Método de tratamiento térmico de calentamiento por inducción de frecuencia media para tubería de acero, tubería de pozo de petróleo y tubería de perforación
La presente invención es un método de tratamiento térmico de calentamiento por inducción de frecuencia intermedia para tuberías de acero, tuberías de pozos de petróleo y tuberías de perforación. El método se divide en: la pieza de trabajo se coloca en la plataforma de almacenamiento; la pieza de trabajo se alinea y posiciona automáticamente: la pieza de trabajo ingresa a la mesa del rodillo calefactor: enfriamiento por inducción de calentamiento: circuito cerrado sistema de control de temperatura: continuo con la línea La pulverización hace que la pieza de trabajo se enfríe rápida y uniformemente y completamente: el agua residual en la pieza de trabajo se escapa de el tubo en la mesa de drenaje: templado calentamiento por inducción: medición de temperatura por infrarrojos sistema de control de circuito cerrado: elimina las incrustaciones de óxido en la superficie de la pieza de trabajo; lecho de enfriamiento: ventajas: calentamiento por inducción de frecuencia media Como fuente de calor para el tratamiento térmico, no contamina el medio ambiente, es seguro, tiene menos escala y es de bajo costo. La mesa de rodillos calefactores asegura que la pieza de trabajo se caliente uniformemente durante el proceso de calentamiento.
Una vez que la pieza de trabajo pasa por la mesa de rodillos, no necesita una máquina enderezadora para enderezarla, lo que reduce el costo. El dispositivo de enfriamiento por aspersión hace que la pieza de trabajo se enfríe rápida y uniformemente y por completo en el rociado continuo en la línea, y el dispositivo de descalcificación hace que la superficie de la pieza de trabajo terminada brille hasta su verdadero color. La mesa de drenaje produce agua y vapor sin templar dentro del serpentín de calentamiento por inducción, y el serpentín de calentamiento por inducción tiene una larga vida útil.
El método de tratamiento térmico de calentamiento por inducción de frecuencia media para tuberías de acero, tuberías de pozos de petróleo y tuberías de perforación se caracteriza porque los pasos del proceso del método se dividen en:
- La plataforma de almacenamiento en la pieza de trabajo: los tubos de acero de la pieza de trabajo o los tubos de los pozos de petróleo o los tubos de perforación están ordenados en la plataforma de almacenamiento; la plataforma de almacenamiento está inclinada de 2 a 5 grados y la grúa eleva la pieza de trabajo a la plataforma de almacenamiento, automáticamente en orden. Disposición ordenada: la plataforma de almacenamiento de material tiene una estructura de rueda excéntrica. Ajuste la rueda excéntrica en diferentes ángulos para φ60 ~ φ139.7, de modo que el dispositivo de giro solo pueda girar un material a la vez;
- La pieza de trabajo se alinea y posiciona automáticamente: la tubería de acero de la pieza de trabajo o la tubería de pozo de petróleo o la tubería de perforación se envía desde la plataforma de almacenamiento a la primera estación, la mesa de rodillos de alineación y posicionamiento, que consta de cuatro rodillos y está equipada con un interruptor de recepción de material , En el que los rodillos en ambos extremos son impulsados por el motor para impulsar el reductor para alinear la pieza de trabajo;
- La pieza de trabajo ingresa a la mesa del rodillo calefactor: la tubería de acero de la pieza de trabajo o la tubería del pozo de petróleo o la tubería de perforación ingresa a la mesa del rodillo calefactor para un calentamiento uniforme. Los rodillos en forma de V, los motores de control de velocidad de frecuencia variable, los reductores y los rodillos en forma de V se instalan en la mesa del rodillo calefactor de forma oblicua. La velocidad de rotación se ajusta mediante conversión de frecuencia. El alimentador paso a paso es operado por el sensor para levantar suavemente la pieza de trabajo en el marco de alineación y hacerla rodar hacia el alimentador de conversión de frecuencia instalado con una inclinación de 8-20 °. El alimentador de conversión de frecuencia gira a la velocidad establecida. Alimentación frontal, el alimentador de frecuencia variable es un accionamiento de un solo rodillo, con velocidad y altura ajustables. La tubería de acero de la pieza de trabajo o la tubería de pozo de petróleo o la tubería de perforación se coloca en el rodillo en forma de V y gira en la bobina de calentamiento por inducción. Es adecuado para la tubería de acero de la pieza de trabajo o la tubería de pozo de petróleo o la tubería de perforación. Caliente uniformemente;
- Calentamiento por inducción de enfriamiento: la tubería de acero de la pieza de trabajo o el tubo de pozo de petróleo o el tubo de perforación ingresan a la zona de calentamiento por inducción de frecuencia intermedia de enfriamiento a través de la mesa del rodillo de calentamiento. Esta zona de calentamiento se compone de dos juegos de fuentes de alimentación de frecuencia intermedia con diferentes potencias y múltiples juegos de bobinas de inducción de calentamiento para formar una zona de calentamiento por inducción de enfriamiento. La temperatura de calentamiento es de 850 ℃ -1000 ℃ para asegurar la temperatura uniforme de la pieza de trabajo;
- Control de temperatura de bucle cerrado: instale un termómetro infrarrojo de dos colores a la salida de la bobina de calentamiento por inducción para controlar la temperatura de la pieza de trabajo y enviar la señal a la fuente de alimentación de frecuencia intermedia para ajustar automáticamente la potencia de salida de la potencia de frecuencia intermedia suministro para formar un sistema de control de circuito cerrado para controlar la temperatura del proceso del producto Dentro del rango de error permitido;
- La pulverización continua a lo largo de la línea hace que la pieza de trabajo se enfríe rápida y uniformemente y por completo: la tubería de acero de la pieza de trabajo calentada o la tubería del pozo de petróleo o la tubería de perforación ingresan a la zona de enfriamiento por aspersión, y el dispositivo de enfriamiento por aspersión se usa para rociar continuamente agua sobre la superficie del calentador. tubo de acero. La pared de la tubería se apaga y el efecto de disipación de calor rápida y uniforme. Pulverización fuerte durante 5-30 segundos. Se seleccionan dos juegos de bombas de agua de alto flujo y alta presión. La presión es de 125 metros. La velocidad de circulación del agua es de 1,000 m ↑ [3] / h. La potencia total es superior a 500 kW. , Para garantizar que se destruya la película de vapor generada en la superficie de la pieza de trabajo;
- Mesa de drenaje en la pieza de trabajo: retire el agua que queda en la tubería después de templar la tubería de acero de la pieza de trabajo o la tubería del pozo de petróleo o la tubería de perforación y llévela a la bobina de templado. Utilice la mesa de drenaje para inclinarla en dos direcciones para lograr el propósito de eliminar el agua. La tubería de acero de la pieza de trabajo o la tubería de pozo de petróleo o la tubería de perforación se desplaza automáticamente, y la otra dirección se inclina de 2 a 5 ° en la dirección axial de la tubería de acero de la pieza de trabajo o la tubería de pozo de petróleo o la tubería de perforación, de modo que la pieza de acero tubería o tubería de pozo de petróleo o tubería de perforación se mueve automáticamente sobre la mesa de drenaje. Cuando esté en posición, haga salir el agua de la tubería de acero de la pieza de trabajo o la tubería del pozo de petróleo o la tubería de perforación y, después de unos minutos, el alimentador neumático la elevará a la mesa de rodillos de la línea de templado;
Horno de tratamiento térmico de tubos de acero de petróleo
Con la creciente dificultad de la extracción de petróleo y la profundización de las profundidades de los pozos, los requisitos para el grado de resistencia de las tuberías de los pozos de petróleo son cada vez más altos. La tubería y la carcasa de grado de acero J55 gradualmente no han podido cumplir con los requisitos de uso, y el grado de acero N80 se ha convertido en un grado de acero convencional. Q125 y otros grados de acero se utilizan cada vez más, y el mercado de tubos proporciona principalmente tubos de acero de grado de acero J55, y es muy difícil comprar tubos de acero de grado N80, P110 y Q125. Esto ha traído grandes dificultades a los fabricantes de tubos de acero al petróleo para fabricar tubos y revestimientos de acero de alta calidad. La construcción de una línea de producción de tratamiento térmico de tuberías de acero al petróleo puede aumentar las tuberías J55 de bajo grado fáciles de comprar a grados de acero N80, P110 y Q125 mediante tratamiento térmico, lo que resuelve la dificultad de comprar tuberías de acero de alto contenido requisitos de los fabricantes de aceite de tubos de acero para la fabricación de acero de alta calidad. La demanda de tuberías y revestimientos de grado cumple con la dificultad cada vez mayor de la exploración petrolera.
Los tubos de acero se cuelgan y se colocan en la plataforma de carga inclinada en la superficie superior del horno de enfriamiento. La mesa de rodillos de alimentación fuera del horno está equipada con un tope y un dispositivo de tracción de material. El dispositivo de tracción de material tira de un tubo de acero desde la plataforma de carga hasta la mesa del rodillo de alimentación fuera del horno de enfriamiento. En el momento del ciclo de alimentación, se abre la puerta del horno de alimentación del horno de enfriamiento, y la mesa de rodillos de alimentación fuera del horno de enfriamiento y la mesa de rodillos en voladizo dentro del horno giran rápidamente al mismo tiempo para enviar la tubería de acero al enfriamiento. horno. El posicionamiento de la tubería de acero al horno de enfriamiento es controlado por el dispositivo de posicionamiento de la tubería de acero y el PLC. El dispositivo de posicionamiento de la tubería de acero generalmente se compone de dos interruptores fotoeléctricos, que y el PLC completan la medición de la longitud y la velocidad de la tubería de acero y el posicionamiento en el horno.
La tubería de acero ingresa al horno en su lugar, y la mesa de rodillos de alimentación dentro y fuera del horno deja de girar. En este momento, la viga móvil del mecanismo de desplazamiento en el horno se eleva, elevando la tubería de acero en la mesa de rodillos en voladizo en el horno 180 mm, y la viga móvil avanza 140 mm horizontalmente y luego desciende 180 mm. Coloque la tubería de acero. en la superficie inclinada del zócalo del diente de la viga fija en el horno y gire un cierto ángulo para caer en el hueco del diente. Luego, la viga móvil se devuelve a la posición original en 140 mm horizontalmente para completar una acción de paso hacia adelante. De esta manera, cada dos latidos de alimentación, la viga caminante completa un movimiento hacia adelante. La tubería de acero se mueve hacia adelante en la viga fija en un paso de 180 mm y se gira en un cierto ángulo. La tubería de acero se calienta y se mantiene en el horno de enfriamiento según el requisito de temperatura de enfriamiento del proceso. La viga móvil sostiene la tubería de acero a la mesa de rodillos en voladizo de salida en el horno de enfriamiento, la puerta del horno de descarga se abre y el rodillo en voladizo de salida en el horno de enfriamiento y la mesa de rodillos de salida fuera del horno de enfriamiento giran rápidamente al mismo tiempo ( Regulación de velocidad de conversión de frecuencia máxima 2 m / S). La tubería de acero se transporta a la mesa de rodillos fuera del horno, y luego a la mesa de rodillos de recepción de la máquina de enfriamiento a través del dispositivo de descalcificación de agua a alta presión. La mesa de rodillos de recepción de la máquina de enfriamiento está equipada con dos interruptores fotoeléctricos. La cabeza del tubo de acero bloquea el primer interruptor fotoeléctrico y la mesa de rodillos se ralentiza. Bloquee la segunda mesa de rodillos del interruptor fotoeléctrico para que se detenga y la tubería de acero se apoyará ligeramente contra el deflector fijo. En este momento, el mecanismo de carga del horno de enfriamiento (un juego de palancas Sweeten) coloca el soporte de la tubería de acero sobre un juego de ruedas giratorias de soporte de enfriamiento. Correspondientes a un conjunto de ruedas de prensado son accionadas por cilindros hidráulicos para prensar los tubos de acero. La tubería de acero es impulsada por la rueda de soporte giratoria para girar a una velocidad más alta. En este momento, el cilindro de aceite quita el deflector de agua de pulverización exterior, se rocía el agua de pulverización exterior, se invierte la válvula de tres vías de pulverización interior y se pulveriza el agua de pulverización interior desde el orificio interior de un extremo del tubo de acero. Se apaga mediante ducha externa y rotación interna del rociador. El tiempo de enfriamiento se puede establecer arbitrariamente dentro de 6-30 segundos según el material y el espesor de la pared de la tubería de acero. Después del enfriamiento, el deflector de agua bloqueará el agua exterior del área de enfriamiento y caerá al pozo de abajo, y la válvula de tres vías de rociado interno cambiará al agua de rociado interno para fluir hacia el pozo a través de la derivación. La rueda de presión se aleja y el mecanismo de tracción del material saca la tubería de acero y la desliza sobre el dispositivo aire-agua, y se levanta un extremo del dispositivo aire-agua. Al mismo tiempo, el aire comprimido expulsa agua por la boquilla. Una vez que el agua está vacía, el dispositivo de agua vacío se deja caer y se reinicia, y el dispositivo de parada de alimentación extrae la tubería de acero y la envía a la mesa de rodillos de alimentación fuera del horno de templado. Cuando se alcanza el ritmo de alimentación, se abre la puerta del horno de templado y la mesa de rodillos envía la tubería de acero al horno de templado. El modo de transmisión es el mismo que el del horno de enfriamiento. La tubería de acero se calienta paso a paso en el horno de templado a la temperatura de proceso. La puerta del horno de descarga del horno de templado se abre y la tubería de acero se transporta al exterior del horno mediante la mesa de rodillos de descarga del horno de templado y se conecta a la mesa de rodillos de alimentación antes que la máquina enderezadora a través de la mesa de rodillos de conexión. . La tubería de acero se enfría a 450- mediante un pequeño lecho de enfriamiento frente a la máquina enderezadora. Aproximadamente a 500 grados, la tubería de acero se coloca en la mesa de rodillos de avance de la máquina enderezadora y se envía a la máquina enderezadora para enderezarla.
Este tipo de horno puede realizar el tratamiento térmico de tubos de acero.
Diseño de línea de producción de tratamiento térmico en laminadora de tubos de acero continuo
Esta línea de tratamiento térmico se utiliza principalmente para el tratamiento térmico de aceite y tripa, de acuerdo con la norma API 5CT — 2001. Producir tuberías y revestimientos de alto valor agregado para mejorar los beneficios económicos. Después del tratamiento térmico, la tubería y la carcasa tienen mayor resistencia, tenacidad y resistencia a la corrosión, alcanzan el estándar internacional y se encuentran en una posición de liderazgo en China.
El diseño se lleva a cabo de acuerdo con el siguiente flujo de proceso: las tuberías de acero a ser tratadas térmicamente desde el almacén intermedio se colocan en la plataforma de carga con una grúa, y luego ingresan al horno de enfriamiento, luego de ser descargadas según sea necesario, la alta presión Se lleva a cabo la desfosforización del agua y el dispositivo de enfriamiento del agua es transportado por la mesa de rodillos giratorios. Utilice varios juegos de rodillos de compactación para comprimir la tubería de acero y hacerla girar. La pared exterior de la tubería se enfría inmediatamente debajo del agua a temperatura ambiente por encima, y la boquilla de la tubería se alinea con la boquilla rociadora interior para enfriar la pared interior de la tubería hasta que la temperatura de la tubería de acero alcanza la transformación de estructura requerida.
En este momento, se levanta el transportador y la palanca de cambios transporta la tubería de acero al área de drenaje y luego al horno de templado. Después de que la tubería de acero sale del horno de templado, ingresa al lecho de enfriamiento a través de la máquina calibradora y la máquina enderezadora en caliente, y luego realiza una inspección no destructiva después del enfriamiento. , E ingrese al almacén intermedio después de ser calificado. Las tecnologías e innovaciones clave de esta línea de producción son:
- Utilice los principios de ingeniería del sistema y los requisitos del proceso para optimizar el flujo del proceso, de modo que toda la línea tenga cuatro funciones de tratamiento térmico, considerando al mismo tiempo el flujo primario y secundario, el flujo suave, la alta eficiencia y el bajo consumo.
- El uso de la tecnología de ducha externa y de rociado interno, junto con el software del sistema experto del proceso de enfriamiento con agua de la tubería de acero, asegura parámetros de proceso razonables y confiables al procesar tuberías de acero sin costura de varios grados de acero, lo que garantiza la calidad de los productos tratados térmicamente.
- Control completamente automático, administración de información computarizada y monitoreo de la calidad de todo el proceso para mejorar la productividad laboral y el nivel de administración.
- El cambio de enfriamiento con aceite por enfriamiento con agua reduce en gran medida la contaminación ambiental, ahorra aceite y mejora la seguridad de la producción.
- Optimice la cartera de inversiones y la selección de equipos, y ahorre más de 100 millones de yuanes en inversiones en construcción en comparación con toda la línea de importaciones de equipos.
Conserve la fuente y la dirección de este artículo para reimprimir: Método de tratamiento térmico de calentamiento por inducción de frecuencia media para tubería de acero, tubería de pozo de petróleo y tubería de perforación
Minhe Empresa de fundición a presión se dedican a fabricar y proporcionar piezas de fundición de calidad y alto rendimiento (la gama de piezas de fundición a presión de metal incluye principalmente Fundición a presión de pared delgada,Fundición a presión en cámara caliente,Fundición a presión de cámara fría), Servicio redondo (servicio de fundición a presión,Mecanizado cnc,Fabricación de moldes, Tratamiento de superficie) .Cualquier fundición a presión de aluminio personalizada, fundición a presión de magnesio o Zamak / zinc y otros requisitos de fundición pueden contactarnos.
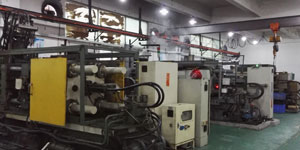
Bajo el control de ISO9001 y TS 16949, todos los procesos se llevan a cabo a través de cientos de máquinas de fundición a presión avanzadas, máquinas de 5 ejes y otras instalaciones, que van desde desintegradores hasta lavadoras Ultra Sonic.Minghe no solo cuenta con equipos avanzados, sino que también cuenta con profesionales equipo de ingenieros, operadores e inspectores experimentados para hacer realidad el diseño del cliente.
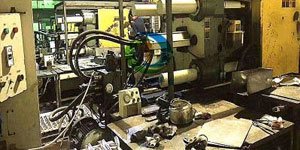
Fabricante por contrato de piezas de fundición a presión. Las capacidades incluyen piezas de fundición a presión de aluminio de cámara fría de 0.15 libras. a 6 libras, configuración de cambio rápido y mecanizado. Los servicios de valor agregado incluyen pulido, vibración, desbarbado, granallado, pintura, enchapado, revestimiento, ensamblaje y herramientas. Los materiales con los que se trabaja incluyen aleaciones como 360, 380, 383 y 413.
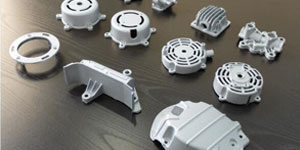
Asistencia en el diseño de fundición a presión de zinc / servicios de ingeniería simultáneos. Fabricante personalizado de piezas fundidas de zinc de precisión. Se pueden fabricar piezas de fundición en miniatura, piezas de fundición a presión de alta presión, piezas de fundición de moldes de deslizamiento múltiple, piezas de fundición de moldes convencionales, piezas de fundición unitaria e independiente y piezas de fundición selladas en cavidades. Las piezas fundidas se pueden fabricar en longitudes y anchos de hasta 24 pulgadas con una tolerancia de +/- 0.0005 pulgadas.
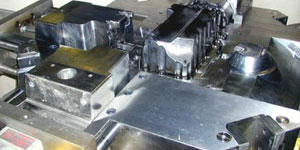
Fabricante certificado por ISO 9001: 2015 de magnesio fundido a presión, las capacidades incluyen fundición a presión de magnesio a alta presión de hasta 200 toneladas de cámara caliente y 3000 toneladas de cámara fría, diseño de herramientas, pulido, moldeado, mecanizado, pintura en polvo y líquida, control de calidad completo con capacidades de CMM , montaje, embalaje y entrega.
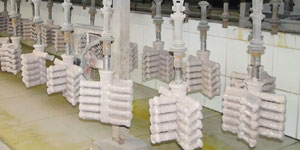
Certificado ITAF16949. El servicio de casting adicional incluye fundición de inversión,moldeo en arena,Fundición por gravedad, Fundición de espuma perdida,Fundición centrífuga,Fundición al vacío,Fundición de molde permanenteLas capacidades incluyen EDI, asistencia de ingeniería, modelado de sólidos y procesamiento secundario.
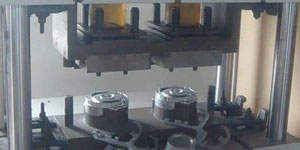
Industrias de fundición Estudios de casos de piezas para: automóviles, bicicletas, aeronaves, instrumentos musicales, embarcaciones, dispositivos ópticos, sensores, modelos, dispositivos electrónicos, carcasas, relojes, maquinaria, motores, muebles, joyas, plantillas, telecomunicaciones, iluminación, dispositivos médicos, dispositivos fotográficos, Robots, Esculturas, Equipos de sonido, Equipos deportivos, Herramientas, Juguetes y más.
¿Qué te podemos ayudar a hacer a continuación?
∇ Ir a la página de inicio para Fundición a presión China
→Piezas de fundición-Descubre lo que hemos hecho.
→ Consejos Ralated Acerca de Servicios de fundición a presión
By Fabricante de fundición a presión Minghe | Categorías: Artículos útiles |Material Tags: Fundición de aluminio, Fundición de zinc, Fundición de magnesio, Fundición de titanio, Fundición de acero inoxidable, Fundición de latón,Fundición de bronce,Casting de video,Historia de la empresa,Fundición a presión de aluminio | Comentarios desactivados