Las precauciones para la fundición en arena de vidrio de agua
¿Cuáles son los factores que afectan el "envejecimiento" del vidrio soluble? ¿Cómo eliminar el "envejecimiento" del vaso de agua?
El vaso de agua recién preparado es una verdadera solución. Sin embargo, durante el proceso de almacenamiento, el ácido silícico en el vaso soluble se someterá a polimerización por condensación, que gradualmente se policondensará de la solución verdadera a una solución de ácido silícico macromolecular y finalmente se convertirá en un gel de ácido silícico. Por lo tanto, el vidrio soluble es en realidad una mezcla heterogénea compuesta por ácido polisilícico con diferentes grados de polimerización, que se ve fácilmente afectado por su módulo, concentración, temperatura, contenido de electrolitos y tiempo de almacenamiento.
Durante el almacenamiento, las moléculas de vidrio soluble se someten a polimerización por condensación para formar un gel, y su fuerza de unión disminuye gradualmente con la extensión del tiempo de almacenamiento. Este fenómeno se denomina "envejecimiento" del vidrio soluble.
El fenómeno de "envejecimiento" se puede explicar por los siguientes dos conjuntos de datos de prueba: vidrio soluble de alto módulo (M = 2.89, ρ = 1.44 g / cm3) después de 20, 60, 120, 180, 240 días de almacenamiento, el CO2 endurecido Se sopla un vaso de agua. La resistencia a la tracción en seco de la arena desciende correspondientemente en un 9.9%, 14%, 23.5%, 36.8% y 40%; El silicato de sodio de bajo módulo (M = 2.44, ρ = 1.41 g / cm3) se almacena durante 7, 30, 60 y 90 días después de secarse. La resistencia a la tracción disminuyó en un 4.5%, 5%, 7.3% y 11% respectivamente.
El tiempo de almacenamiento del vidrio soluble tiene poco efecto sobre la resistencia inicial de la arena autoendurecible para vidrio soluble endurecida con éster, pero tiene un efecto significativo sobre la resistencia posterior. Según las mediciones, se reduce en aproximadamente un 60% para el vidrio soluble de alto módulo y un 15-20% para el vidrio soluble de bajo módulo. . La resistencia residual también disminuye con la extensión del tiempo de almacenamiento.
Durante el almacenamiento de vidrio soluble se produce al mismo tiempo la policondensación y despolimerización del ácido polisilícico, se desproporciona el peso molecular y finalmente se forma un sistema multidispersado en el que coexisten el ácido monoortosilícico y las partículas coloidales. Es decir, durante el proceso de envejecimiento del vidrio soluble, el grado de polimerización del ácido silícico es desproporcionado y el contenido de ácido monoortosilícico y alto contenido de ácido polisilícico aumenta con la extensión del tiempo de almacenamiento. Como resultado de la polimerización por condensación y la reacción de despolimerización del vidrio soluble durante el almacenamiento, la fuerza de unión se reduce, es decir, se produce el fenómeno de "envejecimiento".
Los principales factores que afectan el "envejecimiento" del vidrio soluble son: tiempo de almacenamiento, módulo y concentración del vidrio soluble. Cuanto mayor es el tiempo de almacenamiento, mayor es el módulo y mayor la concentración, más grave es el "envejecimiento".
El vaso de agua existente desde hace mucho tiempo se puede modificar de diversas formas para eliminar el "envejecimiento" y restaurar el vaso de agua al rendimiento del vaso de agua dulce:
1. Modificación física
El envejecimiento del vaso de agua es un proceso espontáneo que libera energía lentamente. La modificación física del vidrio soluble "envejecido" consiste en utilizar un campo magnético, ultrasonido, alta frecuencia o calentamiento para proporcionar energía al sistema de vidrio soluble y promover la alta polimerización del pegamento de polisilicato. Las partículas se vuelven a despolimerizar y promueven la homogeneización del peso molecular del ácido polisilícico, eliminando así el fenómeno del envejecimiento, que es el mecanismo de modificación física. Por ejemplo, después del tratamiento con un campo magnético, la fuerza de la arena de silicato de sodio aumenta en un 20-30%, la cantidad de silicato de sodio agregado se reduce en un 30-40%, se ahorra CO2, se mejora la colapsabilidad y hay buenas beneficios económicos.
La desventaja de la modificación física es que no es duradera y la fuerza de unión disminuirá cuando se almacena después del tratamiento, por lo que es adecuado para su uso lo antes posible después del tratamiento en la fundición. Especialmente para el vidrio soluble con M> 2.6, la concentración de moléculas de ácido silícico es grande y, después de la modificación física y la despolimerización, se policondensará con relativa rapidez. Es mejor usarlo inmediatamente después del tratamiento.
2. Modificación química
La modificación química consiste en agregar una pequeña cantidad de compuestos al vaso soluble, todos estos compuestos contienen carboxilo, amida, carbonilo, hidroxilo, éter, amino y otros grupos polares, que se adsorben en moléculas de ácido silícico o partículas coloidales a través de enlaces de hidrógeno o estática. electricidad. Superficie, cambia su energía potencial de superficie y capacidad de solvatación, mejora la estabilidad del ácido polisilícico, evitando así que prosiga el "envejecimiento".
Por ejemplo, agregar poliacrilamida, almidón modificado, polifosfato, etc. al vaso soluble puede lograr mejores resultados.
La incorporación de materia orgánica en un vaso de agua ordinario o incluso un vaso de agua modificado puede desempeñar una variedad de funciones, tales como: cambiar las propiedades de flujo viscoso del vaso de agua; mejorar el rendimiento de modelado de mezclas de vidrio soluble; aumentando la fuerza de unión para que el vidrio soluble se agregue absolutamente La cantidad se reduce; se mejora la plasticidad del gel de ácido silícico; la resistencia residual se reduce, por lo que la arena de vidrio soluble es más adecuada para hierro fundido y aleaciones no ferrosas.
3. Modificación físico-química
La modificación física es adecuada para el vidrio soluble "envejecido" y se puede utilizar inmediatamente después de la modificación. La modificación química es adecuada para procesar vidrio de agua dulce, y el vidrio de agua modificado se puede almacenar durante mucho tiempo. La combinación de modificación física y modificación química puede hacer que el vaso soluble tenga un efecto de modificación duradero. Por ejemplo, agregar poliacrilamida al autoclave para modificar el vidrio soluble "envejecido" tiene un buen efecto. Entre ellos, se utilizan la presión y la presión del autoclave. La agitación es una modificación física y la adición de poliacrilamida es una modificación química.
¿Cómo evitar la formación de tiza en la superficie del molde (núcleo) de arena de silicato de sodio endurecido por soplado de CO2?
Después de soplar arena de silicato de sodio y soda, se endurece con CO2 y se deja por un período de tiempo, a veces aparece una sustancia como escarcha en la superficie del molde inferior (núcleo), lo que reducirá seriamente la resistencia de la superficie del lugar y producirá arena fácilmente. defectos de lavado durante el vertido. Según el análisis, el componente principal de esta sustancia blanca es el NaHCO3, que puede ser causado por un exceso de humedad o CO2 en la arena de silicato de sodio. La reacción es la siguiente:
- Na2CO3 + H2O → NaHCO3 + NaOH
- Na2O+2CO2+H2O→2NaHCO3
- El NaHCO3 migra fácilmente hacia el exterior con la humedad, lo que produce polvo como escarcha en la superficie del molde y el núcleo.
La solución es la siguiente:
- Controle que el contenido de humedad de la arena de silicato de sodio no sea demasiado alto (especialmente en la temporada de lluvias y el invierno).
- El tiempo para soplar CO2 no debería ser demasiado largo.
- El molde y el núcleo endurecidos no deben colocarse durante mucho tiempo, y deben moldearse y verterse a tiempo.
- Agregar alrededor del 1% (fracción de masa) del jarabe con una densidad de 1.3 g / cm3 a la arena de silicato de sodio puede prevenir eficazmente que la superficie se empolve.
¿Cómo mejorar la resistencia a la absorción de humedad del molde de arena de vidrio soluble (núcleo)?
El núcleo de arena de vidrio de agua con gas endurecido por CO2 o métodos de calentamiento se ensambla en el molde de arcilla húmeda. Si no se vierte a tiempo, la resistencia del núcleo de arena disminuirá drásticamente, no solo puede deslizarse, incluso colapsar; se almacena en un ambiente húmedo La resistencia del núcleo de arena también se reduce significativamente. La Tabla 1 muestra los valores de resistencia de los núcleos de arena de vidrio soluble de sodio endurecido con CO2 cuando se colocan en un ambiente con una humedad relativa del 97% durante 24 horas. La razón de la pérdida de resistencia cuando se almacena en un ambiente húmedo se debe a la rehidratación del vidrio soluble con sodio. El Na + y OH— en la matriz aglutinante de silicato de sodio absorben humedad y erosionan la matriz, finalmente rompiendo el enlace silicio-oxígeno Si-O-Si, resultando en una disminución significativa en la fuerza de unión de la arena de silicato de sodio.
Las medidas para solucionar este problema son:
- 1. Vaso soluble de litio se agrega al vidrio soluble de sodio, o Li2CO3, CaCO3, ZnCO3 y otros aditivos inorgánicos se agregan al vidrio soluble de sodio, porque se pueden formar carbonatos y silicatos relativamente insolubles y se pueden reducir los iones de sodio libres Por lo tanto, la humedad Se puede mejorar la resistencia a la absorción del aglutinante de vidrio soluble de sodio.
- 2. Agregue una pequeña cantidad de material orgánico o materia orgánica con función tensioactiva al vaso de agua de sodio. Cuando el aglutinante se endurece, los iones hidrófilos Na + y OH- en el gel de vidrio soluble de sodio pueden sustituirse por grupos orgánicos hidrófobos, o combinados entre sí, la base orgánica hidrófoba expuesta mejora la absorción de humedad.
- 3. Mejore el módulo del vidrio soluble, porque la resistencia a la humedad del vidrio soluble de alto módulo es más fuerte que la del vidrio soluble de bajo módulo.
- 4. Agregue hidrolizado de almidón a arena de silicato de sodio. Un mejor método es usar hidrolizado de almidón para modificar el vidrio soluble con sodio.
4 ¿Cuáles son las características del proceso compuesto de arena de resina fenólica alcalina de vidrio de agua endurecida por soplado de CO2?
En los últimos años, para mejorar la calidad de las piezas fundidas de acero, algunas pequeñas y medianas empresas necesitan adoptar con urgencia el proceso de arena de resina. Sin embargo, debido a la limitada capacidad económica, no pueden comprar equipos de regeneración de arena de resina y la arena vieja no se puede reciclar ni reutilizar, lo que genera altos costos de producción. Para encontrar una manera eficaz de mejorar la calidad de las piezas fundidas sin aumentar demasiado el costo, se pueden combinar las características del proceso de arena de silicato de sodio endurecida por soplado con CO2 y arena de resina fenólica alcalina endurecida por soplado con CO2, y silicato de sodio endurecido por soplado con CO2 (alcalino) Se puede utilizar resina fenólica. El proceso de composición de arena de resina utiliza arena de resina fenólica alcalina como arena de superficie y arena de vidrio soluble como arena de fondo, mientras se sopla CO2 para el endurecimiento.
La resina fenólica utilizada en la arena de resina fenólica alcalina de CO2 se fabrica mediante policondensación de fenol y formaldehído bajo la acción de un catalizador alcalino fuerte y la adición de un agente de acoplamiento. Su valor de PH es ≥13 y su viscosidad es ≤500mPa • s. La cantidad de resina fenólica añadida a la arena es del 3% al 4% (fracción de masa). Cuando el caudal de CO2 es de 0.8 ~ 1.0 m3 / h, el mejor tiempo de soplado es de 30 ~ 60 s; si el tiempo de soplado es demasiado corto, la resistencia al endurecimiento del núcleo de arena será baja; si el tiempo de soplado es demasiado largo, la resistencia del núcleo de arena no aumentará y es gas desperdiciado.
CO2: la arena de resina fenólica alcalina no contiene elementos nocivos como N, P, S, etc., por lo que se eliminan los defectos de fundición como poros, microfisuras superficiales, etc. causados por estos elementos; durante el vertido no se liberan gases nocivos como H2S y SO2, lo que es beneficioso para la protección del medio ambiente; Buena capacidad de plegado, fácil de limpiar; alta precisión dimensional; alta eficiencia de producción.
El proceso compuesto de arena de resina fenólica alcalina-vidrio de agua endurecido por soplado de CO2 puede ser ampliamente utilizado en piezas de acero, hierro, aleaciones de cobre y aleaciones ligeras.
El proceso compuesto es un proceso sencillo y conveniente. El proceso es el siguiente: primero mezcle arena de resina y arena de silicato de sodio por separado, y luego colóquelos en dos cubos de arena; luego agregue la arena de resina mezclada como arena superficial en la caja de arena y libra, el espesor de la capa de arena superficial es generalmente de 30-50 mm; luego se agrega arena de vidrio soluble para hacer que la arena posterior se llene y compacte; finalmente, se sopla gas CO2 en el molde para su endurecimiento.
El diámetro del tubo de soplado es generalmente de 25 mm y el rango de endurecimiento es aproximadamente 6 veces el diámetro del tubo de soplado.
El tiempo de soplado depende del tamaño, la forma, el flujo de gas y el área del tapón de escape del molde de arena (núcleo). Generalmente, el tiempo de soplado se controla entre 15 y 40 segundos.
Después de soplar el molde de arena dura (núcleo), se puede tomar el molde. La fuerza del molde de arena (núcleo) aumenta rápidamente. Cepille la pintura dentro de la media hora después de tomar el molde y cierre la caja para verter después de 4 horas.
El proceso compuesto es particularmente adecuado para plantas de fundición de acero que no tienen equipos de regeneración de arena de resina y necesitan producir piezas de fundición de alta calidad. El proceso es simple y fácil de controlar, y la calidad de las piezas moldeadas producidas es equivalente a la de otras piezas moldeadas en arena de resina.
La arena de silicato de sodio endurecida por soplado con CO2 también se puede combinar con arena de resina de poliacrilato de sodio endurecida por soplado con CO2 para la producción de diversas piezas fundidas de alta calidad.
¿Cuáles son los pros y los contras del proceso de arena de silicato de sodio endurecido compuesto de éster orgánico de CO2?
En los últimos años, el proceso de arena de silicato de sodio endurecido con compuesto de éster orgánico de CO2 tiene una tendencia a expandir sus aplicaciones. El proceso es el siguiente: agregue una cierta cantidad de éster orgánico durante la mezcla de arena (generalmente la mitad de la cantidad normal requerida o 4 ~ 6% del peso del vidrio soluble); una vez completado el modelado, aplique CO2 para endurecer hasta alcanzar la resistencia al desmoldeo (generalmente se requiere resistencia a la compresión). La resistencia es de aproximadamente 0.5 MPa); después del desmoldeo, el éster orgánico continúa endureciéndose y la resistencia de la arena de moldeo aumenta a un ritmo más rápido; Después de que el CO2 se sopla y se coloca durante 3 ~ 6 h, el molde de arena se puede combinar y verter.
El mecanismo de endurecimiento es:
Cuando la arena de vidrio soluble sopla CO2, bajo la acción de la diferencia de presión del gas y la diferencia de concentración, el gas CO2 intentará fluir en todas las direcciones de la arena de moldeo. Después de que el gas CO2 entra en contacto con el vaso de agua, reacciona inmediatamente con él para formar un gel. Debido al efecto de difusión, la reacción es siempre de afuera hacia adentro, y la capa externa primero forma una película de gel, lo que evita que el gas CO2 y el vidrio soluble sigan reaccionando. Por lo tanto, en poco tiempo, no importa qué método se utilice para controlar el gas CO2, es imposible hacerlo reaccionar con todo el vidrio soluble. Según el análisis, cuando la arena de moldeo alcanza la mejor fuerza de soplado, el vidrio soluble que reacciona con el gas CO2 es aproximadamente del 65%. Esto significa que el vaso soluble no ejerce completamente su efecto adhesivo y al menos el 35% del vaso soluble no reacciona. El endurecedor de éster orgánico puede formar una mezcla uniforme con el aglutinante y puede dar pleno juego al efecto de unión del aglutinante. Todas las partes de la arena del núcleo se fortalecen a la misma velocidad.
Aumentar la cantidad de vidrio soluble que se agrega aumentará la resistencia final del molde de arena, pero también aumentará su resistencia residual, lo que dificultará la limpieza de la arena. Cuando la cantidad agregada de vidrio soluble es demasiado pequeña, la resistencia final es demasiado pequeña y no puede cumplir con los requisitos de uso. En la producción real, la cantidad de vidrio soluble que se agrega generalmente se controla en alrededor del 4%.
Cuando se usa un éster orgánico solo para endurecer, la cantidad general de éster orgánico que se agrega es del 8 al 15% de la cantidad de vidrio soluble. Cuando se usa endurecimiento compuesto, se estima que aproximadamente la mitad del vaso soluble se ha endurecido cuando se sopla CO2, y aproximadamente la mitad del vaso soluble aún no se ha endurecido. Por lo tanto, es más apropiado que la cantidad de ésteres orgánicos represente del 4 al 6% de la cantidad de vidrio soluble.
El método de endurecimiento compuesto puede aprovechar al máximo las ventajas duales del endurecimiento por CO2 y el endurecimiento por éster orgánico, y puede ejercer completamente el efecto de unión del vidrio soluble para lograr una velocidad de endurecimiento rápida, un desmoldeo temprano, alta resistencia, buena capacidad de colapso y bajo costo. Efecto integral.
Sin embargo, el proceso de endurecimiento del compuesto de éster orgánico de CO2 necesita agregar 0.5 a 1% más de vidrio soluble que el método de endurecimiento del éster orgánico simple, lo que aumentará la dificultad de la regeneración de la arena de vidrio soluble usada.
¿Por qué es fácil producir arena pegajosa cuando se utiliza el proceso de arena de silicato de sodio para producir piezas de fundición de hierro? ¿Cómo prevenirlo?
Cuando el molde de arena (núcleo) hecho de arena de silicato de sodio se usa para verter fundiciones de hierro, a menudo se produce arena pegajosa, lo que limita su aplicación en la producción de hierro fundido.
El Na2O, SiO2 en la arena de silicato de sodio y el óxido de hierro producido por el metal líquido durante el vertido forman un silicato de bajo punto de fusión. Como se mencionó anteriormente, si este compuesto contiene más vidrio amorfo fusible, la fuerza de unión entre esta capa de vidrio y la superficie de la pieza fundida es muy pequeña y el coeficiente de contracción es diferente al del metal. La tensión grande es fácil de eliminar de la superficie de la fundición sin que la arena se pegue. Si el compuesto formado en la superficie de la fundición tiene un alto contenido de SiO2 y un bajo contenido de FeO, MnO, etc., su estructura solidificada tiene básicamente una estructura cristalina, que se combinará firmemente con la fundición, dando como resultado arena pegajosa. .
Cuando la arena de silicato de sodio se utiliza para producir piezas de fundición de hierro, debido a la baja temperatura de vertido y el alto contenido de carbono de las piezas de fundición de hierro, el hierro y el manganeso no se oxidan fácilmente y la capa de arena pegajosa resultante tiene una estructura cristalina y es difícil para establecer una capa adecuada entre las piezas de hierro fundido y la capa de arena pegajosa. El grosor de la capa de óxido de hierro es diferente al de la arena de resina entre la fundición y la capa de arena pegajosa, que puede producir una película de carbono brillante a través de la pirólisis de resina cuando se producen fundiciones de hierro, por lo que la capa de arena pegajosa no es fácil de quitar.
Para evitar la producción de arena de vidrio de agua con gas a partir de la producción de piezas de fundición de hierro, se pueden utilizar revestimientos adecuados. Como la pintura a base de agua, la superficie debe secarse después de pintar, por lo que la pintura de secado rápido a base de alcohol es la mejor.
En general, las piezas de fundición de hierro también pueden agregar una cantidad apropiada de polvo de carbón (como 3% a 6%) (fracción de masa) a la arena de silicato de sodio, de modo que la pirólisis del polvo de carbón entre la pieza de fundición y la capa de arena pueda producir una película de carbono brillante. No se moja con metales y sus óxidos, por lo que la capa de arena pegajosa se desprende fácilmente de la pieza fundida.
¿Se espera que la arena de silicato de sodio se convierta en arena de moldeo ecológica sin descarga de arena residual?
El vaso de agua es incoloro, inodoro y no tóxico. No causará problemas graves si toca la piel y la ropa y se enjuaga con agua, pero se debe evitar salpicar en los ojos. El vidrio soluble no tiene gases irritantes o nocivos liberados durante la mezcla de arena, modelado, endurecimiento y vertido, y no hay contaminación negra ni ácida. Sin embargo, si el proceso es inadecuado y se agrega demasiado silicato de sodio, la capacidad de colapso de la arena de silicato de sodio no será buena y el polvo volará durante la limpieza de la arena, lo que también causará contaminación. Al mismo tiempo, es difícil regenerar la arena vieja y la descarga de arena residual causa contaminación alcalina al medio ambiente.
Si estos dos problemas pueden superarse, la arena de silicato de sodio puede convertirse en arena de moldeo ecológica sin descarga de arena residual.
La medida fundamental para solucionar estos dos problemas es reducir la cantidad de agua de vidrio añadida a menos del 2%, que básicamente puede sacudir la arena. Cuando se reduce la cantidad de vidrio soluble añadido, también se reduce el Na2O residual en la arena vieja. Utilizando un método de regeneración en seco relativamente simple, es posible mantener el Na2O residual en la arena circulante por debajo del 0.25%. Esta arena recuperada puede cumplir con los requisitos de aplicación de arena de moldeo simple para piezas fundidas de acero de tamaño pequeño y mediano. En este momento, incluso si la vieja arena de silicato de sodio no usa el costoso y complicado método húmedo para regenerar, pero se usa el método seco relativamente simple y barato, se puede reciclar por completo, básicamente no se descarga arena residual, y la proporción de arena para planchar Se puede reducir a menos de 1: 1.
¿Cómo regenerar eficazmente la arena de silicato de sodio?
Si el Na2O residual en la vieja arena de silicato de sodio es demasiado alto, después de agregar el silicato de sodio a la arena, la arena de moldeo no tendrá suficiente tiempo de uso y la acumulación de demasiado Na2O deteriorará la refractariedad de la arena de cuarzo. Por lo tanto, el Na2O residual debe eliminarse tanto como sea posible al regenerar la arena de silicato de sodio usada.
Conserve la fuente y la dirección de este artículo para reimprimir: Las precauciones para la fundición en arena de vidrio de agua
Minhe Empresa de fundición a presión se dedican a fabricar y proporcionar piezas de fundición de calidad y alto rendimiento (la gama de piezas de fundición a presión de metal incluye principalmente Fundición a presión de pared delgada,Fundición a presión en cámara caliente,Fundición a presión de cámara fría), Servicio redondo (servicio de fundición a presión,Mecanizado cnc,Fabricación de moldes, Tratamiento de superficie) .Cualquier fundición a presión de aluminio personalizada, fundición a presión de magnesio o Zamak / zinc y otros requisitos de fundición pueden contactarnos.
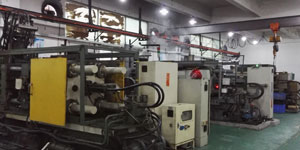
Bajo el control de ISO9001 y TS 16949, todos los procesos se llevan a cabo a través de cientos de máquinas de fundición a presión avanzadas, máquinas de 5 ejes y otras instalaciones, que van desde desintegradores hasta lavadoras Ultra Sonic.Minghe no solo cuenta con equipos avanzados, sino que también cuenta con profesionales equipo de ingenieros, operadores e inspectores experimentados para hacer realidad el diseño del cliente.
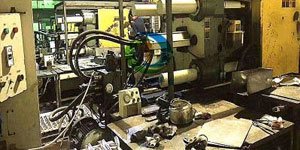
Fabricante por contrato de piezas de fundición a presión. Las capacidades incluyen piezas de fundición a presión de aluminio de cámara fría de 0.15 libras. a 6 libras, configuración de cambio rápido y mecanizado. Los servicios de valor agregado incluyen pulido, vibración, desbarbado, granallado, pintura, enchapado, revestimiento, ensamblaje y herramientas. Los materiales con los que se trabaja incluyen aleaciones como 360, 380, 383 y 413.
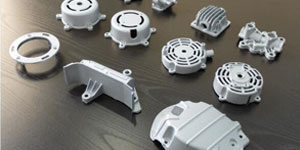
Asistencia en el diseño de fundición a presión de zinc / servicios de ingeniería simultáneos. Fabricante personalizado de piezas fundidas de zinc de precisión. Se pueden fabricar piezas de fundición en miniatura, piezas de fundición a presión de alta presión, piezas de fundición de moldes de deslizamiento múltiple, piezas de fundición de moldes convencionales, piezas de fundición unitaria e independiente y piezas de fundición selladas en cavidades. Las piezas fundidas se pueden fabricar en longitudes y anchos de hasta 24 pulgadas con una tolerancia de +/- 0.0005 pulgadas.
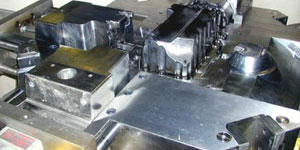
Fabricante certificado por ISO 9001: 2015 de magnesio fundido a presión, las capacidades incluyen fundición a presión de magnesio a alta presión de hasta 200 toneladas de cámara caliente y 3000 toneladas de cámara fría, diseño de herramientas, pulido, moldeado, mecanizado, pintura en polvo y líquida, control de calidad completo con capacidades de CMM , montaje, embalaje y entrega.
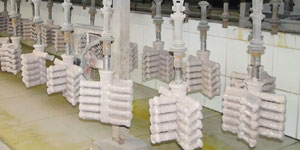
Certificado ITAF16949. El servicio de casting adicional incluye fundición de inversión,moldeo en arena,Fundición por gravedad, Fundición de espuma perdida,Fundición centrífuga,Fundición al vacío,Fundición de molde permanenteLas capacidades incluyen EDI, asistencia de ingeniería, modelado de sólidos y procesamiento secundario.
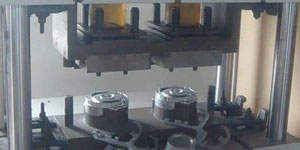
Industrias de fundición Estudios de casos de piezas para: automóviles, bicicletas, aeronaves, instrumentos musicales, embarcaciones, dispositivos ópticos, sensores, modelos, dispositivos electrónicos, carcasas, relojes, maquinaria, motores, muebles, joyas, plantillas, telecomunicaciones, iluminación, dispositivos médicos, dispositivos fotográficos, Robots, Esculturas, Equipos de sonido, Equipos deportivos, Herramientas, Juguetes y más.
¿Qué te podemos ayudar a hacer a continuación?
∇ Ir a la página de inicio para Fundición a presión China
→Piezas de fundición-Descubre lo que hemos hecho.
→ Consejos Ralated Acerca de Servicios de fundición a presión
By Fabricante de fundición a presión Minghe | Categorías: Artículos útiles |Material Tags: Fundición de aluminio, Fundición de zinc, Fundición de magnesio, Fundición de titanio, Fundición de acero inoxidable, Fundición de latón,Fundición de bronce,Casting de video,Historia de la empresa,Fundición a presión de aluminio | Comentarios desactivados