La práctica de producción para reducir el consumo de energía
El consumo de energía es el segundo mayor consumo de energía después del consumo de combustible sólido en el proceso de sinterización, representando alrededor del 13% al 20%. Por lo tanto, la reducción del consumo de energía también es una medida importante para reducir el consumo de energía en el proceso de sinterización.
1. Reducir la tasa de fuga de aire del equipo y reducir el consumo de energía
El consumo de energía del ventilador de extracción principal representa la mayor parte del consumo de energía total de la planta de sinterización. Reducir la tasa de fuga de aire del sistema de ventilación y aumentar el volumen de aire efectivo a través de la capa de material es de gran importancia para ahorrar consumo de energía.
La fuga de aire entre el carro de sinterización y la caja de viento (placa de sellado), el carro y la corredera, y el carro y el carro representan más del 80% de la fuga de aire total de la máquina de sinterización. Por lo tanto, se mejora la forma de sellado entre el carro y la corredera.En particular, la estructura sellada en el extremo de las cajas de aire de la cabeza y la cola puede reducir significativamente las fugas de aire dañinas, aumentar el flujo de aire efectivo a través de la capa de material, aumentar la salida. de sinterización, y ahorra electricidad. Además, la sustitución y el mantenimiento oportunos del carro, la mejora del método de la tela y la reducción de las fugas de aire del borde entre el deflector del carro y la mezcla pueden reducir eficazmente las fugas de aire dañinas. Al fortalecer la lubricación, el mantenimiento y la gestión del equipo, la tasa de fuga de aire de la máquina de sinterización se reduce significativamente, el flujo de aire efectivo a través de la capa de material aumenta considerablemente, se mejora la calidad del mineral sinterizado y se reduce el consumo de energía. reducido.
En la actualidad, la mayor parte del sellado del carro y la guía deslizante adopta un dispositivo de sellado de placa flotante cargado por resorte instalado en la ranura de sellado del carro. Pero la estructura es defectuosa. El dispositivo elástico de sellado de guías deslizantes sirve principalmente para instalar un resorte en espiral y una placa flotante en la ranura de sellado. Problemas con este tipo de dispositivo de sellado:
Una es que el tamaño de la tabla flotante no es fácil de determinar, ya sea grande o pequeño, y no solo el correcto; el segundo es el envejecimiento del muelle helicoidal y pierde su elasticidad; el tercero es la acumulación de polvo en el espacio de la ranura donde se coloca el resorte. Bajo la abrasión del flujo de aire de alta velocidad que arrastraba partículas de polvo, los dos extremos de la ballesta se desgastaron rápidamente y no pudieron usarse durante tres a cinco meses. Además de las deficiencias mencionadas anteriormente, los tres tipos de dispositivos de sellado entre el carro y la guía de deslizamiento mencionados anteriormente tienen un defecto común, es decir, el espacio entre los dos extremos de la placa flotante y la pared lateral de la ranura de sellado es fácil de caer en la escoria y la placa flotante Está atascado de modo que no puede flotar hacia arriba y hacia abajo, lo que provocará una fuga de aire en el espacio entre la tabla flotante y la guía fija.
Por lo tanto, para reducir la tasa de fuga de aire de sinterización, se deben mejorar los dispositivos de sellado existentes que se han adoptado, y el carro debe inspeccionarse regularmente y la placa flotante flotante elástica debe reemplazarse. Para mejorar eficazmente el efecto de sellado, en una palabra, todos los espacios de fuga de aire se pueden sellar completamente para reducir la tasa de fuga de aire de sinterización. De lo contrario, reducir la tasa de fuga de aire de sinterización es una tontería.
2. Mejorar la permeabilidad al aire de la mezcla.
La resistencia de la red de tuberías del ventilador de sinterización se compone de dos partes: la pérdida de carga de la capa de material sinterizado y la pérdida de montaje de la tubería. Mejorar la permeabilidad al aire de la capa de material sinterizado es la clave para reducir la resistencia de la red de tuberías del ventilador y reducir el consumo de energía. La permeabilidad al aire de la capa de material se puede expresar mediante la siguiente fórmula:
- K = Q / A × (h / P) n
- K: transpirabilidad
- Q: volumen de aire que pasa a través de la capa de material m3 / min
- A — área de la capa de material m2
- h — Espesor de la capa de material mm
- P: pérdida de resistencia de la capa de material Pa
- n: índice 0.6
Los estudios han demostrado que el tamaño de partícula de la mezcla sinterizada tiene una relación positiva con la permeabilidad al aire, es decir, la permeabilidad al aire de la capa de material aumenta con el aumento del tamaño de partícula. Por lo tanto, en la producción, al agregar una cantidad adecuada de cal viva, se estabiliza la proporción de mineral que regresa, se aumenta la temperatura del agua caliente en la primera mezcla y se precalienta la segunda mezcla con vapor.
(1) Agregue la cantidad adecuada de cal viva
De acuerdo con la fórmula de reacción CaO + H2O = Ca (OH) 2 + 64883KJ / Kg, se puede calcular aproximadamente que la temperatura del material sinterizado de 100 kg se puede aumentar en 39 ° C. En realidad, la temperatura del material aumenta entre 8 ° C y 10 ° C debido a la pérdida de calor durante el transporte. Teóricamente, la proporción de cal viva al 4% puede cumplir con el requisito de temperatura del punto de rocío. Considerando la pérdida de calor, la proporción de cal viva en producción es del 5%.
(2) Aumente la temperatura del primer agua caliente mezclada.
La temperatura del agua rociada de un mezclador es superior a 60 ℃, lo que puede aumentar la temperatura de la mezcla y promover la digestión de la cal viva.
(3) La segunda mezcla usa vapor para precalentar
El paso de vapor al mezclador secundario también es una medida para aumentar la temperatura del material. La práctica ha demostrado que el uso de vapor puede aumentar la temperatura del material hasta 65 ℃, pero cuando la producción se encuentra durante un período prolongado de parada, se debe confirmar que la válvula de vapor está cerrada para evitar que el vapor entre en el rodillo, provocando una producción innecesaria. accidentes
La temperatura de la mezcla se muestra en la Tabla 1:
Tabla 1 Temperatura de mezcla mensual
Mes | 4 | 5 | 6 | 7 | 8 | 9 |
Temperatura del material ℃ | 55 | 60 | 60 | 62 | 63 | 55 |
(4) Tasa de retorno estable
- ① La cantidad de mineral devuelto afecta el rendimiento de sinterización. Afecta la producción de sinterización, causa una formación irregular del mineral y disminuye la fuerza de la formación del mineral.
- ② El C residual del mineral de retorno y las sustancias alcalinas afectan el equilibrio del C de sinterización y el control del R del mineral.
- ③La mezcla se puede precalentar para devolver el mineral.
- ④La devolución del mineral favorece la granulación de la mezcla y mejora la eficiencia de la sinterización. Demasiado pequeño deteriorará la permeabilidad de la capa de material, y demasiado grande hará que la mezcla se derrita fácilmente, hará que la estructura del mineral sinterizado sea uniforme y la resistencia será peor.
El tamaño de partícula de retorno adecuado es de 0.5 a 5 mm; la inestabilidad del carbón residual hará que el carbón fijo en el sinterizado fluctúe, Afectará el progreso normal del proceso de sinterización; la alta temperatura de retorno favorece el precalentamiento de la mezcla, pero no favorece la formación de bolas de la mezcla. Por lo tanto, se requiere que la proporción de mineral de retorno esté entre 32% y 40% en producción. Como se muestra en la Tabla 2:
Tabla 2 Proporción de rendimiento mensual
Mes | 4 | 5 | 6 | 7 | 8 | 9 |
Proporción | 35 | 33 | 32 | 35 | 36 | 37 |
3. Reducir la resistencia a la sinterización
La temperatura en la zona de alta temperatura de sinterización es alta y la fase líquida producida aumentará la resistencia del flujo de aire. El nivel de temperatura en la zona de alta temperatura está determinado por la temperatura y el grosor de la zona de combustión, que depende no solo del balance de calor de la zona de combustión, sino también de la velocidad de combustión y la tasa de transferencia de calor del carbón sólido. Por lo tanto, las propiedades fisicoquímicas del combustible afectan directamente a la resistencia de la zona de combustión de sinterización. Tiene la siguiente relación:
Cantidad de combustible: aumenta la cantidad de combustible, lo que no solo aumenta la temperatura de la zona de combustión, sino que también aumenta su espesor;
Tamaño de partícula de combustible: aumente el tamaño de partícula de combustible. A medida que disminuye la velocidad de combustión y se prolonga el tiempo de combustión, la temperatura de la zona de combustión disminuye y aumenta el espesor. Velocidad del flujo de aire: la velocidad del flujo de aire tiene un efecto sobre la velocidad de transferencia de calor y la velocidad de combustión, pero el grado de influencia es diferente. Cuando aumenta la velocidad del flujo de aire, la velocidad de transferencia de calor y la velocidad de combustión se desarrollan a diferentes velocidades, y la brecha entre las dos aumenta gradualmente, lo que hace que la transferencia de calor y la combustión se desconecten, reduciendo la temperatura de la capa de combustión y aumentando el espesor. En la producción real, el flujo de aire debe controlarse de modo que la velocidad de combustión y la velocidad de transferencia de calor sean similares para lograr la temperatura de combustión más alta y el ancho de la zona de combustión más estrecha. Para el polvo de coque, se considera que 1 mm ~ 3 mm es el mejor tamaño de partícula, y el tamaño de partícula de polvo de coque de la segunda área de operación de la zona de sinterización de Beiying de Benxi Iron and Steel se controla básicamente al 78% si es inferior a 3 mm. . Como se muestra en la Tabla 3:
Tabla 2 Proporción de rendimiento mensual
Mes | 4 | 5 | 6 | 7 | 8 | 9 |
Granularidad% | 78 | 79 | 78 | 80 | 79 | 80 |
4. Utilice regulación de velocidad de frecuencia variable y compensación de condensador para reducir el consumo de energía
La tecnología de regulación de velocidad de conversión de frecuencia es un método de regulación de velocidad seguro, confiable y razonable desarrollado en los últimos años. Logra el propósito de ajustar la velocidad del motor convirtiendo la corriente alterna con un cierto voltaje y frecuencia utilizada en la producción diaria en una corriente alterna con una frecuencia y voltaje variable a través de un convertidor. Después de que el motor de velocidad variable adopta la regulación de velocidad de conversión de frecuencia, la corriente promedio se reduce y se ahorra energía eléctrica. En la producción real, para perseguir la tasa de operación del equipo, junto con la calidad del equipo, el funcionamiento y otras razones, la potencia del motor a menudo aumenta artificialmente, lo que resulta en el fenómeno de "gran carro tirado por caballos", que aumenta el reactivo potencia del motor y desperdicia energía eléctrica. . En la segunda área de sinterización del área de sinterización Beiying de Benxi Iron and Steel, después de un año de práctica de producción, ha mejorado continuamente su propio nivel operativo y experiencia acumulada. Ha realizado continuos esfuerzos para ahorrar energía y reducir el consumo en sinterización. Durante la producción normal, la potencia media de los dos extractores de aire principales ha cambiado con respecto al original. La calidad y cantidad de sinterización se puede reducir a unos 5500 Kw / h desde unos 6000 Kw / ha unos 5500 Kw / h. Al mismo tiempo, la calidad y cantidad de sinterización satisfacen plenamente los requisitos de producción del alto horno.
Observaciones finales: Sinterizar el ahorro de energía es una tarea difícil, persistente y a largo plazo que debe ser completada por los trabajadores de sinterización. Debe explorarse, resumirse, mejorarse y perfeccionarse constantemente en la producción. Solo bajo la premisa de control de calidad y reducción de costos podemos mantenernos firmes en el débil mercado del acero actual, por lo que la conservación de energía y la reducción de emisiones son la tarea de por vida de los trabajadores de sinterización.
Conserve la fuente y la dirección de este artículo para reimprimir: La práctica de producción para reducir el consumo de energía
Minhe Empresa de fundición a presión se dedican a fabricar y proporcionar piezas de fundición de calidad y alto rendimiento (la gama de piezas de fundición a presión de metal incluye principalmente Fundición a presión de pared delgada,Fundición a presión en cámara caliente,Fundición a presión de cámara fría), Servicio redondo (servicio de fundición a presión,Mecanizado cnc,Fabricación de moldes, Tratamiento de superficie) .Cualquier fundición a presión de aluminio personalizada, fundición a presión de magnesio o Zamak / zinc y otros requisitos de fundición pueden contactarnos.
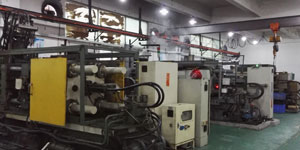
Bajo el control de ISO9001 y TS 16949, todos los procesos se llevan a cabo a través de cientos de máquinas de fundición a presión avanzadas, máquinas de 5 ejes y otras instalaciones, que van desde desintegradores hasta lavadoras Ultra Sonic.Minghe no solo cuenta con equipos avanzados, sino que también cuenta con profesionales equipo de ingenieros, operadores e inspectores experimentados para hacer realidad el diseño del cliente.
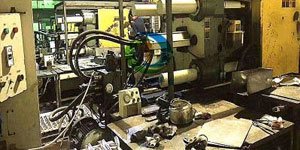
Fabricante por contrato de piezas de fundición a presión. Las capacidades incluyen piezas de fundición a presión de aluminio de cámara fría de 0.15 libras. a 6 libras, configuración de cambio rápido y mecanizado. Los servicios de valor agregado incluyen pulido, vibración, desbarbado, granallado, pintura, enchapado, revestimiento, ensamblaje y herramientas. Los materiales con los que se trabaja incluyen aleaciones como 360, 380, 383 y 413.
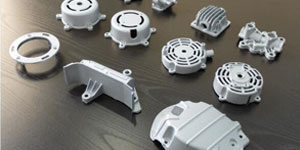
Asistencia en el diseño de fundición a presión de zinc / servicios de ingeniería simultáneos. Fabricante personalizado de piezas fundidas de zinc de precisión. Se pueden fabricar piezas de fundición en miniatura, piezas de fundición a presión de alta presión, piezas de fundición de moldes de deslizamiento múltiple, piezas de fundición de moldes convencionales, piezas de fundición unitaria e independiente y piezas de fundición selladas en cavidades. Las piezas fundidas se pueden fabricar en longitudes y anchos de hasta 24 pulgadas con una tolerancia de +/- 0.0005 pulgadas.
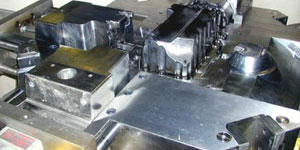
Fabricante certificado por ISO 9001: 2015 de magnesio fundido a presión, las capacidades incluyen fundición a presión de magnesio a alta presión de hasta 200 toneladas de cámara caliente y 3000 toneladas de cámara fría, diseño de herramientas, pulido, moldeado, mecanizado, pintura en polvo y líquida, control de calidad completo con capacidades de CMM , montaje, embalaje y entrega.
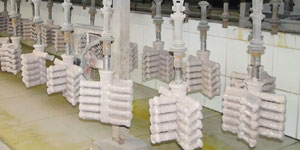
Certificado ITAF16949. El servicio de casting adicional incluye fundición de inversión,moldeo en arena,Fundición por gravedad, Fundición de espuma perdida,Fundición centrífuga,Fundición al vacío,Fundición de molde permanenteLas capacidades incluyen EDI, asistencia de ingeniería, modelado de sólidos y procesamiento secundario.
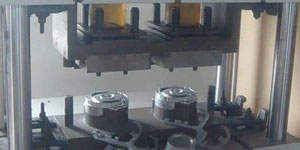
Industrias de fundición Estudios de casos de piezas para: automóviles, bicicletas, aeronaves, instrumentos musicales, embarcaciones, dispositivos ópticos, sensores, modelos, dispositivos electrónicos, carcasas, relojes, maquinaria, motores, muebles, joyas, plantillas, telecomunicaciones, iluminación, dispositivos médicos, dispositivos fotográficos, Robots, Esculturas, Equipos de sonido, Equipos deportivos, Herramientas, Juguetes y más.
¿Qué te podemos ayudar a hacer a continuación?
∇ Ir a la página de inicio para Fundición a presión China
→Piezas de fundición-Descubre lo que hemos hecho.
→ Consejos Ralated Acerca de Servicios de fundición a presión
By Fabricante de fundición a presión Minghe | Categorías: Artículos útiles |Material Tags: Fundición de aluminio, Fundición de zinc, Fundición de magnesio, Fundición de titanio, Fundición de acero inoxidable, Fundición de latón,Fundición de bronce,Casting de video,Historia de la empresa,Fundición a presión de aluminio | Comentarios desactivados