las piezas de plástico, sino que también dañarán gravemente el molde, lo que provocará una falla en la producción. Hay dos partes principales con fugas del molde del canal caliente, una es la cara final del canal en la placa del canal y la otra es la superficie de unión de la placa del canal y la boquilla (incluida la boquilla de la compuerta y la boquilla del canal principal) . Hay muchas razones para las fugas de masa fundida, que se pueden resumir en tres aspectos: operación incorrecta, proceso de ensamblaje y diseño de sellado irrazonable. Este artículo presenta las causas de las fugas de masa fundida y las medidas de precaución.
Derretir fugas causadas por factores del proceso.
La tecnología de operación incorrecta es una de las principales razones de las fugas de masa fundida durante la producción de moldes. Para compensar la expansión térmica de las partes del sistema de canal caliente, a menudo existe un cierto espacio frío entre las partes al diseñar y ensamblar el molde. Solo bajo la temperatura de funcionamiento especificada, la expansión térmica de las piezas puede eliminar completamente el espacio frío y lograr el sellado y la prevención de fugas. Las fugas de masa fundida causadas por un funcionamiento incorrecto se producen principalmente en las siguientes situaciones:
- Derretir fugas causadas por un proceso de calentamiento del sistema incorrecto o un control de temperatura desigual. Durante el proceso de calentamiento, si la tasa de calentamiento de la boquilla es mayor que la tasa de calentamiento de la placa del canal caliente, la expansión térmica axial de las partes del sistema limitará la expansión térmica transversal de la placa del canal caliente, haciendo que la placa del canal caliente se deforme y causar fugas de masa fundida. La temperatura desigual de las partes del sistema de compuerta causará una expansión desigual de las partes y también hará que las partes se deformen y causen fugas de masa fundida.
- Inyecte por adelantado cuando el sistema no alcance la temperatura de funcionamiento especificada. Como se muestra, después de calentar el sistema, el anillo de soporte 6, la placa de canal caliente 5 y la boquilla de compuerta 4 experimentan expansión térmica en la dirección axial, y el anillo de soporte se comprime en la placa de montaje del molde fijo 3, y una cierta Se genera una cantidad de calor entre la placa del canal caliente y la boquilla. presión. Si la inyección se realiza cuando no se alcanza la temperatura especificada, la presión térmica generada por la expansión térmica no es suficiente para compensar la presión de la masa fundida, lo que hará que la boquilla 4 y la placa del canal caliente 5 se separen y provoquen fugas de masa fundida.
- Derretir la fuga causada por la temperatura de calentamiento del sistema superior a la temperatura de funcionamiento. En este caso, debido a la expansión térmica excesiva, se generará una gran presión térmica, lo que hará que las partes del sistema se deformen y derritan fugas.
Por otro lado, cuando la temperatura del sistema de compuerta se reduce a la temperatura de funcionamiento, también se producirán fugas de masa fundida debido a la mala adaptabilidad de la boquilla térmica con bordes rígidos a la expansión térmica.
En resumen, operar de acuerdo con los pasos correctos y las condiciones del proceso es un requisito previo para evitar fugas de masa fundida. El molde de canal caliente general se puede operar de acuerdo con los siguientes pasos:
- Caliente el sistema de canal caliente a la temperatura establecida. Generalmente se divide en dos pasos: el primero es un arranque suave para eliminar la humedad en el calentador.
- Calentar el molde a la temperatura establecida. Especialmente para moldes grandes, se calienta antes de la inyección y luego se enfría durante la inyección.
- Caliente el barril de la máquina de inyección a la temperatura establecida. El segundo paso es calentar el sistema a la temperatura establecida a plena carga. La temperatura de la boquilla se puede calentar a 2/3 de la temperatura de la placa del canal caliente. Una vez que la temperatura de la placa del canal caliente alcanza la temperatura de diseño, la temperatura de la boquilla se calienta a la temperatura establecida.
- Para el sistema de canal caliente nuevo o limpio, se debe utilizar primero una inyección lenta a baja presión.
- Si no hay fugas de masa fundida después de varios ciclos de inyección, los parámetros del proceso de inyección establecidos se utilizan para la producción.
Diseño de sellado del sistema de canal caliente
Compensación de expansión térmica del sistema de canal caliente
El molde ensamblado a temperatura ambiente hará que la posición relativa de las partes cambie durante la expansión térmica de las partes del sistema de canal caliente. Para compensar la expansión térmica de las piezas, es necesario dejar un espacio de expansión adecuado, como el espacio frío A y C que se muestran. Se fija en la plantilla fija 1 mediante el pasador de posicionamiento central 7 y se estira después de calentarse. La expansión térmica transversal de la placa del canal caliente reducirá el espacio A entre la placa del canal caliente y el perno antirrotación 2. Si el valor A es menor que la expansión térmica transversal de la placa del canal caliente en el diseño, el El pasador de rotación evitará la extensión transversal de la placa del canal caliente después del calentamiento.
Provoca el alabeo y la deformación de la placa del canal caliente, lo que hace que el sello entre la placa del canal caliente y la boquilla sea ineficaz y provoque fugas de masa fundida. La expansión térmica axial del anillo de soporte 6, la placa del canal caliente 5 y la boquilla de la compuerta 4 eliminarán el espacio frío C. Si el espacio frío es demasiado grande y la expansión térmica axial es insuficiente, la presión de la masa fundida durante la inyección provocará la boquilla de compuerta 4 y el canal caliente La placa 5 se separa y la masa fundida tiene fugas. Si el espacio frío es demasiado pequeño y la presión de expansión térmica del sistema es demasiado grande, las piezas del sistema se doblarán o la tensión de compresión excederá la tensión de fluencia de la plantilla fija, lo que hará que el anillo de soporte aplaste la pieza fija. plantilla, limitando así la expansión térmica lateral de la placa del canal caliente y provocando la puerta Se produjo una fuga de masa fundida entre la boquilla y la placa del canal caliente.
Por lo tanto, al diseñar el molde, calcular correctamente la expansión térmica del sistema y dejar un espacio de expansión térmica razonable son los requisitos previos para evitar fugas de masa fundida. La expansión térmica lineal del sistema se puede calcular mediante la siguiente fórmula: L = TL (1) El estrés térmico causado por la resistencia de la expansión térmica del sistema es: = EL-CL (2) La presión del molde fijo La placa fija se verifica mediante la siguiente fórmula p (3) donde: L es la expansión térmica lineal del sistema de canal caliente, mm; es el coeficiente de expansión térmica lineal del material de las piezas del sistema; T es la diferencia de temperatura entre las piezas del sistema de canal caliente y el molde; L es la longitud de las partes del sistema de corredera en la dirección de expansión a temperatura ambiente, mm; es la expansión térmica del sistema El estrés térmico causado por la resistencia, MPa; C es la cantidad de espacio reservado, mm; E es el módulo de elasticidad de las partes del sistema, MPa; p es la tensión de compresión admisible del material de la placa de molde fijo.
La forma de sellado del sistema de canal caliente
El sello plano entre la placa del canal caliente y la boquilla es una forma de sellado común en los sistemas de canal caliente extranjeros. Después de que el sistema se expande térmicamente en la dirección axial, el anillo de soporte se presiona sobre la placa del molde fijo y se genera una cierta presión térmica en el plano de unión de la placa del canal caliente y la boquilla para compensar la presión de fusión para sellar y evitar fuga. Este tipo de estructura no puede garantizar el sellado en frío y no existe una medida de protección contra el sobrecalentamiento. Solo bajo las condiciones de temperatura configuradas se pueden sellar la placa del canal caliente y la boquilla. Al diseñar, es necesario calcular con precisión la expansión térmica y dejar un espacio frío adecuado C.
B. El anillo de sellado en forma de O se utiliza en el plano de unión de la boquilla y la placa del canal caliente. El anillo de sellado en forma de O está hecho de tubería de acero inoxidable. Al ensamblar, hay una precarga de tubo de acero de 2030 de diámetro para evitar fugas de material fundido. Esta estructura es muy adecuada para placas y moldes de canal caliente de baja rigidez.
Se adopta la conexión elástica y el resorte proporciona tensión previa para realizar el sellado en el estado de enfriamiento. Cuando se sobrecalienta, el resorte absorbe la expansión térmica para evitar daños y fugas en el sistema. Es una forma de sellado ideal.
La boquilla de la compuerta se fija en la placa del canal caliente mediante roscas, y la boquilla y el anillo de presión deslizante se mueven con la placa del canal caliente cuando el sistema se expande térmicamente. Dado que el movimiento de la boquilla provocará la desalineación del eje de la guía de la boquilla y el eje de la compuerta en la plantilla fija, se debe considerar la expansión térmica lateral al diseñar la posición de la boquilla. Este tipo de sellado es adecuado para ocasiones con pocos puntos de inyección y una pequeña distancia entre boquillas.
Proceso de ensamblaje de la placa del canal caliente
La precisión de montaje y la secuencia de instalación del sistema de canal caliente están directamente relacionadas con si la masa fundida tiene fugas. Si la altura de la boquilla es inconsistente, el espacio entre la boquilla más corta y la placa del canal caliente causará fugas de masa fundida, y la deformación de la placa de la pista caliente causada por la altura inconsistente de la almohadilla de soporte y la altura de la boquilla también causará fugas de masa fundida.
Lo siguiente toma un molde de canal caliente de caja de plástico de 1 molde y 4 cavidades como ejemplo para ilustrar el proceso de ensamblaje de la placa del canal caliente:
- Fije firmemente la placa de fijación del molde.
- Presione el bloque del canal 7 en la placa del canal caliente 10, instale el pasador antirrotación 2 después de corregir la dirección, y luego presione el bloque con el tornillo de compresión 3, y use el anillo de sellado de metal en forma de O para evitar que la masa fundida se filtre .
- Instale la boquilla de compuerta 1 y la almohadilla de soporte 15 en la plantilla fija 14, y verifique si la altura de todos los planos del conjunto de boquillas es la misma en base al plano de la plantilla fija. Si son inconsistentes, realice el rectificado al valor mínimo, con una tolerancia de 0.01 mm.
- Intente instalar la placa del canal caliente y compruebe si la placa del canal caliente y el perno antirrotación 2 tienen las holguras A y B necesarias en las direcciones radial y axial.
- Fije el marco de la placa trasera 12 en la plantilla fija 14 con pernos.
- Basándose en el plano superior del marco de respaldo 12, repare todos los anillos de presión 6 para hacerlos consistentes en altura y tener un espacio con el plano superior del marco de respaldo. C.
- Enrosque la boquilla del canal principal 9 en la placa del canal caliente 10.
Conserve la fuente y la dirección de este artículo para reimprimir:Tres razones para las fugas de material fundido durante la producción de moldes
Minhe Empresa de fundición a presión se dedican a fabricar y proporcionar piezas de fundición de calidad y alto rendimiento (la gama de piezas de fundición a presión de metal incluye principalmente Fundición a presión de pared delgada,Fundición a presión en cámara caliente,Fundición a presión de cámara fría), Servicio redondo (servicio de fundición a presión,Mecanizado cnc,Fabricación de moldes, Tratamiento de superficie) .Cualquier fundición a presión de aluminio personalizada, fundición a presión de magnesio o Zamak / zinc y otros requisitos de fundición pueden contactarnos.
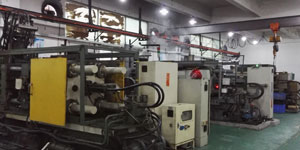
Bajo el control de ISO9001 y TS 16949, todos los procesos se llevan a cabo a través de cientos de máquinas de fundición a presión avanzadas, máquinas de 5 ejes y otras instalaciones, que van desde desintegradores hasta lavadoras Ultra Sonic.Minghe no solo cuenta con equipos avanzados, sino que también cuenta con profesionales equipo de ingenieros, operadores e inspectores experimentados para hacer realidad el diseño del cliente.
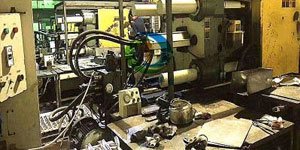
Fabricante por contrato de piezas de fundición a presión. Las capacidades incluyen piezas de fundición a presión de aluminio de cámara fría de 0.15 libras. a 6 libras, configuración de cambio rápido y mecanizado. Los servicios de valor agregado incluyen pulido, vibración, desbarbado, granallado, pintura, enchapado, revestimiento, ensamblaje y herramientas. Los materiales con los que se trabaja incluyen aleaciones como 360, 380, 383 y 413.
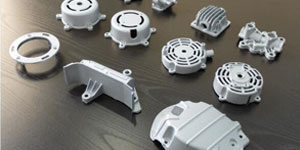
Asistencia en el diseño de fundición a presión de zinc / servicios de ingeniería simultáneos. Fabricante personalizado de piezas fundidas de zinc de precisión. Se pueden fabricar piezas de fundición en miniatura, piezas de fundición a presión de alta presión, piezas de fundición de moldes de deslizamiento múltiple, piezas de fundición de moldes convencionales, piezas de fundición unitaria e independiente y piezas de fundición selladas en cavidades. Las piezas fundidas se pueden fabricar en longitudes y anchos de hasta 24 pulgadas con una tolerancia de +/- 0.0005 pulgadas.
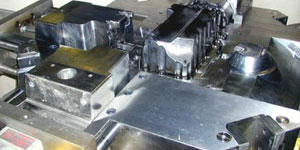
Fabricante certificado por ISO 9001: 2015 de magnesio fundido a presión, las capacidades incluyen fundición a presión de magnesio a alta presión de hasta 200 toneladas de cámara caliente y 3000 toneladas de cámara fría, diseño de herramientas, pulido, moldeado, mecanizado, pintura en polvo y líquida, control de calidad completo con capacidades de CMM , montaje, embalaje y entrega.
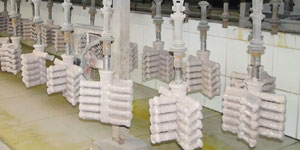
Certificado ITAF16949. El servicio de casting adicional incluye fundición de inversión,moldeo en arena,Fundición por gravedad, Fundición de espuma perdida,Fundición centrífuga,Fundición al vacío,Fundición de molde permanenteLas capacidades incluyen EDI, asistencia de ingeniería, modelado de sólidos y procesamiento secundario.
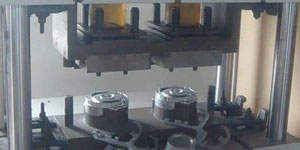
Industrias de fundición Estudios de casos de piezas para: automóviles, bicicletas, aeronaves, instrumentos musicales, embarcaciones, dispositivos ópticos, sensores, modelos, dispositivos electrónicos, carcasas, relojes, maquinaria, motores, muebles, joyas, plantillas, telecomunicaciones, iluminación, dispositivos médicos, dispositivos fotográficos, Robots, Esculturas, Equipos de sonido, Equipos deportivos, Herramientas, Juguetes y más.
¿Qué te podemos ayudar a hacer a continuación?
∇ Ir a la página de inicio para Fundición a presión China
→Piezas de fundición-Descubre lo que hemos hecho.
→ Consejos Ralated Acerca de Servicios de fundición a presión
By Fabricante de fundición a presión Minghe | Categorías: Artículos útiles |Material Tags: Fundición de aluminio, Fundición de zinc, Fundición de magnesio, Fundición de titanio, Fundición de acero inoxidable, Fundición de latón,Fundición de bronce,Casting de video,Historia de la empresa,Fundición a presión de aluminio | Comentarios desactivados