El control del proceso de producción de hierro vermicular
En comparación con el hierro gris, la resistencia a la tracción del hierro vermicular aumenta en al menos un 70%, el módulo de elasticidad aumenta en un 35% y la resistencia a la fatiga casi se duplica. En comparación con la aleación de aluminio, la resistencia y la rigidez del hierro vermicular son dos veces más altas y la resistencia a la fatiga es dos veces más alta. Estas características del hierro vermicular brindan la posibilidad al motor de mejorar la relación potencia / peso y aumentar la presión del cilindro. El aumento de la presión de los cilindros es la clave para el rendimiento óptimo del motor diésel de inyección directa de próxima generación. Para hacer frente a la aplicación generalizada de hierro vermicular, la industria de la fundición se está preparando activamente, invirtiendo fuertemente y reconstruyendo nuevos procesos para hacer que la producción de hierro vermicular sea estable y confiable.
Para los motores de hierro vermicular desde el prototipo hasta la producción en masa, el factor decisivo es el riesgo de calidad. Para el hierro vermicular de alta calidad, la zona estable es muy pequeña, solo en el rango del 0.008% de contenido de magnesio. Una cantidad mínima, como una pérdida del 0.001% de magnesio, producirá grafito en escamas, lo que hará que las propiedades mecánicas caigan entre un 25% y un 40%. Este artículo describe un sistema de control de procesos basado en métodos de análisis térmico. El sistema mide la pérdida de magnesio y ajusta el estado del hierro fundido en línea para evitar la generación de grafito en escamas. Este método de control en línea de medición y ajuste reduce la volatilidad en el proceso de producción de hierro vermicular al punto más bajo y elimina fundamentalmente el riesgo de calidad causado por la producción de hierro vermicular.
La demanda de alta potencia, alto par, bajas emisiones de escape y menor consumo de combustible sigue creciendo. Esto obliga a los diseñadores de motores diésel de alta potencia a aumentar la presión máxima de encendido, lo que aumenta en gran medida la carga térmica y la carga mecánica del motor. La carga térmica y la carga mecánica aumentan al mismo tiempo, por lo que los motores convencionales de fundición y fundición de aleación (CrMo) actualmente utilizados han alcanzado o superado el límite superior de su uso. Los fabricantes de motores necesitan materiales con mayor resistencia y mejor resistencia al calor.
El hierro vermicular se ha convertido rápidamente en el material preferido por las personas. Mejora en gran medida la fiabilidad del bloque de cilindros, la culata y la camisa de cilindros de la nueva generación de motores de camión. Para lograr la mejor combinación de varias propiedades (como propiedades de fundición, propiedades de mecanizado, conductividad térmica y propiedades mecánicas), estas piezas deben fabricarse con una tasa de esferoidización de 0% a 20% (tasa de fluencia de 80% a 100% ) Fabricado en hierro vermicular. Si la tasa de esferoidización supera el 20%, provocará una serie de factores desfavorables. Por ejemplo, la cantidad de contracción es demasiado grande y las piezas con formas complejas, como culatas de cilindros, son particularmente propensas a contraerse. Otro ejemplo es la reducción de la vida útil de la herramienta debido al desgaste excesivo durante el mecanizado. También hay una disminución significativa de la conductividad térmica, lo que provoca estrés térmico, etc. En el otro extremo del hierro vermicular, la aparición de grafito en escamas provocará una disminución lineal de las propiedades mecánicas, lo que hará que el motor no pueda cumplir con los nuevos requisitos. En resumen, para satisfacer las necesidades de la nueva generación de motores de camión, la tasa de esferoidización del hierro vermicular de alta resistencia debe estar entre el 0% y el 20% (es decir, la tasa de fluencia está por encima del 80%, sin escamas).
El uso o no del control del proceso de producción depende de la producción anual del producto, la complejidad del producto y el rango permitido de cambios en la estructura metalográfica. Como se muestra en la Figura 1, las piezas relativamente simples y de bajo volumen, tales como lingoteras, generalmente se pueden producir mediante métodos de fundición convencionales. El control del proceso generalmente no es necesario y no es económicamente rentable. Cuando aumenta la producción anual de componentes, como tubos de escape, manivelas y soportes, debería tener sentido introducir el control del proceso. Aunque este tipo de producto tiene una gran producción anual, el tonelaje anual de fundición no es elevado. Los requisitos de la estructura metalográfica no son muy estrictos, lo que permite que la tasa de esferoidización alcance el 50%. Además, debido a la pequeña cantidad de mecanizado de tales piezas, se puede permitir que el aumento de titanio que se puede agregar en la producción amplíe el rango controlable. Para este tipo de producto, los métodos de fundición convencionales y una formación estricta son generalmente competentes para la producción de hierro vermicular. Pero desde la perspectiva del control de calidad, el control de procesos debería ser más seguro. Del mismo modo, el control de procesos también ofrece una garantía para la producción de grandes bloques de motores marinos y culatas. Aunque el gran tamaño y la baja cantidad de producción son propicias para la fabricación de productos, las pérdidas económicas causadas por los productos que exceden el estándar son suficientes para agregar un conjunto de sistema de control de procesos.
Los productos que más necesitan control de procesos son los bloques de cilindros de los motores de automóviles, las culatas y los discos de freno con gran producción anual, alta complejidad y estrictos requisitos técnicos. El volumen de producción anual y el tonelaje anual de estos productos son muy elevados. Son de tamaño complejo, exigentes con la estructura metalográfica y tienden a producir cavidades de contracción. Estos productos no deben tener ningún riesgo de calidad, de lo contrario la pérdida será muy grave.
Los estrictos requisitos sobre el rendimiento del bloque del motor, la culata y el asiento del cilindro han sentado las bases para las especificaciones de los productos de fabricación. Para obtener el mejor rendimiento integral de moldeabilidad, maquinabilidad y propiedades mecánicas, la tasa de esferoidización debe estar en el rango de 0% a 20% en todas las partes clave del componente. Más importante aún, se debe evitar absolutamente el grafito en escamas para evitar daños a las piezas causados por debilidad local. Para lograr una buena aditividad mecánica, los carburos libres deben reducirse al mínimo. Por lo tanto, nunca se debe agregar titanio. Finalmente, desde el punto de vista de la producción, la fundición necesita un proceso estable y confiable para asegurar la tasa de desperdicio más baja causada por la estructura metalográfica. Los fabricantes de la industria automotriz requieren garantía de calidad y el 100% de las piezas fundidas deben cumplir con los requisitos metalográficos. La producción confiable a gran escala de bloques de cilindros, culatas y asientos de cilindros requiere un análisis preciso y un ajuste en línea del hierro fundido para eliminar las fluctuaciones en el proceso antes del vertido.
Estabilidad del hierro vermicular
La razón por la que el hierro compactado no se usa en grandes cantidades para producir piezas complejas (como bloques de motor) es porque el área estable del hierro compactado es demasiado pequeña para garantizar que no haya riesgos en la producción. En términos generales, esta zona estable solo abarca el área de 0.008% de magnesio, como se muestra en la Figura 2. El tamaño y la posición de la plataforma en la zona estable varían con el producto. De hecho, el rango de magnesio disponible es más pequeño. Porque cada 5 minutos, el magnesio activo quema un 0.001%. El punto de vertido inicial del hierro fundido debe estar lo suficientemente alejado del punto de inflexión afilado del hierro compactado al hierro gris para garantizar que no aparezcan escamas de grafito en la pieza fundida final. Cuando se agrega magnesio al hierro fundido, aparecerán escamas de grafito en aproximadamente 15 minutos.
El punto de partida no debe estar demasiado cerca del lado derecho de la plataforma estable (alto contenido de magnesio), de lo contrario provocará que se forme una gran cantidad de grafito esferoidal en la parte más delgada y en la parte de enfriamiento rápido.
Además de la pequeña área de la plataforma disponible, el área de la plataforma siempre está en movimiento. Si el contenido de oxígeno activo y azufre es alto, consumirán más magnesio activo y toda la plataforma se moverá hacia la derecha (alto contenido de magnesio). Por el contrario, si el contenido de oxígeno activo y azufre es bajo, la plataforma se moverá hacia la izquierda (bajo contenido de magnesio). Los cambios en la composición de las materias primas, pureza, grado de oxidación y humedad, etc., hacen imposible que las personas controlen el hierro vermicular con un rango fijo de composición química.
Aunque la conversión de hierro vermicular a hierro gris solo necesita reducir el magnesio activo en un 0.001%, la combustión del magnesio no hace que toda la pieza se convierta en grafito en escamas. Cuando el magnesio activo no es suficiente, el grafito primero forma escamas y se expande hacia afuera a medida que se solidifica, y el magnesio se hunde y se concentra en el extremo frontal de la interfaz sólido-líquido. Si la cantidad inicial de magnesio activo es apropiada, se formará grafito vermicular en el límite del eutéctico, como se muestra en la Figura 3. El grafito en escamas aparece primero como manchas de grafito en escamas dispersas. A diferencia de todo el grafito en escamas común, estas manchas de grafito en escamas aisladas son difíciles de detectar con ultrasonido. La probabilidad de que sean escaneados por ultrasonido no es alta.
La sensibilidad del magnesio al hierro vermicular se puede mostrar en la Figura 4: En una tonelada de cucharón de metal caliente, solo agregue 10 gramos de magnesio, las manchas de grafito en escamas dispersas en la muestra de prueba Φ25 se pueden transformar completamente en grafito vermicular. La resistencia a la tracción de la barra de prueba con puntos de grafito en escamas es de solo 300 MPa, mientras que la resistencia a la tracción de la misma barra de prueba con fugas completas alcanza los 450 MPa.
El inoculante también es muy sensible a la plataforma estable de hierro vermicular, como se muestra en la Figura 5: agregar 80 gramos de inoculante a una tonelada de hierro fundido aumentará la tasa de esferoidización en la barra de prueba Φ25 del 3% al 21%. La cantidad de inoculación es alta y el núcleo cristalino es elevado, lo que favorece la formación de grafito esférico. Esto eleva la plataforma de hierro vermicular en la dirección de una alta tasa de esferoidización. La baja tasa de inoculación hace que la plataforma se mueva hacia abajo. Numerosos factores, como la temperatura de sobrecalentamiento del hierro fundido, el tiempo de retención, la composición química de las materias primas, el tipo de inoculante y la cantidad de inoculación, afectarán la posición de la plataforma de hierro vermicular.
El requisito más básico de cualquier tecnología de control de procesos es medir y analizar con precisión el estado del hierro fundido. Para el hierro vermicular, un control de producción confiable requiere la medición simultánea del punto crítico de magnesio activo de la transición de fluencia-ceniza, el grado de quemado posterior del magnesio y el grado de inoculación.
La muestra de análisis térmico de 200 gramos se obtiene insertando la sonda Xinte en el hierro fundido después de la esferoidización e inoculación. Durante el proceso de inserción de tres segundos, la pared de la sonda y el hierro fundido alcanzan un estado de equilibrio térmico. A diferencia de la copa de muestra de análisis térmico convencional, este muestreador de pared delgada no solo garantiza el mismo volumen de muestra cada vez, sino que también evita la oxidación en el hierro fundido que se vierte en la copa de muestra. La medición del recalentamiento es más precisa porque no existe un fenómeno como el fenómeno de la condensación violenta en el análisis térmico convencional.
Como se muestra en la Figura 6a, la sonda Xinte está hecha de chapa de acero estirada y prensada. Básicamente es un recipiente esférico. La delgada pared de acero que contiene el hierro fundido tiene una capa de aislamiento similar a un matraz de vacío. El grosor de la capa de aislamiento se engrosa simétricamente de acuerdo con la dirección de la altura para asegurar una disipación de calor uniforme y enfriamiento a los alrededores, y el hierro zz agua en ella está cerca de la solidificación de un cuerpo esférico. Hay dos termopares tipo N en el tubo de protección de la sonda. El termopar se puede extraer después de cada medición y usarse repetidamente más de 100 veces. Uno de los dos termopares está ubicado en la parte inferior del contenedor y el otro está ubicado en el centro térmico del contenedor. Dado que el recipiente es esférico y está suspendido libremente (esto es diferente de la taza de muestra de análisis térmico convencional que descansa sobre un soporte absorbente de calor), el hierro fundido genera un flujo de calor uniforme en el recipiente, como se muestra en la Figura 6b. Este flujo de calor hace que el hierro fundido se intercambie continuamente en el recipiente, formando una partición de flujo en el fondo de la sonda.
Para imitar la pérdida natural de hierro fundido durante el vertido, hay un revestimiento en la pared de la sonda que reacciona con el magnesio activo. El hierro fundido fluye a lo largo de la pared revestida impulsado por el flujo de calor. Después de la reacción, el contenido de magnesio del hierro fundido disminuye y se acumula en el compartimento del fondo del recipiente. Hablando directamente: el termopar en el centro de la sonda mide el hierro fundido sin reaccionar, que es el estado inicial de vertido; el termopar en la parte inferior mide el estado después del final del vertido. La formulación del revestimiento reactivo es muy particular. Debe asegurarse con precisión que el hierro fundido acumulado en el compartimento sea un 0.003% menos activo que el hierro fundido central. Por lo tanto, si el contenido inicial de magnesio está demasiado cerca del punto de inflexión de la ceniza rastrera, el hierro fundido en el compartimiento generará hierro gris, que será medido por el termopar en esta área. De esta manera, al comienzo de la fundición, el taller puede agregar más magnesio para compensar la inevitable pérdida de magnesio por combustión.
Si el termopar en la parte inferior muestra una curva de hierro vermicular, indica que el contenido de magnesio inicial es lo suficientemente alto como para que no haya grafito en escamas después del final de la fundición.
La figura 7 es un diagrama de erosión en sección transversal de la sonda Xinte después de la medición de la muestra. En la figura, puede ver claramente el área de partición, el área principal de la muestra y el tubo de protección del termopar. A medida que el magnesio activo se reduce en un 0.003%, se forma una matriz de ferrita y grafito en forma de D en la zona de separación. El tamaño del área de grafito en escamas en la parte inferior refleja directamente el contenido de magnesio inicial en el área principal de la muestra. El tamaño de esta zona se puede calcular a partir del calor liberado en la parte inferior. El coeficiente de regresión de la varianza entre la liberación de calor y el tamaño de la partición supera el 0.9, lo que demuestra que la relación entre ambos es muy estrecha. El calor liberado se obtiene mediante la integración temporal de la curva de enfriamiento. Este método de medir el estado del hierro fundido en la corriente y al final del vertido al mismo tiempo asegura la precisión del contenido de magnesio antes del vertido.
Dado que el hierro vermicular es muy sensible a los agentes esferoidizantes e inoculantes, es imposible que las fundiciones utilicen los métodos de tratamiento excesivos utilizados en la producción de hierro gris y hierro dúctil. Como se muestra en la Figura 8, debido a su sensibilidad, el hierro vermicular solo es estable dentro de una ventana cuadrada, no solo en el área de la plataforma de magnesio. Un proceso de producción de hierro vermicular confiable debe controlar la esferoidización y la inoculación de principio a fin para garantizar que la estructura metalográfica cumpla con el objetivo.
No importa cuánto esfuerzo se haga, no importa cuán estricto sea el manejo, la fluctuación del hierro fundido es siempre inevitable. Por no hablar de la precisión con la que la gente sabe sobre el tratamiento con hierro fundido, los métodos de tratamiento de un solo paso, como el método sándwich, no pueden garantizar que cada tratamiento caiga dentro de la estrecha ventana de hierro vermicular. Numerosas variables de producción, tales como relación de mezcla, temperatura del horno, tiempo de retención, grado de precalentamiento de la cuchara de hierro fundido, velocidad de roscado, posición de roscado del hierro fundido (medición interior o exterior), peso del hierro fundido, condición de la bolsa de aleación, agente esferoidizante. El contenido real de magnesio de (PeSiMg), la disposición de la aleación de cada capa en el método sándwich y la cobertura de las virutas de hierro, etc., afectarán la absorción de magnesio. Además de estos factores, el contenido de oxígeno activo y azufre activo también cambiará el tamaño y la posición de la ventana de hierro vermicular. Los cambios en el tiempo de residencia del hierro fundido en la cuchara, el tiempo de transporte y el tiempo de vertido cambiarán el tiempo de combustión disponible.
Sin embargo, los factores de fluctuación más impredecibles son los errores del operador o las diferencias entre diferentes operadores debido a diferentes hábitos de trabajo.
En la producción en masa a gran escala, la única forma segura es medir las características de solidificación del hierro fundido después del tratamiento. De esta manera, se han medido, analizado y considerado de manera integral varios factores que afectan el tamaño, la posición y la absorción de la aleación de la ventana de hierro vermicular. Luego se puede agregar la cantidad apropiada de magnesio e inoculante. Cada cucharón de hierro fundido se vierte después de que se ha mejorado a un estado ideal. Este método de control del proceso de medición y ajuste de dos pasos minimiza la variabilidad de la producción y elimina por completo el riesgo de grafito en escamas en la fundición.
Control de proceso de producción de hierro vermicular con cucharón de metal caliente
Como se muestra en la Figura 9, el control del proceso comienza con el análisis térmico del hierro fundido después del tratamiento inicial de esferoidización e inoculación. Según el resultado del análisis, la máquina de alimentación de alambre muestra automáticamente la longitud del alambre que se agregará con magnesio e inoculante, y espera a que el operador lo encienda. Cuando se completa la línea de alimentación, el cucharón se envía a la línea de colada inmediatamente. Todo el proceso de medición y ajuste dura unos tres minutos. Durante este período, el taller puede realizar tratamientos convencionales de precolado, como la eliminación de escorias. Esto asegura la continuidad de la línea de lanzamiento.
Desde un punto de vista operativo, el hierro fundido crudo no contiene magnesio y su capacidad de incubación también es muy limitada. Después de la esferoidización y la inoculación, el magnesio y los inoculantes comen primero el oxígeno activo y el azufre del hierro fundido y luego "saltan" el hierro fundido a una determinada posición en el tablero. En el ejemplo de la Figura 10, el índice de magnesio y el índice de inoculación del hierro fundido son 65 y 45, respectivamente. Debido a que los principales parámetros de cambio de la producción de sombras se muestran en el hierro fundido después de la medición y el tratamiento, los resultados del análisis térmico reflejan directamente el estado actual del hierro fundido. Todo lo que queda es agregar la cantidad apropiada de magnesio e inoculante para elevar el hierro fundido desde su posición actual hasta el punto de partida requerido. En el ejemplo de la Figura 10, primero se agregan siete unidades de cables de magnesio y luego se agregan 23 unidades de cables inoculantes. La relación correspondiente entre la unidad de índice y la longitud del cable se calibra según el producto y el taller, y se compila en el programa. Basado en la experiencia pasada de casi 100,000 piezas de fundición de hierro vermicular, la cantidad promedio de cable de magnesio agregado es de 5 metros por tonelada. Contiene 12 gramos de magnesio por metro, y calculado a una tasa de absorción del 50%, la cantidad de magnesio añadida por tonelada de hierro fundido es de solo 30 gramos. Dado que la cantidad de adición es muy pequeña y los principales cambios ya se han producido en el tratamiento inicial, el ajuste es muy eficaz y fiable. Después del ajuste, no es necesario realizar un análisis térmico.
En el tratamiento inicial, el estado posterior al tratamiento debe ser más bajo que la posición de vertido inicial, de modo que incluso si todos los factores que son beneficiosos para la absorción de magnesio y el inoculante alcanzan el valor óptimo, el hierro fundido solo alcanzará el estado de vertido inicial. . Excepto para no tratar en exceso, el hierro fundido después del tratamiento no se encuentra en el estado de hierro gris y hierro blanco. Para que el proceso de fundición sea más eficiente, el índice de magnesio y el índice de inoculación de cada cuchara de hierro fundido se muestran en el diagrama de bloques del proceso. De acuerdo con la tendencia cambiante del diagrama de bloques, el operador puede ajustar la cantidad de hierro fundido que se agrega a la siguiente cuchara. El valor de carbono equivalente también se muestra en la pantalla. Estos datos se han editado y almacenado en el registro de producción, para que se pueda rastrear y completar, y también cumple con los requisitos de garantía de calidad.
Si bien el análisis térmico y los ajustes posteriores pueden asegurar la producción de hierro vermicular, se recomienda tomar muestras de la copa del bebedero del vaciado final para su análisis. En comparación con la inspección de calidad convencional, este resultado de análisis térmico puede proporcionar un análisis en línea y clasificar las piezas fundidas si es necesario. La simulación de la pérdida de magnesio en la sonda hace que esta técnica de inspección "no destructiva" sea más eficaz que los métodos metalográficos y ultrasónicos. Debido a que este método mide un tamaño de muestra más grande, también detecta cómo se solidificará el hierro fundido en los próximos 10 a 15 minutos.
Para resumir
La elección del sistema de control del proceso depende del producto y del proceso de fundición. Al fundir productos complejos como la tapa del motor y el cilindro de hierro vermicular, el sistema debe controlar simultáneamente el contenido de magnesio y de inoculante para que esté dentro de una ventana muy estrecha desde el principio hasta el final del vertido. La tasa de esferoidización debe estar entre el 0% y el 20% (tasa de avance del 80% al 100%) para garantizar la mejor capacidad de fundición, la aditividad mecánica y otras prestaciones integrales y la mejor función de uso. Las manchas de grafito en escamas deben eliminarse por completo para evitar defectos y debilidades locales.
El punto de partida de cualquier sistema de control de procesos es medir con precisión y eficacia el estado del hierro fundido. La producción confiable de hierro vermicular a gran escala debe tener métodos de control factibles para eliminar los cambios de proceso y los errores de operación humana. La forma más eficaz de eliminar los cambios en el proceso es realizar un análisis térmico del hierro fundido después de la esferoidización y la inoculación. De acuerdo con los resultados del análisis térmico, se agrega una cantidad precisa de magnesio e inoculante antes de verter. Este método de medición y ajuste en línea asegura la estabilidad de la línea de producción de fundición y elimina varios riesgos que conlleva la producción de hierro vermicular a gran escala.
Conserve la fuente y la dirección de este artículo para reimprimir: El control del proceso de producción de hierro vermicular
Minhe Empresa de fundición a presión se dedican a fabricar y proporcionar piezas de fundición de calidad y alto rendimiento (la gama de piezas de fundición a presión de metal incluye principalmente Fundición a presión de pared delgada,Fundición a presión en cámara caliente,Fundición a presión de cámara fría), Servicio redondo (servicio de fundición a presión,Mecanizado cnc,Fabricación de moldes, Tratamiento de superficie) .Cualquier fundición a presión de aluminio personalizada, fundición a presión de magnesio o Zamak / zinc y otros requisitos de fundición pueden contactarnos.
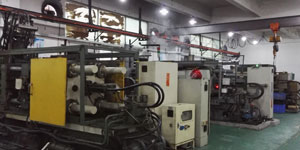
Bajo el control de ISO9001 y TS 16949, todos los procesos se llevan a cabo a través de cientos de máquinas de fundición a presión avanzadas, máquinas de 5 ejes y otras instalaciones, que van desde desintegradores hasta lavadoras Ultra Sonic.Minghe no solo cuenta con equipos avanzados, sino que también cuenta con profesionales equipo de ingenieros, operadores e inspectores experimentados para hacer realidad el diseño del cliente.
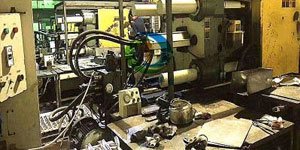
Fabricante por contrato de piezas de fundición a presión. Las capacidades incluyen piezas de fundición a presión de aluminio de cámara fría de 0.15 libras. a 6 libras, configuración de cambio rápido y mecanizado. Los servicios de valor agregado incluyen pulido, vibración, desbarbado, granallado, pintura, enchapado, revestimiento, ensamblaje y herramientas. Los materiales con los que se trabaja incluyen aleaciones como 360, 380, 383 y 413.
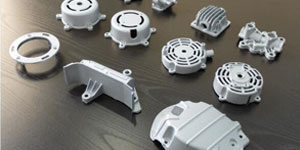
Asistencia en el diseño de fundición a presión de zinc / servicios de ingeniería simultáneos. Fabricante personalizado de piezas fundidas de zinc de precisión. Se pueden fabricar piezas de fundición en miniatura, piezas de fundición a presión de alta presión, piezas de fundición de moldes de deslizamiento múltiple, piezas de fundición de moldes convencionales, piezas de fundición unitaria e independiente y piezas de fundición selladas en cavidades. Las piezas fundidas se pueden fabricar en longitudes y anchos de hasta 24 pulgadas con una tolerancia de +/- 0.0005 pulgadas.
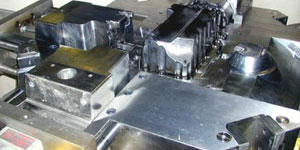
Fabricante certificado por ISO 9001: 2015 de magnesio fundido a presión, las capacidades incluyen fundición a presión de magnesio a alta presión de hasta 200 toneladas de cámara caliente y 3000 toneladas de cámara fría, diseño de herramientas, pulido, moldeado, mecanizado, pintura en polvo y líquida, control de calidad completo con capacidades de CMM , montaje, embalaje y entrega.
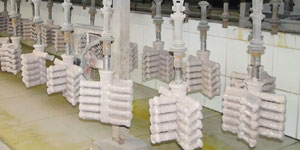
Certificado ITAF16949. El servicio de casting adicional incluye fundición de inversión,moldeo en arena,Fundición por gravedad, Fundición de espuma perdida,Fundición centrífuga,Fundición al vacío,Fundición de molde permanenteLas capacidades incluyen EDI, asistencia de ingeniería, modelado de sólidos y procesamiento secundario.
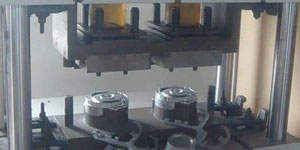
Industrias de fundición Estudios de casos de piezas para: automóviles, bicicletas, aeronaves, instrumentos musicales, embarcaciones, dispositivos ópticos, sensores, modelos, dispositivos electrónicos, carcasas, relojes, maquinaria, motores, muebles, joyas, plantillas, telecomunicaciones, iluminación, dispositivos médicos, dispositivos fotográficos, Robots, Esculturas, Equipos de sonido, Equipos deportivos, Herramientas, Juguetes y más.
¿Qué te podemos ayudar a hacer a continuación?
∇ Ir a la página de inicio para Fundición a presión China
→Piezas de fundición-Descubre lo que hemos hecho.
→ Consejos Ralated Acerca de Servicios de fundición a presión
By Fabricante de fundición a presión Minghe | Categorías: Artículos útiles |Material Tags: Fundición de aluminio, Fundición de zinc, Fundición de magnesio, Fundición de titanio, Fundición de acero inoxidable, Fundición de latón,Fundición de bronce,Casting de video,Historia de la empresa,Fundición a presión de aluminio | Comentarios desactivados