Método de alimentación de alambre Proceso de tratamiento de hierro dúctil
A través de la producción real, se utilizan el método de punzonado y el método de alimentación para producir hierro dúctil, y se analizan las características de los dos procesos. A través de la comparación, el rendimiento integral de las piezas fundidas producidas por el método de alimentación es más estable que el del método de punzonado; y el proceso de alimentación es esferoidizado. Para compartir algunas de las experiencias en él.
1. Visión
Como todos sabemos, el eje es una parte importante del vehículo que soporta carga y está directamente relacionado con la seguridad del vehículo. La carcasa del eje es uno de los componentes clave del eje. El rendimiento del material de la carcasa del eje determina directamente la capacidad de carga del vehículo. En la actualidad, las carcasas de eje en la industria de camiones pesados se dividen generalmente en dos categorías: carcasas de eje estampadas y soldadas y carcasas de eje fundido, y las carcasas de eje fundido se pueden dividir en carcasas de eje de acero fundido y carcasas de eje de hierro fundido.
La carcasa del eje fundido siempre ha ocupado la posición principal de la carcasa del eje del camión pesado debido a su alto peso de carga y bajo costo de producción. Debido al duro entorno de trabajo de la carcasa del eje y al trabajo prolongado bajo carga dinámica, esto requiere altos requisitos para las propiedades del material de la carcasa del eje. Al tiempo que garantiza la resistencia, también necesita obtener una mayor plasticidad y tenacidad para adaptarse a la carcasa del eje. Características del trabajo.
Sabemos que para el hierro fundido nodular, el proceso de esferoidización es un eslabón clave en la producción de hierro fundido nodular, y la calidad del tratamiento esferoidizante afecta directamente la calidad del hierro fundido nodular. Al principio, el proceso de esferoidización que usamos fue el proceso de esferoidización del método rápido. Aunque este método es simple y fácil de operar, tiene muchas deficiencias, tales como: bajo rendimiento de la aleación; gran cantidad de humo y mal ambiente de trabajo; reacción La cantidad de escoria producida en ese momento es grande; el efecto del tratamiento se ve afectado fácilmente por factores externos, lo que conduce a fluctuaciones en la calidad de las piezas moldeadas y, a menudo, a una esferoidización no calificada. Estas fluctuaciones de calidad afectarán el rendimiento de la carcasa del eje e incluso afectarán la seguridad del vehículo.
El proceso de tratamiento de esferoidización del método de alimentación de alambre se aplicó a la producción de hierro fundido. Comenzó en la década de 1980 en el extranjero. Si bien la producción nacional de hierro fundido nodular comenzó a aplicar esta tecnología tardíamente, la tecnología se ha popularizado y utilizado rápidamente en el país, y es útil para mejorar la producción de grafito nodular. El efecto de estabilidad de la calidad del hierro fundido es obvio.
2. Proceso de esferoidización del alambre de alimentación
El principio básico del proceso de esferoidización de alimentación de hilo es envolver una determinada composición de agente esferoidizante en polvo e inoculante a través de la piel de acero y enviarlo al paquete de tratamiento de esferoidización a una cierta velocidad a través del equipo, de modo que la esferoidización en la parte inferior de el paquete detonará. Para lograr el propósito del tratamiento de inoculación de esferoidización.
En la actualidad, el proceso de esferoidización con alimentación de alambre que adoptamos es: ajustar la composición química a los requisitos del proceso, calentar hasta 1510-1520 ℃ y dejar reposar, la temperatura de roscado es 1480 ~ 1500 ℃, la salida de hierro es 2t, y la temperatura del tratamiento de esferoidización es de 1420 ~ 1450 ℃. La temperatura de vertido es de 1370 ~ 1380 ℃. La tasa de inoculación con el flujo es del 0.1%.
La longitud de la línea de esferoidización es de 39-46 m, ajustada según el contenido de azufre del hierro fundido original. Cuanto mayor sea el contenido de azufre, más tiempo será necesario agregar la línea de esferoidización y viceversa. La longitud de la línea de inoculación es de 32 m.
3. El proceso de esferoidización del alambre de alimentación mejora la calidad de las piezas fundidas.
Después de más de un año de producción, la calidad de nuestras carcasas de eje ha mejorado significativamente en comparación con antes. Especialmente la estabilidad de la composición, la metalografía y las propiedades mecánicas se han mejorado enormemente.
Comparación de estructura metalográfica Seleccione la misma posición de la fundición a pulir y observe la estructura metalográfica. La imagen metalográfica tomada se muestra en la Figura 2. En comparación con el método de punzonado, las bolas de grafito de la pieza fundida producidas por el método de alimentación son más y más delgadas, y la redondez es mejor.
4. Ventajas del proceso de esferoidización del hilo de alimentación
De acuerdo con nuestra comparación de producción real, el proceso de esferoidización con alimentación de hilo tiene muchas ventajas sobre el proceso de esferoidización del método de punzonado.
- Mejora del entorno de producción in situ. Cuando el agente esferoidizante reacciona con el hierro fundido, se genera una gran cantidad de humo y una luz intensa, lo que empeora el entorno de trabajo en el lugar; cuando se utiliza el método de alimentación de alambre para la esferoidización, la estación de procesamiento Hay una cubierta para cubrir la bolsa de esferoidización, y la cubierta está conectada al sistema de eliminación de polvo de la estación de procesamiento, de modo que el sistema de eliminación de polvo procesa el humo. de ser liberado directamente en el taller.
- Se reduce la cantidad de aleación añadida y se reduce el coste de producción. Después del cálculo, el procesamiento de 1t de método de alimentación de hierro fundido puede ahorrar alrededor de 78 yuanes en costo de materia prima que el método de impulso. Según la capacidad de producción anual de 10,000 toneladas de carcasa de eje de hierro dúctil de nuestra fábrica, el ahorro anual es de 780,000 yuanes y los beneficios son considerables.
- Consiga la automatización del trabajo y reduzca la intensidad laboral de los trabajadores. Cuando se lleva a cabo el proceso de esferoidización, los preparativos preliminares de los trabajadores son engorrosos, incluido el pesaje del esferoidizante y el inoculante, la adición del esferoidizante y el inoculante a la bolsa, y se requieren operaciones de apisonamiento y recubrimiento; la cantidad adicional de las líneas de esferoidización e inoculación del método de alimentación de hilo se agrega automáticamente a través del gabinete de control, lo que reduce mucho trabajo.
- La calidad de la esferoidización es estable y el efecto de esferoidización es mejor. Según las estadísticas, desde el uso del proceso de esferoidización de alimentación de hilo en 2013, la tasa de aprobación de la esferoidización es superior al 99.5%, mientras que la tasa de aprobación del proceso de esferoidización es solo del 95%.
5. Cómo elegir correctamente los parámetros del proceso de alimentación de la esferoidización del hilo
En la producción real, cómo seleccionar correctamente los parámetros del proceso de alimentación de alambre requiere una cierta cantidad de pruebas para verificar. Hemos sufrido muchos ajustes de proceso desde el inicio de la organización de la prueba hasta la producción en masa formal. A continuación, compartiremos nuestra experiencia con colegas.
Para seleccionar correctamente los parámetros del proceso de alimentación de la esferoidización del hilo, debe prestar atención a los siguientes aspectos:
- (1) La elección del alambre con núcleo Alguna experiencia extranjera no recomienda el uso de alambre con núcleo de alto Mg. El contenido de Mg es demasiado alto, la reacción de esferoidización es intensa, el Mg se quema mucho y la cantidad de escoria es grande. En general, se recomienda seleccionar un contenido de Mg de aproximadamente el 30% y utilizar hilo de inoculación que contenga Ba, que puede prevenir eficazmente la disminución de la inoculación. Los principales parámetros del alambre con núcleo utilizado por nuestra empresa son: el grosor de la vaina de acero exterior es de 0.4 mm y el diámetro del alambre con núcleo es de 13 mm. Antes de usarlo, verifique que el aspecto del alambre tubular sea redondo y libre de grietas, fugas de polvo, etc. En la producción real, es necesario ajustar de acuerdo con la temperatura de tratamiento y la altura del hierro fundido. Generalmente, cuanto mayor es la temperatura de tratamiento, mayor es la altura del hierro fundido y más rápida es la velocidad de alimentación del alambre. Además. Algunos materiales también han introducido un método conveniente y factible para medir la velocidad óptima de alimentación del alambre: primero mida la altura del hierro fundido en la bolsa de procesamiento y luego alimente manualmente la máquina de alambre de modo que el alambre del núcleo toque la superficie del líquido, luego limpiar el mostrador, la máquina de alimentación de alambre manual realiza la alimentación de alambre. Cuando escuche el sonido de respuesta de "boom", verifique la longitud de alimentación inmediatamente. Si esta longitud es básicamente igual a la altura del hierro fundido, la velocidad debería ser adecuada. Después de la verificación, seleccionamos la velocidad de alimentación de 30 m / min.
- Selección de la cantidad de alimentación de hilo La cantidad de alimentación de hilo adecuada es alimentar el hilo con menos núcleo bajo la premisa de garantizar el efecto de esferoidización. La cantidad de alimentación de alambre debe determinarse de acuerdo con el volumen de procesamiento del hierro fundido, la temperatura de procesamiento y el contenido de azufre del hierro fundido. De acuerdo con nuestro contenido original de azufre de hierro fundido y los requisitos del proceso del producto, combinados con la verificación experimental, bajo la condición de garantizar el contenido de magnesio residual, la longitud de la línea de esferoidización es de 39-46 my la longitud de la línea de inoculación es de 32 m.
- La elección de la temperatura de procesamiento La temperatura de procesamiento debe reducirse tanto como sea posible bajo la premisa de garantizar la temperatura de vertido. Cuanto menor sea la temperatura de procesamiento, mayor será la tasa de absorción de magnesio y menor será el consumo de alambre con núcleo. Según las pruebas de producción reales, el tiempo desde el inicio del tratamiento de esferoidización hasta el inicio del vertido es de 4 a 5 minutos, durante los cuales la caída de temperatura es de 40 a 50 ° C y el tiempo de reacción de esferoidización es de 80 a 90 segundos. Dado que el proceso de esferoidización necesita ser invertido, establecemos la temperatura de procesamiento en 1410 ~ 1450 ℃, el límite superior se toma cuando la temperatura ambiente es menor que 5 ℃, y el límite inferior cuando la temperatura ambiente es superior a 25 ℃.
- Selección del contenido de magnesio residual en hierro fundido después del tratamiento. El contenido de magnesio residual debe reservarse para una cierta cantidad de contenido de magnesio de acuerdo con las características de la pieza fundida en sí. Al principio, controlamos el contenido de magnesio residual de 0.03% a 0.06%, pero después de la verificación de la producción real, es más apropiado controlar el contenido de magnesio residual de 0.05% a 0.06%, porque encontramos que cuando el magnesio residual es menor que 0.04%, su grafito La redondez de la bola es un poco peor. Cuando es superior al 0.07%, es propenso a aparecer cementita y la tendencia a la contracción del hierro fundido aumenta.
- Solución del problema del atasco del alambre durante el uso El fenómeno del atasco del alambre ocurrirá durante el proceso de transporte del alambre con núcleo, lo que hará que se deseche todo el paquete de hierro fundido. Para ello, hemos tomado las siguientes medidas: una es instalar un anillo de acero sobre el carrete de alambre con núcleo, como se muestra en la Figura 5, que puede reducir la flexión del alambre y hacer que entre suavemente en el mecanismo de guía; el segundo es conectar las dos bobinas Al soldar, después de soldar, pula las protuberancias más grandes para evitar que el alambre se atasque durante el proceso de transporte; En tercer lugar, evite las curvas de diámetro inferior a 1 m en la tubería de transporte o en la ruta del alambre con núcleo para evitar que el alambre con núcleo sea transportado. Se produjeron fugas de polvo o atascos durante el proceso.
Conclusión 6
- El proceso de esferoidización del método de alambre de alimentación tiene una baja cantidad de adición de aleación, una alta tasa de absorción de Mg y puede reducir eficazmente el humo y la fuerte contaminación lumínica en el taller, creando buenos beneficios económicos y ambientales para las empresas de fundición.
- El proceso de esferoidización del método de alimentación de hilo puede reducir efectivamente la tasa de falla de la esferoidización, mejorar la calidad del hierro fundido nodular, mejorar sus propiedades mecánicas integrales y mejorar la competitividad de la empresa en el mercado.
- Cada fundición debe seleccionar los parámetros de proceso apropiados para la esferoidización de alambre de acuerdo con sus propias condiciones de producción y requisitos del proceso del producto, combinados con la experiencia de producción de sus pares.
El proceso de esferoidización de la línea de alimentación puede mejorar significativamente la estabilidad de la calidad del hierro fundido nodular, reducir los costos de producción, mejorar el entorno de producción y reducir la intensidad laboral de los trabajadores. Esta es la tendencia de desarrollo reciente del proceso de esferoidización.
Conserve la fuente y la dirección de este artículo para reimprimir: FProceso de tratamiento de hierro dúctil con método de alambre de alimentación
Minhe Empresa de fundición a presión se dedican a fabricar y proporcionar piezas de fundición de calidad y alto rendimiento (la gama de piezas de fundición a presión de metal incluye principalmente Fundición a presión de pared delgada,Fundición a presión en cámara caliente,Fundición a presión de cámara fría), Servicio redondo (servicio de fundición a presión,Mecanizado cnc,Fabricación de moldes, Tratamiento de superficie) .Cualquier fundición a presión de aluminio personalizada, fundición a presión de magnesio o Zamak / zinc y otros requisitos de fundición pueden contactarnos.
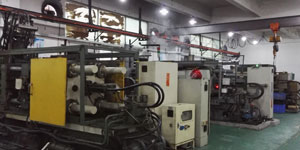
Bajo el control de ISO9001 y TS 16949, todos los procesos se llevan a cabo a través de cientos de máquinas de fundición a presión avanzadas, máquinas de 5 ejes y otras instalaciones, que van desde desintegradores hasta lavadoras Ultra Sonic.Minghe no solo cuenta con equipos avanzados, sino que también cuenta con profesionales equipo de ingenieros, operadores e inspectores experimentados para hacer realidad el diseño del cliente.
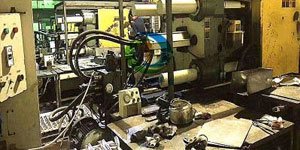
Fabricante por contrato de piezas de fundición a presión. Las capacidades incluyen piezas de fundición a presión de aluminio de cámara fría de 0.15 libras. a 6 libras, configuración de cambio rápido y mecanizado. Los servicios de valor agregado incluyen pulido, vibración, desbarbado, granallado, pintura, enchapado, revestimiento, ensamblaje y herramientas. Los materiales con los que se trabaja incluyen aleaciones como 360, 380, 383 y 413.
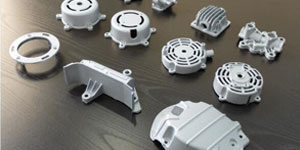
Asistencia en el diseño de fundición a presión de zinc / servicios de ingeniería simultáneos. Fabricante personalizado de piezas fundidas de zinc de precisión. Se pueden fabricar piezas de fundición en miniatura, piezas de fundición a presión de alta presión, piezas de fundición de moldes de deslizamiento múltiple, piezas de fundición de moldes convencionales, piezas de fundición unitaria e independiente y piezas de fundición selladas en cavidades. Las piezas fundidas se pueden fabricar en longitudes y anchos de hasta 24 pulgadas con una tolerancia de +/- 0.0005 pulgadas.
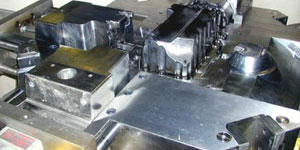
Fabricante certificado por ISO 9001: 2015 de magnesio fundido a presión, las capacidades incluyen fundición a presión de magnesio a alta presión de hasta 200 toneladas de cámara caliente y 3000 toneladas de cámara fría, diseño de herramientas, pulido, moldeado, mecanizado, pintura en polvo y líquida, control de calidad completo con capacidades de CMM , montaje, embalaje y entrega.
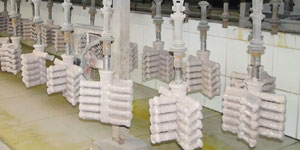
Certificado ITAF16949. El servicio de casting adicional incluye fundición de inversión,moldeo en arena,Fundición por gravedad, Fundición de espuma perdida,Fundición centrífuga,Fundición al vacío,Fundición de molde permanenteLas capacidades incluyen EDI, asistencia de ingeniería, modelado de sólidos y procesamiento secundario.
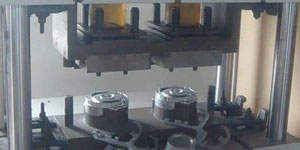
Industrias de fundición Estudios de casos de piezas para: automóviles, bicicletas, aeronaves, instrumentos musicales, embarcaciones, dispositivos ópticos, sensores, modelos, dispositivos electrónicos, carcasas, relojes, maquinaria, motores, muebles, joyas, plantillas, telecomunicaciones, iluminación, dispositivos médicos, dispositivos fotográficos, Robots, Esculturas, Equipos de sonido, Equipos deportivos, Herramientas, Juguetes y más.
¿Qué te podemos ayudar a hacer a continuación?
∇ Ir a la página de inicio para Fundición a presión China
→Piezas de fundición-Descubre lo que hemos hecho.
→ Consejos Ralated Acerca de Servicios de fundición a presión
By Fabricante de fundición a presión Minghe | Categorías: Artículos útiles |Material Tags: Fundición de aluminio, Fundición de zinc, Fundición de magnesio, Fundición de titanio, Fundición de acero inoxidable, Fundición de latón,Fundición de bronce,Casting de video,Historia de la empresa,Fundición a presión de aluminio | Comentarios desactivados