Fundición a presión: un caso compartido típico de la industria digital
La fundición a presión, también conocida como fundición a alta presión, es una tecnología de forma casi neta que se ha utilizado ampliamente en las industrias automotriz, aeroespacial y electrónica en los últimos años. En el proceso de fundición a presión, el metal fundido (generalmente aleación ligera) llena la cavidad a alta presión y alta velocidad bajo la acción del punzón, y se enfría rápidamente para formar la fundición final.
La fundición a presión se divide generalmente en fundición a presión en cámara fría y fundición a presión en cámara caliente. La fundición a presión en cámara fría se utiliza principalmente en la producción de piezas grandes, como piezas de automóvil, componentes de refrigeración de estaciones base de comunicación, etc .; La fundición a presión en cámara caliente se utiliza ampliamente en la producción de productos electrónicos pequeños o productos 3C. Procesos, como conectores USB, estuches para computadoras portátiles, etc.
1. La fundición a presión tiene una buena base para la automatización
En comparación con el proceso de fundición ordinario, la fundición a presión se caracteriza por su alta velocidad y alta presión. Los productos producidos son generalmente piezas de aleación ligera de paredes delgadas, pero la tecnología de fundición a presión también se aplica a la producción de rotores de cobre puro. A diferencia de las aleaciones de aluminio y magnesio, el cobre puro El punto de fusión es muy alto, por lo que la corta vida útil en el proceso de fundición a presión de cobre puro es un gran problema.
Entre todas las tecnologías de fundición, la fundición a presión tiene el mayor grado de automatización. Las empresas de fundición a presión modernas adoptan la tecnología de isla de fundición a presión automatizada, que integra en gran medida las máquinas de fundición a presión (generalmente docenas o incluso cientos) para formar un proceso de producción totalmente automatizado. Al mismo tiempo, se adopta la tecnología de fábrica inteligente para monitorear el proceso de producción de la máquina de fundición a presión, y el rendimiento y el estado de cada máquina de fundición a presión se pueden captar en tiempo real. A través de la medición de big data y la retroalimentación en tiempo real, el proceso de producción de la máquina de fundición a presión se puede ajustar a tiempo para garantizar la calidad final del producto.
El control en tiempo real de la temperatura del molde de fundición a presión es un ejemplo simple:
Tomemos como ejemplo la fundición a presión en cámara fría. En el proceso de producción, la temperatura del molde aumenta continuamente debido a que el metal líquido a alta temperatura llena continuamente la cavidad. En este momento, para asegurar que la temperatura del molde no se sobrecaliente, generalmente se usa agua de enfriamiento para pasar al molde para enfriarlo. Si el diseño de la tubería de agua de refrigeración es razonable, en términos generales, podemos asegurarnos de que la temperatura del molde alcance el llamado equilibrio térmico controlando la temperatura y el caudal del agua de refrigeración. Desde este punto de vista, podemos diseñar un sistema de retroalimentación de agua de refrigeración. Después de conocer el valor real de la temperatura del molde, la temperatura y el caudal del agua de refrigeración se pueden controlar mediante el cálculo y un sistema de retroalimentación instantánea, y finalmente se puede controlar la temperatura del molde. Esta es una aplicación típica de la fábrica inteligente de fundición a presión en esta etapa.
De hecho, el caso antes mencionado de control inteligente es solo un pequeño escenario de aplicación en la "fábrica inteligente". Hacer realidad una verdadera "fábrica inteligente" requiere la recopilación de una gran cantidad de datos de producción en tiempo real, entre los que juegan un papel decisivo los datos relacionados con la calidad del producto, como la densidad, la porosidad y las inclusiones oxidadas, porque estos datos son los indicadores que los clientes se preocupan más, y también son los indicadores básicos para medir si un elenco está calificado. En esta etapa, estos indicadores más críticos son los más difíciles de obtener, porque para los productos de aleación de metal, no podemos observar directamente la estructura interna del producto. El método adoptado por la mayoría de los fabricantes es comprobar las piezas fundidas, cortar en áreas clave claramente definidas por el cliente y luego observar directamente si hay problemas; otro método consiste en utilizar tecnología de inspección de rayos X bidimensional para escanear y escanear las posiciones locales de las piezas moldeadas muestreadas. Observación, el mayor problema con este método es que la información de fundición tridimensional se comprime en cortes bidimensionales, y la información obtenida por observación no puede reflejar completamente la situación real.
2. Control de calidad interno de las piezas de fundición
Con el desarrollo continuo de la industria del automóvil, los requisitos de calidad de las piezas y componentes son cada vez más altos. Los grandes fabricantes de automóviles continúan formulando requisitos para la calidad interna de piezas y componentes, y especifican cuantitativamente los estándares que pueden existir para defectos internos en las piezas. En este caso, los proveedores de componentes deben poder detectar y calibrar la distribución de defectos en todas las piezas fundidas en tiempo real durante el proceso de producción y comparar estándares para evaluar si las piezas fundidas cumplen con los requisitos.
Entonces, ¿cómo observar y registrar correctamente los defectos dentro de la fundición? La mejor tecnología en la tecnología existente es la tomografía computarizada, que es lo que comúnmente llamamos tecnología CT. La tecnología CT se ha utilizado ampliamente en el campo médico y la aplicación de la tecnología CT a la inspección industrial sigue siendo una tecnología que acaba de surgir en los últimos años.
Para aplicar la tecnología CT a la inspección de la calidad interna de las piezas fundidas, se deben cumplir los siguientes requisitos:
- La velocidad de inspección debe ser lo suficientemente alta para coincidir con el proceso de producción de piezas fundidas en tiempo real;
- La calidad de la imagen obtenida por la detección debe ser lo suficientemente buena para cooperar con el reconocimiento preciso de la imagen por el software posterior;
- En el caso de asegurar la precisión, el software o algoritmo que reconoce la imagen debe ser lo suficientemente rápido como para no retrasar el cronograma de producción.
Entre ellos, los dos primeros requisitos son para la detección de TC en sí, y el último es para el software o algoritmo de detección. Tomando una visión general de la tecnología CT actual, encontraremos que el instrumento de inspección más prometedor es el equipo Speed-Scan CT (Speed-Scan) producido por General Electric, y Volkswagen ha utilizado este equipo en Alemania para fundiciones reales. Detectado. Sin embargo, al observar la industria nacional de fundición a presión, el uso de tecnología CT en tiempo real para controlar la calidad de las piezas fundidas es un gran desafío desde una perspectiva operativa. La mayor limitación es el costo: el costo del equipo de inspección de CT es extremadamente alto y se utiliza para La línea de producción generalmente requiere una gran cantidad de equipo de inspección de CT, que la mayoría de las empresas nacionales no pueden pagar. Con el desarrollo continuo de la industria y la mejora continua de los requisitos de calidad de fundición, el uso de la tecnología CT para detectar la calidad interna de las piezas de fundición en tiempo real será un requisito general para los proveedores de OEM en el futuro.
3. Realimentación y ajuste del proceso
Bajo la premisa de que la fundición es inspeccionada por CT y se obtienen los datos sólidos tridimensionales, asumimos que existe un algoritmo que puede analizar los datos de una manera muy eficiente y dar toda la información sobre los defectos internos de la fundición, incluyendo tipo, tamaño y distribución, etc., luego podemos utilizar esta información para ajustar y modificar el proceso de producción en sí, y finalmente obtener piezas calificadas sin defectos excesivos. Este proceso, el proceso de obtener información de fundición y revisar el proceso, lo llamamos el proceso de retroalimentación y ajuste del proceso. Por supuesto, no podemos simplemente completar este proceso basándonos en la información de un casting. La situación más normal debería ser obtener información sobre un gran número de piezas fundidas y resolver los defectos de las piezas fundidas mediante análisis estadístico y métodos relacionados con el proceso.
La siguiente pregunta es, incluso si obtenemos una gran cantidad de información sobre la distribución de defectos dentro de la fundición, ¿cómo podemos ajustar los parámetros del proceso para evitar defectos no calificados? La herramienta de análisis más poderosa disponible es la simulación numérica por computadora, que también se conoce como tecnología de ingeniería asistida por computadora (CAE).
Usando tecnología de simulación por computadora, podemos realizar la producción virtual en un sentido local. Especialmente para la fundición a presión, podemos simular directamente el proceso de llenado y solidificación mediante el estudio de la velocidad, la presión, el patrón de flujo y las salpicaduras de la cavidad de llenado de fluido. Para juzgar si hay arrastre en el proceso de llenado; juzgar y estudiar los posibles puntos calientes, defectos de fundición (cavidad de contracción, porosidad de contracción) y el comportamiento del balance de calor de la fundición a presión calculando los cambios de temperatura de la fundición y el molde en diferentes condiciones del ciclo de fundición a presión. A través de este tipo de tecnología de simulación numérica, basada en ciertas condiciones de análisis, podemos juzgar y evitar los defectos internos de la fundición en gran medida, mejorar el rendimiento de la fundición y aumentar en gran medida la eficiencia de producción, y lograr la retroalimentación y corrección del proceso. discutimos antes. propósito.
Encadenamos todo el proceso: utilizamos tecnología digital (CT) para detectar los datos de defectos tridimensionales del producto en tiempo real, y si el producto no está calificado, los datos se transmitirán al centro de análisis CAE y a la simulación analógica. la tecnología se utilizará para analizar y producir soluciones de problemas de defectos, y la retroalimentación de la solución. Vaya al principio de la producción y el proceso para ejecutar y volver a obtener el producto. El producto continúa sometido a inspección digital y obtiene datos de defectos tridimensionales. Si el producto está calificado, la iteración finaliza; de lo contrario, continúa.
4. Domina la tecnología digital central
Se puede ver que el análisis CAE juega un papel clave en este proceso, y la efectividad de la solución propuesta tendrá un impacto en la eficiencia de todo el proceso. De hecho, si puede dominar el núcleo de la tecnología CAE y si puede aplicar bien la tecnología de simulación numérica en la producción real, puede medir las capacidades técnicas de una empresa de fundición a presión en gran medida, porque la tecnología digital es imprescindible para la empresa Road. , cuanto antes domine el núcleo de la tecnología digital en este camino, más podrá destacar en la futura competencia corporativa.
Por lo tanto, si la tecnología de inspección digital y la tecnología de análisis CAE se aplican bien a las empresas de fundición a presión existentes, podemos ver una escena de fábrica digital completa y típica. Entre ellos, la tecnología de detección digital realiza la digitalización de entidades físicas, mientras que la tecnología de análisis CAE transforma la información digital obtenida de la detección en soluciones de problemas basadas en la producción virtual. En este proceso, la detección digital es en realidad un proceso totalmente automatizado, mientras que el análisis CAE todavía necesita la participación humana. Si el análisis CAE se puede solidificar en un algoritmo y completamente automatizado, entonces esta es la forma embrionaria de la futura fábrica digital inteligente.
Página relacionada: consulta de fundición a presión/servicios de fundición a presión/video de fundición a presión/productos de fundición a presión
Artículos relacionados:
- ¿Qué es la prueba de moldes para fundición a presión?
- El control de calidad de las piezas de aleación de aluminio de fundición a presión
- ¿Qué es la presión de fundición a presión?
- El análisis del proceso de piezas automotrices de fundición a presión de nuevo tipo
Conserve la fuente y la dirección de este artículo para reimprimir:Fundición a presión: un caso compartido típico de la industria digital
Minhe Empresa de fundición a presión se dedican a fabricar y proporcionar piezas de fundición de calidad y alto rendimiento (la gama de piezas de fundición a presión de metal incluye principalmente Fundición a presión de pared delgada,Fundición a presión en cámara caliente,Fundición a presión de cámara fría), Servicio redondo (servicio de fundición a presión,Mecanizado cnc,Fabricación de moldes, Tratamiento de superficie) .Cualquier fundición a presión de aluminio personalizada, fundición a presión de magnesio o Zamak / zinc y otros requisitos de fundición pueden contactarnos.
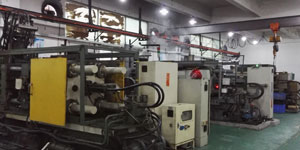
Bajo el control de ISO9001 y TS 16949, todos los procesos se llevan a cabo a través de cientos de máquinas de fundición a presión avanzadas, máquinas de 5 ejes y otras instalaciones, que van desde desintegradores hasta lavadoras Ultra Sonic.Minghe no solo cuenta con equipos avanzados, sino que también cuenta con profesionales equipo de ingenieros, operadores e inspectores experimentados para hacer realidad el diseño del cliente.
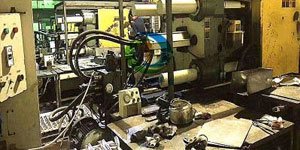
Fabricante por contrato de piezas de fundición a presión. Las capacidades incluyen piezas de fundición a presión de aluminio de cámara fría de 0.15 libras. a 6 libras, configuración de cambio rápido y mecanizado. Los servicios de valor agregado incluyen pulido, vibración, desbarbado, granallado, pintura, enchapado, revestimiento, ensamblaje y herramientas. Los materiales con los que se trabaja incluyen aleaciones como 360, 380, 383 y 413.
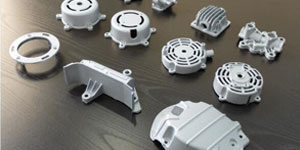
Asistencia en el diseño de fundición a presión de zinc / servicios de ingeniería simultáneos. Fabricante personalizado de piezas fundidas de zinc de precisión. Se pueden fabricar piezas de fundición en miniatura, piezas de fundición a presión de alta presión, piezas de fundición de moldes de deslizamiento múltiple, piezas de fundición de moldes convencionales, piezas de fundición unitaria e independiente y piezas de fundición selladas en cavidades. Las piezas fundidas se pueden fabricar en longitudes y anchos de hasta 24 pulgadas con una tolerancia de +/- 0.0005 pulgadas.
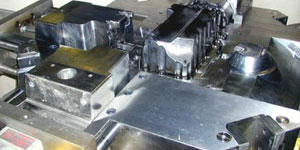
Fabricante certificado por ISO 9001: 2015 de magnesio fundido a presión, las capacidades incluyen fundición a presión de magnesio a alta presión de hasta 200 toneladas de cámara caliente y 3000 toneladas de cámara fría, diseño de herramientas, pulido, moldeado, mecanizado, pintura en polvo y líquida, control de calidad completo con capacidades de CMM , montaje, embalaje y entrega.
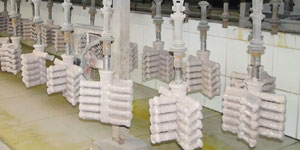
Certificado ITAF16949. El servicio de casting adicional incluye fundición de inversión,moldeo en arena,Fundición por gravedad, Fundición de espuma perdida,Fundición centrífuga,Fundición al vacío,Fundición de molde permanenteLas capacidades incluyen EDI, asistencia de ingeniería, modelado de sólidos y procesamiento secundario.
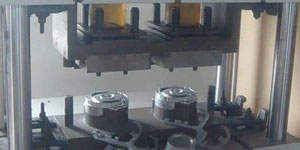
Industrias de fundición Estudios de casos de piezas para: automóviles, bicicletas, aeronaves, instrumentos musicales, embarcaciones, dispositivos ópticos, sensores, modelos, dispositivos electrónicos, carcasas, relojes, maquinaria, motores, muebles, joyas, plantillas, telecomunicaciones, iluminación, dispositivos médicos, dispositivos fotográficos, Robots, Esculturas, Equipos de sonido, Equipos deportivos, Herramientas, Juguetes y más.
¿Qué te podemos ayudar a hacer a continuación?
∇ Ir a la página de inicio para Fundición a presión China
→Piezas de fundición-Descubre lo que hemos hecho.
→ Consejos Ralated Acerca de Servicios de fundición a presión
By Fabricante de fundición a presión Minghe | Categorías: Artículos útiles |Material Tags: Fundición de aluminio, Fundición de zinc, Fundición de magnesio, Fundición de titanio, Fundición de acero inoxidable, Fundición de latón,Fundición de bronce,Casting de video,Historia de la empresa,Fundición a presión de aluminio | Comentarios desactivados