"Álcali" y "Magnesio" para mejorar el rendimiento de los pellets
Los pellets oxidados tienen buena resistencia mecánica y propiedades metalúrgicas, y se han convertido en una carga indispensable de alta calidad para la fabricación de hierro en altos hornos. Sin embargo, la falta de suministro nacional de concentrado de magnetita ha provocado que muchas plantas de acero nacionales utilicen hematita importada para producir pastillas de óxido. En comparación con los gránulos de magnetita, los gránulos de hematita tienen una temperatura de tostado alta y un rango estrecho (1300 ℃ ~ 1350 ℃), y los gránulos tienen baja resistencia a la compresión. Además, los gránulos de hematita ácida tienen malas propiedades metalúrgicas. Entre ellos, la specularita pertenece a un tipo importante de hematita, y el rendimiento de tostado y las propiedades metalúrgicas de los gránulos son peores que los gránulos de hematites ordinarios.
Los investigadores han realizado muchas investigaciones sobre cómo utilizar la hematita para producir gránulos oxidados de alta resistencia. Los estudios han demostrado que agregar magnetita a la hematita para preparar gránulos oxidados puede reducir eficazmente la temperatura de precalentamiento de tostado y aumentar la resistencia a la compresión de los gránulos de tostado precalentados; agregar fundente para producir gránulos de hematita fundente también es una solución.
Las plantas de pellets domésticos generalmente usan hematita y magnetita para producir pellets de alta resistencia, pero a medida que aumenta la proporción de hematita, el efecto de agregar magnetita se debilita en gran medida. La adición de fundente de CaO para producir bolitas de fundente puede obtener una mayor resistencia mecánica y una mejor reducibilidad a una temperatura más baja, pero el rendimiento del reflujo a alta temperatura es deficiente y la expansión de la reducción es grave. Los primeros estudios han demostrado que agregar MgO a los gránulos puede reducir la tasa de expansión de reducción y mejorar el rendimiento del reflujo a alta temperatura.
En la actualidad, hay relativamente pocos informes sobre el efecto de la alcalinidad y el contenido de MgO sobre la resistencia y las propiedades metalúrgicas de los gránulos de specularita, especialmente el efecto de la alcalinidad y el MgO sobre las propiedades metalúrgicas de los gránulos. Por lo tanto, este artículo, que estudia los efectos de la alcalinidad y el contenido de MgO sobre la resistencia y las propiedades metalúrgicas de los gránulos de specularita, tiene un valor teórico importante para mejorar el tostado de los gránulos y fortalecer la fabricación de hierro en altos hornos.
Propiedades de las materias primas y métodos de investigación.
Las materias primas utilizadas en este experimento son specularita brasileña, bentonita, piedra caliza y magnesita. Debido a que la especularita, la piedra caliza y la magnesita brasileñas son relativamente gruesas en tamaño de partícula, se muelen al tamaño de partícula y al área de superficie específica requerida para la producción de pellets con un molino de bolas en el laboratorio. La espiegelita tiene un alto grado de hierro, menos minerales de ganga y otras impurezas dañinas, y es una materia prima de pellets de alta calidad. La piedra caliza y la magnesita tienen un bajo contenido de SiO2 y pocas otras impurezas dañinas. Son fundentes de calcio y magnesio de alta calidad.
El aglutinante utilizado en la prueba es bentonita a base de sodio de alta calidad, y los indicadores son los siguientes: el contenido de montmorillonita es del 92.76%, el volumen de hinchamiento es de 20 ml / g, la tasa de absorción de agua en 2 horas es del 342% y el contenido de -0.074 mm alcanza el 100%.
La investigación experimental incluye el proceso de dosificación, mezcla, preparación de bolas verdes, secado de bolas verdes, precalentamiento de bolas secas, tostado y pruebas de rendimiento de pellets de tueste. El contenido de SiO2 de los gránulos terminados se controla al 3.0% ± 3.1% añadiendo arena de cuarzo finamente molida. La alcalinidad y el contenido de MgO de los gránulos terminados se ajustan agregando piedra caliza y magnesita, y los efectos de los cambios en la alcalinidad y el contenido de MgO en la resistencia a la compresión, el grado de reducción, la expansión por reducción, la pulverización por reducción a baja temperatura y la fusión suave a alta temperatura. Se investigan las características de los gránulos tostados. Influencia.
Resultados de pruebas y análisis de impacto
"El efecto de la alcalinidad y el contenido de MgO sobre la resistencia a la compresión y la porosidad". La resistencia a la compresión de los pellets es un indicador importante que refleja la presión que pueden soportar los pellets durante el proceso de transporte y almacenamiento y en el horno de reducción. Los altos hornos grandes requieren que la resistencia a la compresión de los pellets sea superior a 2500 N / pieza.
Bajo contenido natural de MgO, la resistencia a la compresión de los gránulos aumenta primero con el aumento de la alcalinidad. Cuando la alcalinidad aumenta a 0.2, la resistencia a la compresión de los gránulos aumenta de 2400 N / pieza de alcalinidad natural a 3,500 N / pieza; Después de alcanzar 0.4, la resistencia a la compresión de los gránulos ya no aumenta. Esto se debe al aumento de la alcalinidad de CaO, Fe2O3 y SiO2, como la ferrita de calcio y el silicato de calcio. La fase líquida adecuada favorece la recristalización de la hematita, pero demasiada fase líquida no favorece la mejora de la resistencia a la compresión de los gránulos. Bajo alcalinidad natural, la resistencia a la compresión de los gránulos disminuye con el aumento del contenido de MgO. Esto se debe a que la magnesita se descompone durante el precalentamiento y tostado de los gránulos, lo que aumenta la porosidad de los gránulos.
Cuando la alcalinidad y el MgO trabajan juntos, bajo el mismo contenido de MgO, el efecto de la alcalinidad sobre la resistencia a la compresión de los gránulos calcinados es básicamente el mismo que el efecto de la alcalinidad sobre la resistencia a la compresión de los gránulos bajo el contenido natural de MgO, es decir, la resistencia a la compresión de los gránulos. La fuerza primero aumenta con el aumento de la alcalinidad. Una vez que la alcalinidad alcanza un cierto valor, la resistencia a la compresión de los gránulos ya no aumenta significativamente; bajo la misma alcalinidad, la resistencia a la compresión de los gránulos disminuye con el aumento del contenido de MgO, lo que se debe al contenido de MgO.A medida que aumenta, la porosidad de los gránulos aumenta, y al mismo tiempo, el MgO entra en la fase de escoria para aumentar la punto de fusión de los minerales de la ganga, que tiene un cierto efecto inhibidor sobre la formación de la fase líquida. Los resultados de la prueba muestran que cuando la alcalinidad es superior a 0.2, la resistencia a la compresión de los gránulos de specularita con diferente alcalinidad y contenido de MgO puede alcanzar más de 2500 N / pieza.
A medida que aumenta la cantidad de fundente, también aumentan los poros que deja la descomposición del fundente durante el precalentamiento del tostado. La adición de fundente no solo afecta la composición química y la composición mineral de los gránulos, sino que también afecta la estructura y la porosidad de los gránulos. Esto afectará en cierta medida la resistencia a la compresión y las propiedades metalúrgicas de los gránulos.
El efecto de la alcalinidad y el contenido de MgO sobre el grado de reducción. El grado de reducción (RI) es un indicador importante para evaluar la tendencia y dificultad de remover oxígeno del mineral de hierro en las condiciones de temperatura y atmósfera en la zona de reducción del alto horno. Los factores que afectan el grado de reducción del mineral de hierro incluyen el tamaño de las partículas, la porosidad, la composición y estructura del mineral y la composición del mineral de ganga.
El grado de reducción de los gránulos ácidos con alcalinidad natural y contenido de MgO natural es bajo, solo 62.22%. Con el aumento del contenido de MgO, aumenta el grado de reducción. Cuando el contenido de MgO es del 3.0%, el grado de reducción de los gránulos puede alcanzar el 68%; Cuando el contenido de MgO aumenta la alcalinidad, el grado de reducción de los gránulos de specularita mejora enormemente. Cuando la alcalinidad aumenta a 1.2, el grado de reducción de los gránulos se eleva al 72.82%. Esto se debe a que la adición de piedra caliza aumenta la porosidad de los gránulos y, al mismo tiempo, el CaO reacciona con el Fe2O3 para formar ferrita de calcio que se reduce fácilmente.
Cuando la alcalinidad y el MgO actúan juntos, bajo la misma alcalinidad, el grado de reducción de los gránulos de mirrorite aumenta con el aumento del contenido de MgO; bajo el mismo contenido de MgO, el grado de reducción aumenta con el aumento de alcalinidad.
Cuando la alcalinidad alcanza 1.2 y el contenido de MgO aumenta al 3.0%, el grado de reducción de los gránulos es tan alto como 76.94%. Esto se debe a que la magnesita también aumenta la porosidad de los pellets durante el precalentamiento y tostado de los pellets, y el MgO puede aumentar el punto de fusión de la fase de escoria y el cuerpo flotante, por lo que no es fácil de fundir durante el proceso de reducción. y los poros de los gránulos no se funden. El material se llena para mantener una alta porosidad, lo que favorece la difusión del gas.
El efecto de la alcalinidad y el contenido de MgO sobre la expansión de la reducción.
Bajo el contenido de MgO natural, la tasa de expansión de reducción de los gránulos de specularita primero aumenta y luego disminuye, y la alcalinidad alcanza el valor máximo entre 0.4 y 0.6, y el valor máximo es tan alto como 32%.
Esto se debe a que una pequeña parte del CaO añadido a los gránulos reacciona con el Fe2O3 para producir ferrita de calcio y la mayor parte entra en la fase de escoria. Cuando no se reduce, la fase de escoria está dominada por el sistema binario CaO-SiO2. Cuando la alcalinidad está entre 0.4 y 0.6, es decir, el contenido de SiO2 en la fase de escoria está entre 62.5% y 70%, que es el intervalo de la composición del punto eutéctico binario del metasilicato de calcio (CaOSiO2) y SiO2, y su bajo El punto eutéctico de temperatura es de 1436 ℃, pero en condiciones reductoras, esta fase de escoria se convierte en un sistema ternario de escoria CaO-SiO2-FeO debido a la adición de FeO. En este sistema de escoria, la proporción de CaO y SiO2 permanece sin cambios. El punto de fusión de la fase de escoria aumenta bruscamente con el aumento del contenido de FeO. En el sistema de escoria ternaria pura, puede ser tan bajo como 1093 ℃, y la fase de escoria de bajo punto de fusión solo empeorará la reducción y expansión de los gránulos.
Bajo alcalinidad natural, la tasa de expansión de reducción de los gránulos disminuye ligeramente con el aumento del contenido de MgO, pero no es obvio. Esto se debe a la alcalinidad natural y la fase de escoria de gránulos de MgO natural con un punto de fusión de 1700 ℃ cuando el contenido de SiO2 es del 90%. Con la adición de MgO, la fase de escoria está dominada por el sistema binario MgO-SiO2, pero su temperatura eutéctica de baja temperatura también tiene una temperatura eutéctica baja. 1543 ° C. Cuando la alcalinidad y el MgO trabajan juntos, el efecto de la alcalinidad en la tasa de expansión de reducción de los gránulos es básicamente el mismo que el contenido de MgO natural con el mismo contenido de MgO. Cuando se añade MgO, el punto de fusión de la fase de escoria aumenta mediante la fusión del MgO en la fase de escoria. Al mismo tiempo, el punto de fusión de la fase de escoria también aumenta con MgO en la fase de escoria.
Por lo tanto, bajo la misma alcalinidad, el aumento del contenido de MgO puede reducir la expansión de la reducción.
La expansión de volumen de la hematita en los gránulos oxidados se reduce a magnetita y floatita. Esta expansión se debe principalmente al cambio de la estructura cristalina cuando la hematita se reduce a magnetita. La tasa de expansión de reducción de los gránulos está relacionada con la composición de la ganga y la capacidad de la fase de escoria para resistir el estrés generado por la reducción de partículas de hematita.
La fase de escoria de alto punto de fusión no es fácil de fundir durante el proceso de reducción, y mantener una alta resistencia puede limitar efectivamente la tasa de expansión de reducción de los gránulos, mientras que la fase de escoria de bajo punto de fusión empeorará la expansión de reducción de los gránulos.
La tasa de expansión de reducción de gránulos por debajo del 20% pertenece al rango de expansión normal, y la alcalinidad de los gránulos de specularita debe controlarse dentro del rango de menos de 0.2 o mayor o igual a 1.0.
Sin embargo, en la producción industrial general, se requiere que la tasa de expansión de reducción de los pellets se controle por debajo del 15%. Para gránulos de specularita con alcalinidad natural que contienen 3.0% ~ 3.1% SiO2, la tasa de expansión de reducción es menos del 15% y el grado de reducción es solo 62.2%. Cuando se mejora el grado de reducción aumentando la alcalinidad, es necesario reducir la alcalinidad Solo cuando el grado de aumento a 1.0 y el contenido de MgO al 3.0%, o la alcalinidad a 1.2 y el contenido de MgO ≥1.0%, se puede expandir la reducción la tasa sea inferior al 15%.
El efecto de la alcalinidad y el contenido de MgO en la pulverización por reducción a baja temperatura. La pulverización por reducción a baja temperatura (RDI) refleja la tendencia de los gránulos a producir polvo cuando se reducen en la parte superior del alto horno o en el horno de eje de reducción directa en un rango de temperatura de 400 ° C a 600 ° C. La razón principal de la reducción y pulverización a baja temperatura es la expansión de volumen y la distorsión de la red causada por la conversión de la estructura cristalina cuando la hematita se reduce a magnetita.
Hay tres métodos principales de unión que se forman cuando los gránulos se precalientan y tuestan:
Recristalización de óxido de hierro, unión de silicatos y unión de ferrita.
Entre ellos, la unión por recristalización de hematita es la más común y más fuerte, pero la hematita es extremadamente inestable en condiciones reductoras, mientras que la fase de unión de silicato se puede mantener cuando la hematita se reduce a magnetita. Cambiar.
Por lo tanto, es posible aumentar esta distribución uniforme y mantener una fase de unión estable en condiciones de reducción de baja temperatura mediante la adición de un fundente, para reducir la reducción y pulverización a baja temperatura de los gránulos de mirrorita.
Los gránulos con alcalinidad natural y contenido de MgO natural son principalmente hematites de consolidación por difusión en fase sólida, con menos fase de unión de silicato. Por lo tanto, se produce más polvo durante la reducción a baja temperatura y su valor de RDI-3.15 mm es tan alto como 12.75. %. Bajo el contenido de MgO natural, la alcalinidad aumentó a 0.2 y el valor de RDI-3.15 mm de la tasa de pulverización de reducción a baja temperatura del gránulo disminuyó rápidamente a 0.52%; la alcalinidad siguió aumentando y el valor de RDI-3.15 mm se mantuvo básicamente en aproximadamente 0.5%. Esto se debe a que la adición de CaO permite que los gránulos formen más fases líquidas de silicato que son estables durante la reducción a baja temperatura durante el precalentamiento y la calcinación, logrando así el propósito de reducir la reducción a baja temperatura y la pulverización de los gránulos.
Bajo alcalinidad natural, aumentando el contenido de MgO, la reducción a baja temperatura y la tasa de pulverización de los gránulos, RDI-3.15 mm, todos caen por debajo del 3.0%. Cuando la alcalinidad y el MgO trabajan juntos, el valor de RDI-3.15 mm de los gránulos en la pulverización de reducción a baja temperatura es bajo. La RDI-3.15 mm disminuye con el aumento de la alcalinidad y aumenta ligeramente con el aumento del contenido de MgO. Esto se debe al MgO que puede dificultar la formación de silicato en fase líquida.
El efecto de la alcalinidad y el contenido de MgO sobre las características de reflujo. Las características de fusión de los gránulos pueden reflejar la formación de gránulos en la zona de fusión blanda en la parte inferior del alto horno y su comportamiento en la zona de fusión blanda. Las características de reflujo de la carga tienen un mayor impacto en el funcionamiento del alto horno. La temperatura de ablandamiento de los gránulos es baja y el intervalo de reflujo es amplio, y la permeabilidad al aire de la zona de reflujo en la parte inferior del alto horno se reducirá, lo que no conduce a la convección del gas reductor y la carga y afecta seriamente el proceso de reducción.
Los gránulos de ácido con alcalinidad natural y contenido de MgO natural comienzan a ablandarse a 1009 ° C y la temperatura de caída es de 1272 ° C. Con el contenido de MgO natural, la alcalinidad aumenta a 1.2, la temperatura de ablandamiento de los gránulos aumenta a 1034 ° C, el intervalo de ablandamiento y el intervalo de ablandamiento se reducen y la temperatura de goteo también aumenta a 1299 ° C. Cuando la alcalinidad es 1.2, el aumento del contenido de MgO puede aumentar la temperatura de inicio del ablandamiento y la temperatura de goteo. Cuando el contenido de MgO es 1.0%, la temperatura de ablandamiento del gránulo aumentará a 1072 ℃, la temperatura de goteo alcanzará 1319 ℃, el contenido de MgO continuará aumentando y la temperatura de ablandamiento del gránulo no aumentará. .
Las características de reflujo de los gránulos se ven afectadas principalmente por las fases líquidas de bajo punto de fusión, como la fusterita y la escoria, producidas durante la reducción. Las malas características de reflujo a alta temperatura de los gránulos ácidos se deben principalmente al bajo punto de fusión de la fase de escoria de olivina rica en FeO durante el proceso de reducción, y la adición de MgO puede aumentar el punto de fusión de la fase de escoria. La formación de una solución sólida con un alto punto de fusión también desempeñará un papel en la mejora de las características de reflujo a alta temperatura de los gránulos.
Conserve la fuente y la dirección de este artículo para reimprimir: "Álcali" y "Magnesio" para mejorar el rendimiento de los pellets
Minhe Empresa de fundición a presión se dedican a fabricar y proporcionar piezas de fundición de calidad y alto rendimiento (la gama de piezas de fundición a presión de metal incluye principalmente Fundición a presión de pared delgada,Fundición a presión en cámara caliente,Fundición a presión de cámara fría), Servicio redondo (servicio de fundición a presión,Mecanizado cnc,Fabricación de moldes, Tratamiento de superficie) .Cualquier fundición a presión de aluminio personalizada, fundición a presión de magnesio o Zamak / zinc y otros requisitos de fundición pueden contactarnos.
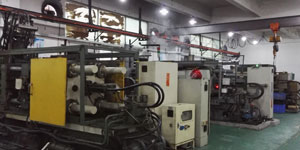
Bajo el control de ISO9001 y TS 16949, todos los procesos se llevan a cabo a través de cientos de máquinas de fundición a presión avanzadas, máquinas de 5 ejes y otras instalaciones, que van desde desintegradores hasta lavadoras Ultra Sonic.Minghe no solo cuenta con equipos avanzados, sino que también cuenta con profesionales equipo de ingenieros, operadores e inspectores experimentados para hacer realidad el diseño del cliente.
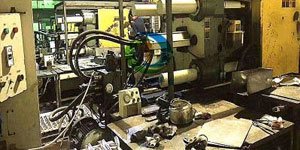
Fabricante por contrato de piezas de fundición a presión. Las capacidades incluyen piezas de fundición a presión de aluminio de cámara fría de 0.15 libras. a 6 libras, configuración de cambio rápido y mecanizado. Los servicios de valor agregado incluyen pulido, vibración, desbarbado, granallado, pintura, enchapado, revestimiento, ensamblaje y herramientas. Los materiales con los que se trabaja incluyen aleaciones como 360, 380, 383 y 413.
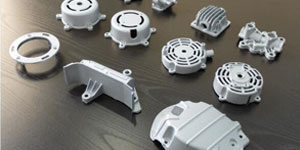
Asistencia en el diseño de fundición a presión de zinc / servicios de ingeniería simultáneos. Fabricante personalizado de piezas fundidas de zinc de precisión. Se pueden fabricar piezas de fundición en miniatura, piezas de fundición a presión de alta presión, piezas de fundición de moldes de deslizamiento múltiple, piezas de fundición de moldes convencionales, piezas de fundición unitaria e independiente y piezas de fundición selladas en cavidades. Las piezas fundidas se pueden fabricar en longitudes y anchos de hasta 24 pulgadas con una tolerancia de +/- 0.0005 pulgadas.
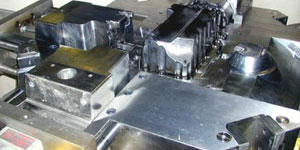
Fabricante certificado por ISO 9001: 2015 de magnesio fundido a presión, las capacidades incluyen fundición a presión de magnesio a alta presión de hasta 200 toneladas de cámara caliente y 3000 toneladas de cámara fría, diseño de herramientas, pulido, moldeado, mecanizado, pintura en polvo y líquida, control de calidad completo con capacidades de CMM , montaje, embalaje y entrega.
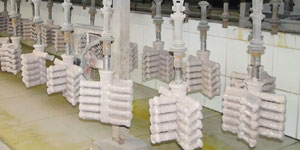
Certificado ITAF16949. El servicio de casting adicional incluye fundición de inversión,moldeo en arena,Fundición por gravedad, Fundición de espuma perdida,Fundición centrífuga,Fundición al vacío,Fundición de molde permanenteLas capacidades incluyen EDI, asistencia de ingeniería, modelado de sólidos y procesamiento secundario.
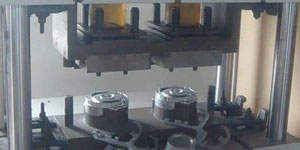
Industrias de fundición Estudios de casos de piezas para: automóviles, bicicletas, aeronaves, instrumentos musicales, embarcaciones, dispositivos ópticos, sensores, modelos, dispositivos electrónicos, carcasas, relojes, maquinaria, motores, muebles, joyas, plantillas, telecomunicaciones, iluminación, dispositivos médicos, dispositivos fotográficos, Robots, Esculturas, Equipos de sonido, Equipos deportivos, Herramientas, Juguetes y más.
¿Qué te podemos ayudar a hacer a continuación?
∇ Ir a la página de inicio para Fundición a presión China
→Piezas de fundición-Descubre lo que hemos hecho.
→ Consejos Ralated Acerca de Servicios de fundición a presión
By Fabricante de fundición a presión Minghe | Categorías: Artículos útiles |Material Tags: Fundición de aluminio, Fundición de zinc, Fundición de magnesio, Fundición de titanio, Fundición de acero inoxidable, Fundición de latón,Fundición de bronce,Casting de video,Historia de la empresa,Fundición a presión de aluminio | Comentarios desactivados