La aplicación de la tecnología de impregnación en la fabricación de motores
El tratamiento de impregnación de piezas fabricadas con materiales ligeros, como cilindros de aluminio, puede reducir eficazmente la tasa de desperdicio de piezas de trabajo y mejorar significativamente su calidad. Con la premisa de garantizar la calidad del producto, pueden reducir efectivamente los costos de fabricación y mejorar la eficiencia de la producción.
Propuesta de tratamiento de impregnación y aligeramiento del motor
El peso ligero se ha convertido en una tendencia en la industria automotriz contemporánea, que está determinada principalmente por la atención mundial a la protección del medio ambiente y el ahorro de energía. Los datos muestran que si el peso propio de un automóvil se reduce en un 10%, su eficiencia de combustible se puede aumentar en un 15%. El aumento de la eficiencia del combustible significa que se reducen el consumo de combustible y las emisiones del automóvil. Por lo tanto, reducir el peso del automóvil es la forma más efectiva de mejorar el ahorro de energía y la protección ambiental del automóvil. El motor es el conjunto grande más crítico de un automóvil, y reducir su peso es crucial para reducir el peso del automóvil.
Desde un punto de vista técnico, hay muchas formas de lograr el peso ligero, como la optimización de toda la estructura de la máquina, los módulos accesorios y el peso ligero, pero el uso de materiales ligeros como plásticos, aleaciones de aluminio y aleaciones de magnesio para reemplazar materiales tradicionales como como hierro fundido es la reducción actual. La forma principal de peso del motor. De hecho, la aleación de aluminio se ha utilizado ampliamente en culatas de cilindros de motor, colectores de admisión y piezas más pequeñas como carcasas de bombas de agua y carcasas de bombas de aceite durante muchos años, y cada vez más empresas han adoptado bloques de cilindros de aleación de aluminio en la última década. Sin embargo, en comparación con el hierro fundido, las piezas de aluminio son más propensas a la flojedad interna, la contracción y los poros durante el proceso de fundición debido a la formación de cristales, contracción y absorción de gas. Estas piezas fundidas defectuosas tienen una capa superficial densa después del mecanizado. El área se elimina, exponiendo así defectos organizativos internos. Para aquellas fundiciones de aluminio que requieren estanqueidad en el motor, al pasar por el proceso de detección de fugas en la línea de producción, la existencia de microporos defectuosos provocará fugas excesivas y producirá productos de desecho, a veces incluso en lotes. Dado que estas condiciones solo se pueden descubrir después de múltiples mecanizados, también causarán un grave desperdicio de horas de trabajo, materias primas y energía. Se puede ver que para resolver el problema de la alta tasa de desperdicio de piezas de fundición de aluminio, se deben tomar ciertas medidas de tratamiento en la producción. En la actualidad, la tecnología más utilizada es el tratamiento de impregnación, es decir, el taponamiento de fugas. La llamada "impregnación" consiste en infiltrar el infiltrante en los microporos de la fundición de aluminio en determinadas condiciones, y después de la solidificación, el relleno infiltrado en el poro y la pared interna del poro de la fundición se conectan en su conjunto a Bloquear los microporos para que las piezas puedan satisfacer una tecnología de proceso requerida para presurización, anti-filtración y anti-filtración.
Proceso de impregnación a presión al vacío
En la actualidad, en la producción de piezas de fundición de aluminio en el país y en el extranjero, se adopta generalmente el método de infiltración por presión de vacío. Este proceso se lleva a cabo principalmente en un tanque de presión de vacío. Según el flujo del proceso, se puede dividir en tres etapas: pretratamiento, tratamiento de impregnación y postratamiento. Sus diversos pasos incluyen principalmente: el pretratamiento también se llama pretratamiento microporoso, que principalmente desengrasa, limpia y seca las piezas fundidas para preparar el siguiente proceso; el primer paso del tratamiento de impregnación es colocar la pieza de trabajo en una canasta Luego colocar la canasta en el tanque de impregnación; aspirar el tanque de impregnación para eliminar el gas en los poros de las piezas; transportar el sellador del tanque de almacenamiento al tanque de impregnación y sumergir las partes que aún están al vacío; Aspire el tanque de impregnación nuevamente para eliminar el gas en el sellador; libere el vacío y presurice el tanque de impregnación con aire comprimido, lo que ayuda a empujar el sellador hacia los poros; libere la presión y devuelva el sellador al tanque de almacenamiento; El posprocesamiento es principalmente para quitar las piezas, centrifugar, enjuagar y completar las operaciones de curado.
El propósito principal del pretratamiento es eliminar manchas de aceite, virutas de metal y polvo en la superficie de las piezas, mejorar la calidad de la impregnación y evitar que el aceite y las impurezas mecánicas ingresen al líquido de impregnación para afectar la penetración y adhesión. Los métodos de desengrasado comúnmente utilizados incluyen el desengrasado con solvente, el desengrasado con lejía y el desengrasado electroquímico. Las piezas fundidas se sacan después del desengrasado y la limpieza antes mencionados, se enjuagan con agua caliente y luego se secan a 80-90 ℃. Para mejorar el efecto de remojo y evitar que entre una gran cantidad de agua en la bomba de vacío, es muy importante secar después de la limpieza.
El tratamiento de impregnación consiste en colocar las piezas de trabajo preprocesadas en el tanque de impregnación para sellar y aspirar, para eliminar completamente el aire y el polvo fino en el tanque y los poros de la fundición, y crear las condiciones dinámicas de diferencia de presión para el llenado y la infiltración. del agente de impregnación. Luego, el infiltrante es aspirado por la presión negativa en el tanque y se vuelve a extraer el vacío. El objetivo del segundo vaciado es descargar el gas en el líquido de impregnación en el tanque para evitar que el líquido de impregnación que contiene el gas penetre en los defectos microporos de la fundición, a fin de evitar la generación de poros durante la solidificación que afecten el sellado. actuación. Finalmente, presurice, de modo que el infiltrante que se ha llenado e infiltrado en los poros del yeso penetre aún más en la parte más profunda de cada parte del defecto. El impregnante es una sustancia líquida preparada a partir de sustancias inorgánicas u orgánicas. En la actualidad, el sellador de metacrilato PC504 / 66 más utilizado se cura con calor y proporciona un relleno de microporos prominente con su baja contracción durante la polimerización. Habilidad, al mismo tiempo, su baja viscosidad ayuda a que el sellador penetre rápida y profundamente en los microporos. El sellador curado puede funcionar normalmente en el rango de -50 ~ 200 ℃.
El postratamiento consiste en gotear la pieza de trabajo, limpiarla y ponerla en un horno de curado para que solidifique, de modo que el infiltrante que ingresa a los poros de la pieza fundida cambie de líquido a sólido para formar una película sólida solidificada. La temperatura de curado generalmente se establece en 80 ~ 90 ℃, o se coloca a temperatura ambiente (por encima de 25 ℃) durante 24 horas. Si la pieza de fundición se utiliza por encima de 300, debe curarse a 80 ℃ durante 2 h, y luego a 110 1 durante XNUMX h.
En cuanto a qué parte del proceso de producción está impregnada, las diferentes plantas de producción y los diferentes tipos de piezas de trabajo son muy diferentes. Un pequeño número de empresas hará normativas uniformes para todas las piezas del sistema de propulsión que requieran una alta precisión de fabricación y estanqueidad: dichas piezas deben estar impregnadas antes del mecanizado, es decir, cuando aún se encuentran en el estado de fundición, para lograr una mejora. El propósito del rendimiento de fundición, prolongar la vida útil de la herramienta durante el mecanizado y garantizar la calidad del producto. Sin embargo, la mayoría de las fábricas todavía adoptan diferentes métodos según los diferentes tipos de piezas. En términos generales, para algunas piezas clave, como el bloque de cilindros de aluminio en el motor, generalmente se requiere impregnar todas las piezas cuando están en el estado de fundición y luego enviarlas. OEM. En cuanto a la impregnación de algunas piezas de trabajo según ciertos criterios después de un determinado proceso en la línea de producción del OEM, depende del proceso de fabricación del OEM.
Para la mayoría de las piezas, generalmente no es necesario impregnarlas cuando están en estado fundido. En cambio, el proceso de impregnación se implementa después de un cierto proceso en el proceso de producción de acuerdo con la situación real. Es decir, cuando las piezas después de varios procesos de mecanizado se confirman que el valor de detección de fugas de algunas piezas está dentro del intervalo especificado, solo se impregna esta parte de la pieza rechazada. En la mayoría de los casos, la proporción de piezas de trabajo rechazadas es muy baja (aproximadamente del 1% al 2%), pero cuando esta proporción excede un cierto límite (dependiendo de la situación específica), el OEM requerirá que la fábrica de piezas en bruto esté impregnada de todas las piezas fundidas. .
También hay algunas piezas que requieren un tratamiento de impregnación que no están incluidas en el proceso de fabricación del OEM por motivos estructurales. Para aquellas piezas cuyos resultados de detección de fugas están fuera de tolerancia, no importa qué tan grande sea el valor medido real, se desecharán directamente. Sin embargo, si el valor de fuga excede la proporción de la pieza de trabajo hasta cierto punto, la fábrica de motores principal también presentará el requisito de un tratamiento de impregnación para todas las piezas en bruto de fundición.
Entonces, ¿dónde está la operación real del tratamiento de impregnación? La práctica común en el país y en el extranjero la llevan a cabo empresas independientes y profesionales. Esto no solo es eficiente y fácil de garantizar la calidad, sino que también el costo es relativamente bajo para la planta de ensamblaje. Sin embargo, también hay algunas fábricas de motores con lotes grandes, ritmo de producción rápido y requisitos de alta calidad del producto. Se abrirá un área cerrada en el taller, para que las fábricas profesionales mencionadas anteriormente dedicadas al tratamiento de impregnación puedan construir una línea de producción de impregnación relativamente única, eficiente y con un mayor grado de mecanización equivale a una sección del taller. Por supuesto, la tasa de operación de esta "sección de trabajo" es menor que la de una línea de producción general.
Realice múltiples definiciones de piezas de trabajo impregnadas
Como todos sabemos, como cuerpo principal del motor, el bloque de cilindros es la parte más grande y pesada entre ellos. Cuando se selecciona la aleación de aluminio, su reducción de peso aproximadamente a la mitad tiene la mayor importancia para el peso ligero del motor. Sin embargo, en vista de la compleja estructura del bloque de cilindros y el número de procesos de mecanizado, en comparación con otras fundiciones de aluminio en el motor, la probabilidad de defectos internos en el bloque de cilindros de aluminio durante el proceso de fundición y conformado también es mayor. Por lo tanto, cómo estandarizar y adoptar de manera eficiente el proceso de infiltración de inmersión para garantizar su calidad también es lo más preocupado por las empresas. A continuación, tomando como ejemplo el cilindro de aluminio, se explica con más detalle el problema de definir y aprobar las piezas a impregnar a través de un caso representativo. Una línea de producción de mecanizado de cilindros de aluminio recién construida en una moderna fábrica de motores de automóvil ha completado todos los procesos de mecanizado en bruto antes de que la pieza de trabajo ingrese a la estación de limpieza intermedia. Antes de la siguiente instalación de la tapa del cojinete principal y las posteriores operaciones de acabado, se instaló una estación de prueba de sellado. Además de la detección de fugas del paso de aceite de baja presión, paso de agua y paso de aceite de alta presión del bloque de cilindros de aluminio, esta estación también es equivalente a instalar una compuerta. De acuerdo con el valor de fuga medido, es necesario determinar si este El cilindro de aluminio está impregnado.
Para la pieza de trabajo, se establecen dos límites de cribado: el primero es la tasa de fuga de la pieza inspeccionada, tomando como ejemplo el canal de aceite de baja presión, el límite de la tasa de fuga es 30 CC / min; el segundo límite de cribado es Esta parte inspeccionada tiene como objetivo determinar si existe una fuga en el cilindro de aluminio, pero si es posible y necesario remediarla mediante un tratamiento de impregnación. Tomando como ejemplo el paso de aceite de baja presión, la tabla indica que es de 500 CC / min. En vista de esto, cuando el cuerpo del cilindro de aluminio después del proceso de limpieza intermedia ingresa a la estación de prueba de sellado a lo largo de la pista de transporte, si alguno de los valores de fuga medidos de la pieza de trabajo es menor que el límite de cribado correspondiente dado en la tabla, que es decir, la tasa de fuga se considerará calificada y luego pasará al siguiente proceso. Pero siempre que cualquiera de los valores de fuga medidos reales exceda su tasa de fuga pero sea menor que el límite de desperdicio, tome el paso de aceite de baja presión en la tabla como ejemplo, el rango está entre 30 y 500CC / min. El bloque de cilindros de aluminio se trata como una pieza de trabajo que debe sacarse para un tratamiento de impregnación, enviarse por la pista de rodadura en la dirección inversa, y luego retirarse manualmente y enviarse. En cuanto a un número muy pequeño de piezas de trabajo cuyo valor de fuga medido ha alcanzado o incluso superado el límite de desechos de la tabla, fluirán a través de la pista de rodadura del transportador. El proceso de detección, cribado y desvío mencionado anteriormente lo realiza el robot en la estación de prueba de sellado.
En resumen, después del tratamiento de impregnación de cilindros de aluminio y otras partes, no solo se reduce la tasa de desperdicio y se mejora significativamente la calidad, sino que también se reduce el costo de fabricación bajo la premisa de garantizar la calidad y se mejora la productividad de manera efectiva. Por lo tanto, en el proceso de que la industria de motores de automóviles contemporánea se vuelve cada vez más liviana, el uso científico y razonable de la tecnología de infiltración es la mejor solución para resolver por completo los problemas inherentes de las aleaciones de aluminio y otras piezas fundidas de materiales ligeros (como defectos como los microporos).
Conserve la fuente y la dirección de este artículo para reimprimir:La aplicación de la tecnología de impregnación en la fabricación de motores
Minhe Empresa de fundición a presión se dedican a fabricar y proporcionar piezas de fundición de calidad y alto rendimiento (la gama de piezas de fundición a presión de metal incluye principalmente Fundición a presión de pared delgada,Fundición a presión en cámara caliente,Fundición a presión de cámara fría), Servicio redondo (servicio de fundición a presión,Mecanizado cnc,Fabricación de moldes, Tratamiento de superficie) .Cualquier fundición a presión de aluminio personalizada, fundición a presión de magnesio o Zamak / zinc y otros requisitos de fundición pueden contactarnos.
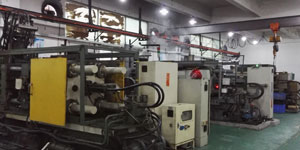
Bajo el control de ISO9001 y TS 16949, todos los procesos se llevan a cabo a través de cientos de máquinas de fundición a presión avanzadas, máquinas de 5 ejes y otras instalaciones, que van desde desintegradores hasta lavadoras Ultra Sonic.Minghe no solo cuenta con equipos avanzados, sino que también cuenta con profesionales equipo de ingenieros, operadores e inspectores experimentados para hacer realidad el diseño del cliente.
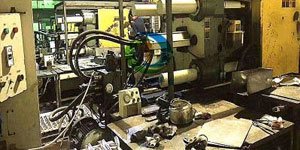
Fabricante por contrato de piezas de fundición a presión. Las capacidades incluyen piezas de fundición a presión de aluminio de cámara fría de 0.15 libras. a 6 libras, configuración de cambio rápido y mecanizado. Los servicios de valor agregado incluyen pulido, vibración, desbarbado, granallado, pintura, enchapado, revestimiento, ensamblaje y herramientas. Los materiales con los que se trabaja incluyen aleaciones como 360, 380, 383 y 413.
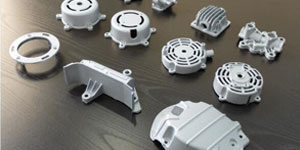
Asistencia en el diseño de fundición a presión de zinc / servicios de ingeniería simultáneos. Fabricante personalizado de piezas fundidas de zinc de precisión. Se pueden fabricar piezas de fundición en miniatura, piezas de fundición a presión de alta presión, piezas de fundición de moldes de deslizamiento múltiple, piezas de fundición de moldes convencionales, piezas de fundición unitaria e independiente y piezas de fundición selladas en cavidades. Las piezas fundidas se pueden fabricar en longitudes y anchos de hasta 24 pulgadas con una tolerancia de +/- 0.0005 pulgadas.
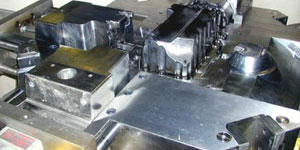
Fabricante certificado por ISO 9001: 2015 de magnesio fundido a presión, las capacidades incluyen fundición a presión de magnesio a alta presión de hasta 200 toneladas de cámara caliente y 3000 toneladas de cámara fría, diseño de herramientas, pulido, moldeado, mecanizado, pintura en polvo y líquida, control de calidad completo con capacidades de CMM , montaje, embalaje y entrega.
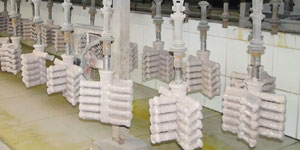
Certificado ITAF16949. El servicio de casting adicional incluye fundición de inversión,moldeo en arena,Fundición por gravedad, Fundición de espuma perdida,Fundición centrífuga,Fundición al vacío,Fundición de molde permanenteLas capacidades incluyen EDI, asistencia de ingeniería, modelado de sólidos y procesamiento secundario.
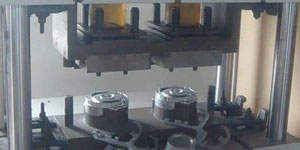
Industrias de fundición Estudios de casos de piezas para: automóviles, bicicletas, aeronaves, instrumentos musicales, embarcaciones, dispositivos ópticos, sensores, modelos, dispositivos electrónicos, carcasas, relojes, maquinaria, motores, muebles, joyas, plantillas, telecomunicaciones, iluminación, dispositivos médicos, dispositivos fotográficos, Robots, Esculturas, Equipos de sonido, Equipos deportivos, Herramientas, Juguetes y más.
¿Qué te podemos ayudar a hacer a continuación?
∇ Ir a la página de inicio para Fundición a presión China
→Piezas de fundición-Descubre lo que hemos hecho.
→ Consejos Ralated Acerca de Servicios de fundición a presión
By Fabricante de fundición a presión Minghe | Categorías: Artículos útiles |Material Tags: Fundición de aluminio, Fundición de zinc, Fundición de magnesio, Fundición de titanio, Fundición de acero inoxidable, Fundición de latón,Fundición de bronce,Casting de video,Historia de la empresa,Fundición a presión de aluminio | Comentarios desactivados